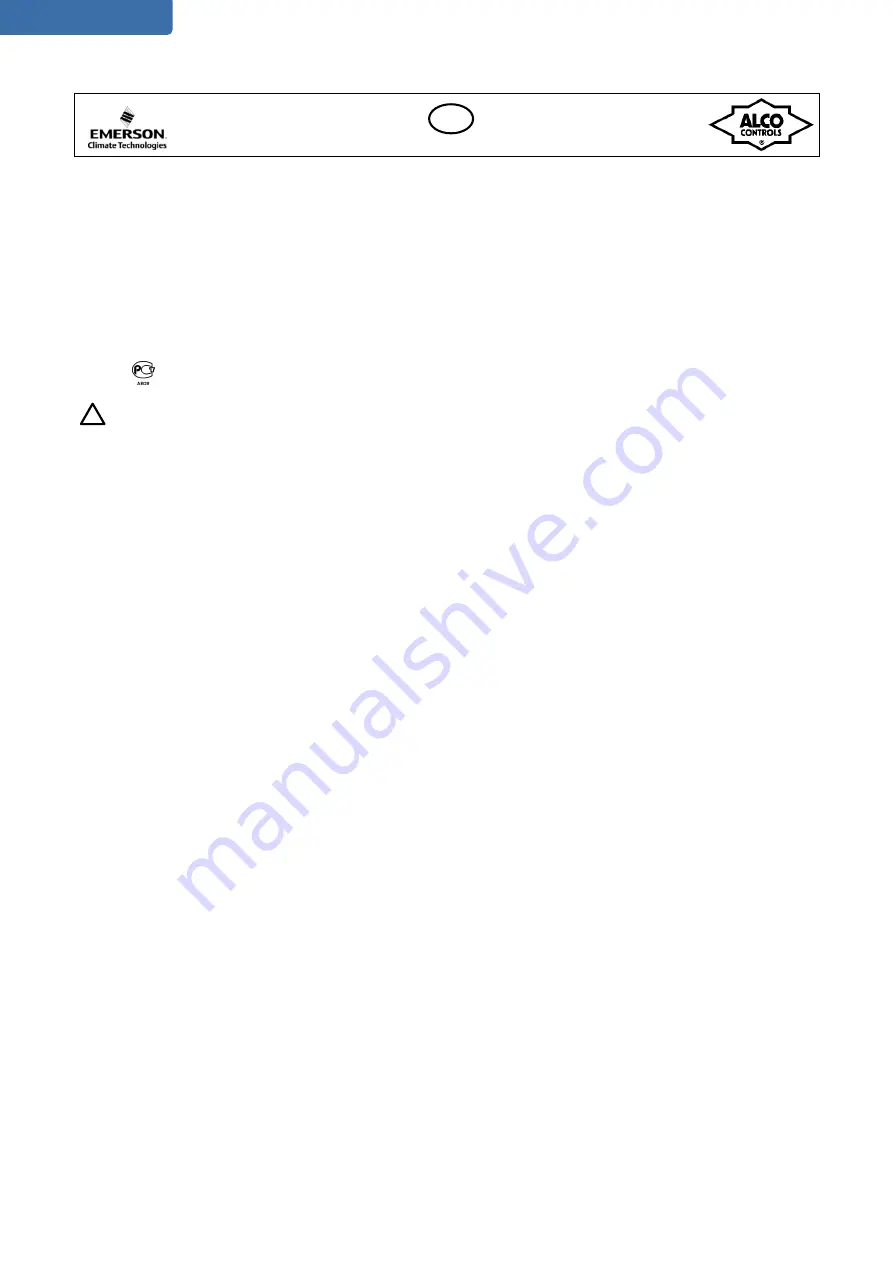
CPHE_65008__R05
Replacement for 04
Operating Instructions
Pressure Regulator
CPHE and ACP
Description and Technical Data:
Regulators are used to avoid permanent on/off
cycling of compressor or to keep evaporating
temperatures above certain levels
•
Can be installed in any position.
•
Intended for use with CFC, HCFC, HFC
•
Adjustable from: CPHE -0,4 to 5 bar
•
ACP: 0 to 5 bar
•
Factory setting:
CPHE: 1,4 bar
•
ACP: 2,7 bar
•
Max. allowable pressure PS: CPHE: 35 bar
•
ACP 31 bar
•
Medium temperature range TS: -40°C to 120°C
•
Ambient temperature range: -40 to 50°C
•
Transport temperature range: -40 to 70°C
•
Marking:
•
Safety Instructions:
•
Read installation instructions thoroughly.
Failure to comply can result in device failure,
system damage or personal injury.
