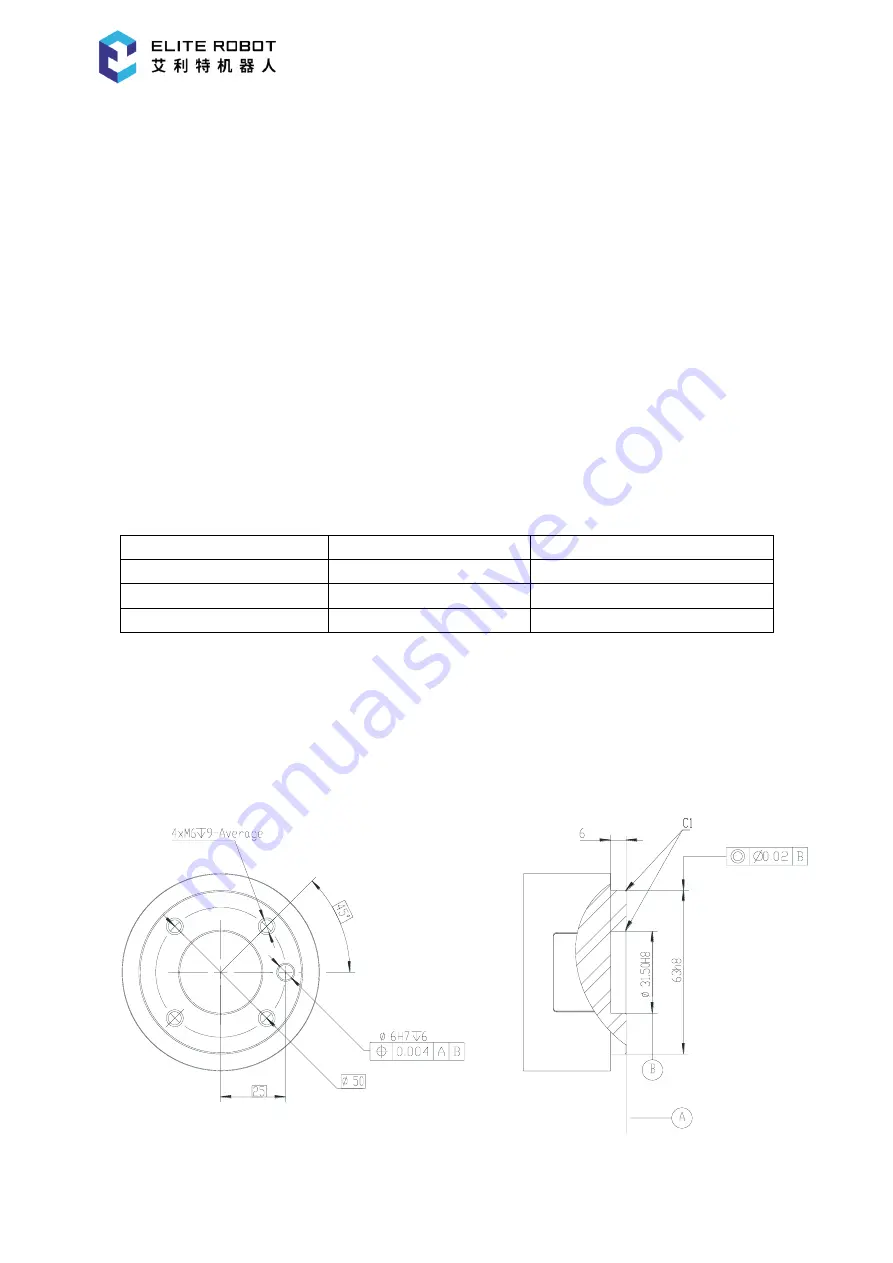
Page 29 of 130
Doc No.
:
T202001005
from vibration. If the robot is installed on a moving platform, an acceleration of the moving platform
should be very low, and a high acceleration would trigger the collision stop function of the robot.
2. The user is recommended to use a base contact surface with strong heat dissipation
performance, such as all-aluminium material. When the operating temperature is greater than 35°C,
the user is strongly recommended to use the material with strong heat dissipation performance.
Make sure the robot arm is correctly and securely installed in place.
If soaked in water for more than a certain period of time, the robot may be damaged. The robot
should not be installed in water or the humid place unless IP67 protection class is declared.
Danger of overturning: if not securely placed on the hard surface, the robot may overturn and
cause damage.
Installation Requirements of the Robot Arm:The robot arm having a 6KG load runs normally
without bumping against the outside, in which a center of gravity of the load is deviated from a
central axis of the tool end for 100mm. Three ways of installation (forward installation, hoisting and
vertical installation) are available, and it is recommended that the minimum anti-overturning force
should be available at each hole position of fixing the bolt of the robot arm.
Way of installation
Normal running
Stopping in case of emergency
Forward installation
1554N±360N
1554N±2594N
Reverse installation
1754N±360N
1754N±2594N
Vertical installation
1554N±360N
1554N±2594N
6.5 Installation of the End/Tool Effector
The tool flange has four M6 threaded holes and one Ф6 positioning hole, in this way the clamp
may be conveniently installed and connected to the robot end. The mechanical dimensions of the tool
flange are shown in Figure 6-5.
Figure 6-5 Mechanical dimensions diagram of the tool flange of the robot, with unit of mm