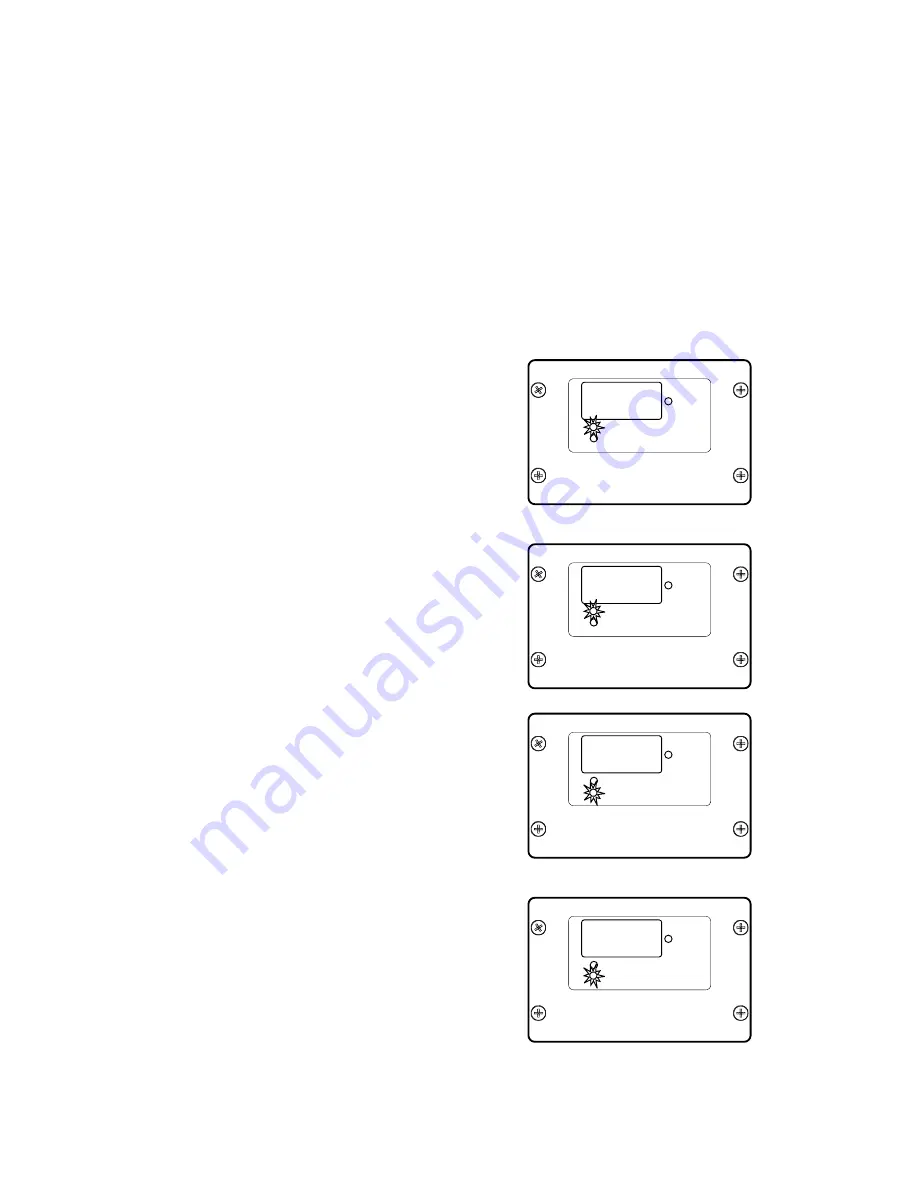
26
1. Programming Upper RPM Limit (Ceiling):
• Press mode button twice. Digital readout will
display current upper limit setting. This repre-
sents the RPM at which the Rapid Recovery
Auto Reverse will re-start the feed rolls after
a suspension.
•
Oil Use indicator will flash. Increase or de
-
crease setting using program buttons (factory
setting is 1375 RPM)
2. Programming Upper Flow Percentage:
• Press mode button once more. Digital read-
out will display current upper flow setting. This
represents the percent of hydraulic flow that
will be sent to the feed rolls (Feed speed.).
•
Oil Use indicator will flash. Increase or de
-
crease setting using program buttons, do not
set above 80 % (factory setting is 75%)
3. Programming Lower RPM Limit (Floor) :
• Press mode button once more. Digital rea-
dout will display current lower limit setting.
This represents the rotor RPM at which the
Rapid Recovery Auto Reverse will reverse
and suspend the feed rolls.
•
Machine hours indicator will flash. Increase
or decrease setting using program buttons.
(factory setting is 900 RPM)
4. Programming Lower Flow Percentage:
• Press mode button once more. Digital read-
out will display current lower flow setting. This
represents the percent of hydraulic flow that
will be sent to the feed rolls (Feed speed.).
•
Machine hours indicator will flash. Increase
or decrease setting using program buttons,
do not set below 25% (factory setting is 35%)
8888
ROTOR
R. P. M.
OIL USE HOURS
MACHINE HOURS
EMB MFG INC.
8888
ROTOR
R. P. M.
OIL USE HOURS
MACHINE HOURS
EMB MFG INC.
8888
ROTOR
R. P. M.
OIL USE HOURS
MACHINE HOURS
EMB MFG INC.
8888
ROTOR
R. P. M.
OIL USE HOURS
MACHINE HOURS
EMB MFG INC.
1
375
88
75
0
900
88
35
4.4.2 INTELLIFEED PROGRAMMING:
The factory settings provide good overall performance for the CR70, however you may under certain
circumstances, choose to customize performance. (controller is accessible through the battery access
door.) Programmable features of Intellifeed include: the upper and lower RPM limits (rotor speed) and
the upper and lower flow percentage (roller speed).
How best to adjust the programming will come from experience and common sense, if in doubt set to
factory setting for optimum performance.
Here are some helpful hints:
•
For heavier brush, decrease the upper flow percentage for slower feed speed.
•
For lighter brush, increase the upper flow percentage for faster feed speed.
•
If the chipper is stalling before the feed rolls stop, increase the rotor floor setting.
•
If you prefer more aggressive feeding with faster feed and more stops, increase the lower flow
percentage.
Содержание Wallenstein CR Series
Страница 69: ...69 ...