•
It is intended for use by persons having the
appropriate knowledge and skill. Before
attempting to install the regulator, make sure
pressure in system is brought to and remains at
atmospheric pressure.
•
Do not release any refrigerant into the
atmosphere.
•
Do not use any other fluid media without prior
approval of Alco Controls. Use of fluid not
listed could result in change of Hazard
Category of the product and consequently
change of conformity assessment requirement
for product in accordance with European
Pressure Equipement Directive 97/23/EC.
•
In a severely contaminated system, avoid
breathing acid vapours and avoid contact with
skin from contaminated refrigerant / lubricants.
Failure to do so could result in skin injury.
•
CPHE and ACP are not released for use with
flammable refrigerants such as hydrocarbon
refrigerants and ammonia.
•
The CPH(E) regulator’s power assembly and
cage assembly must be removed before
soldering.
Installation and Mounting:
Two typical installation applications are possible:
Hot Gas Bypass to the evaporator inlet (with up to
100% of capacity control) per Fig. 1
Hot Gas Bypass to the suction line (max. 40% of
capacity control
because of oil return
capability) per Fig. 2
•
Pressure regulators can be installed in any position.
•
Direction of flow must match arrow on body.
•
Before brazing clean tubing.
•
CPHE:
Remove power assembly and cage before
brazing.
•
ACP:
Do not disassemble valve before brazing.
•
Use wet rags or chill blocks when brazing to
prevent valve damage.
Do not
Direct flame away from valve body (Fig. 3).
Use an inert gas such as nitrogen to pass through
the valve to prevent
•
The use of appropriate brazing material is required
(soft solder is not allowed).
•
Never use
•
Internal parts must be protected from foreign
material and moisture. ALCO filter
liquid line and ALCO filter use in suction line is
recommended.
•
Install the external equalizer line to the compressor
suction line alw
pressure regulators. NEVER join the equalizer line
with another control except of the Liquid Injection
Valve.
Setting:
If desired set point differs from factory setting,
follow the procedure for setting before any
installatio
below
The function of the CPHE and ACP series regulators
is to prevent the suction pressure from falling below
a predetermined set point, thereby balancing the
system. Therefore, the first step after installation is
to determine this set point for the minimum suction
pressure allowable for your application. To do so,
follow this procedure:
•
Start the system and determine if it is operating
properly. Install a gauge on the compressor suction
line and measure the suction
system has stabilized. To make sure, that hot gas is
not bypassed de
•
Remove the seal cap (1) and turn the power
assembly adjusting stem (2) full
COUNTERCLOCKWISE.
•
Reduce the evaporator load until the sucti
pressure lowers to the point at which bypass is
desired.
•
Energize hot gas solenoid to enable gas flow.
•
Turn the power assembly adjusting stem on top of
the regulator in a CLOCKWISE direction until
bypass occurs and suction pressure does not fall
below t
CLOCKWISE turn of the adjusting stem will
increase the pressure setting; a
COUNTERCLOCKWISE turn will decrease it.
Adjustments should be made in small increments,
allowing the system to stabilize after each turn.
Do not
regulator (only CPHE). This screw should only be
used when working in a vacuum temperature range
•
Vary evaporator load to test at various conditions
that the suction pressure does not fall below the
predetermined set point
•
CPHE: Replace the seal cap (1) on the adjusting
stem (Fig 4).
•
ACP: replace plastic cap
!
Replacement for 04
Date: 20.06.2013
DWG Nr.: CPH EZ 005000/PCN 863003
Operating Instructions
Pressure Regulator
CPHE and ACP
GB
Emerson Climate Technologies GmbH
Holzhauser Str. 180 - D-13509 Berlin
Germany
www.emersonclimate.eu
Use wet rags or chill blocks when brazing to
prevent valve damage.
Do not
exceed max. body temperature of 120°C.
Direct flame away from valve body (Fig. 3).
Use an inert gas such as nitrogen to pass through
the valve to prevent copper oxide formation.
The use of appropriate brazing material is required
(soft solder is not allowed).
Never use oxygen or flammable gases.
Internal parts must be protected from foreign
material and moisture. ALCO filter-drier use in
liquid line and ALCO filter use in suction line is
recommended.
Install the external equalizer line to the compressor
suction line always downstream from evaporator
pressure regulators. NEVER join the equalizer line
with another control except of the Liquid Injection
Valve.
Setting:
If desired set point differs from factory setting,
follow the procedure for setting before any
installation and/or refer to the Adjustment Table
below:
The function of the CPHE and ACP series regulators
is to prevent the suction pressure from falling below
a predetermined set point, thereby balancing the
system. Therefore, the first step after installation is
to determine this set point for the minimum suction
pressure allowable for your application. To do so,
follow this procedure:
Start the system and determine if it is operating
properly. Install a gauge on the compressor suction
line and measure the suction pressure after the
system has stabilized. To make sure, that hot gas is
not bypassed de-energize the hot gas solenoid.
Remove the seal cap (1) and turn the power
assembly adjusting stem (2) full
COUNTERCLOCKWISE.
Reduce the evaporator load until the suction
pressure lowers to the point at which bypass is
desired.
Energize hot gas solenoid to enable gas flow.
Turn the power assembly adjusting stem on top of
the regulator in a CLOCKWISE direction until
bypass occurs and suction pressure does not fall
below the predetermined set point. A
CLOCKWISE turn of the adjusting stem will
increase the pressure setting; a
COUNTERCLOCKWISE turn will decrease it.
Adjustments should be made in small increments,
allowing the system to stabilize after each turn.
Do not
turn adjustment screw on the side of the
regulator (only CPHE). This screw should only be
used when working in a vacuum temperature range
Vary evaporator load to test at various conditions
that the suction pressure does not fall below the
predetermined set point.
CPHE: Replace the seal cap (1) on the adjusting
stem (Fig 4).
ACP: replace plastic cap
NOTES:
•
On multiple evaporator systems, do not pipe hot
gas to more than one evaporator. Use separate
bypass regulators or consult the ALCO
Applications Engineering De
•
If the compressor is located above the evaporator,
bypass should be piped to the evaporator to insure
proper oil return during low load bypass
conditions.
•
On a long piping run, bypass to the evaporator,
insulate the bypass to prevent condensate.
Condensate can lead to unstable conditions and
or flooding of the compressor.
Solenoid Connections
•
If a compressor discharge line thermostat is used,
it is recommended that the solenoid
series with the thermostat.
•
Voltage and frequency of the c
to the power source. Connect leads to the power
source.
(NEVER wire on the load side of the motor
starter.)
Note 1: For installation of a Liquid Injection Valve
(e.g. L-series), refer to ALCO’s catalog for selection
and see the Superheat Table below.
Note 2: If a liquid-injection solenoid valve is used,
the electrical connections should be in parallel with
the hot gas solenoid valve.
Leakage test:
•
After completion of installation, a pressure test
must be carried out as follows:
•
- According to EN378 for systems which must
comply with European pressure equipment
directive 97/23/EC.
•
- To maximum working pressure of system for
other applications.
Warning:
•
Failure to do so could result in loss of refrigerant
and personal injury.
•
The pressure test must be conducted by skilled
persons with due respect regarding the danger
related to pressure.
Service:
•
Before any service shut down system and
disconnect from power source.
•
Fully depressurize regulator. After reducing
pressure to atmospheric
be opened, internal parts removed, cleaned and
replaced, per Fig.4. Install parts in reverse
sequence as removed.
•
Replace gaskets 4, 6 and 7 before reassembling the
regulator.
•
Tighten capscrews evenly to torque specification
35 Nm.
DWG Nr.: CPH EZ 005000/PCN 863003
Emerson Climate Technologies GmbH
13509 Berlin
On multiple evaporator systems, do not pipe hot
gas to more than one evaporator. Use separate
bypass regulators or consult the ALCO
Applications Engineering Department.
If the compressor is located above the evaporator,
bypass should be piped to the evaporator to insure
proper oil return during low load bypass
On a long piping run, bypass to the evaporator,
insulate the bypass to prevent condensate.
Condensate can lead to unstable conditions and
or flooding of the compressor.
Solenoid Connections
If a compressor discharge line thermostat is used,
it is recommended that the solenoid is wired in
series with the thermostat.
Voltage and frequency of the coil must correspond
to the power source. Connect leads to the power
(NEVER wire on the load side of the motor
Note 1: For installation of a Liquid Injection Valve
series), refer to ALCO’s catalog for selection
eat Table below.
injection solenoid valve is used,
the electrical connections should be in parallel with
the hot gas solenoid valve.
After completion of installation, a pressure test
must be carried out as follows:
According to EN378 for systems which must
comply with European pressure equipment
97/23/EC.
To maximum working pressure of system for
other applications.
Failure to do so could result in loss of refrigerant
and personal injury.
ressure test must be conducted by skilled
persons with due respect regarding the danger
related to pressure.
Before any service shut down system and
disconnect from power source.
Fully depressurize regulator. After reducing
pressure to atmospheric only CPHE regulator may
be opened, internal parts removed, cleaned and
replaced, per Fig.4. Install parts in reverse
sequence as removed.
Replace gaskets 4, 6 and 7 before reassembling the
Tighten capscrews evenly to torque specification