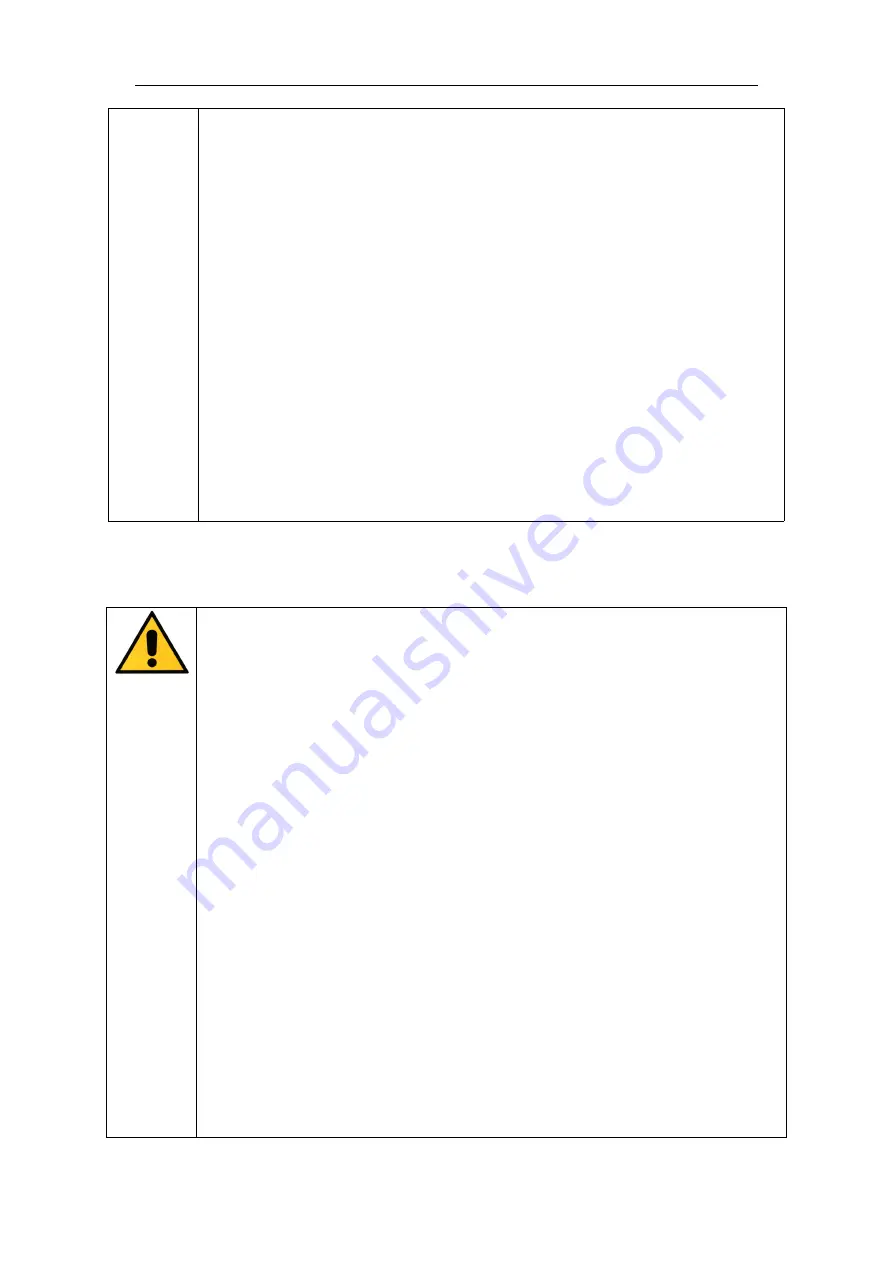
Electrical Operation and Maintenance Manual for ER15-1400 Industrial Robot
8
met and no humans or obstacles left are around the robot or within the safety fence.
9. During teaching, please confirm the motion range of the robot. Approaching the
underside of the robot is prohibited and may pose risks causing accidents. It’s also
worth noticing that it is forbidden to approach the robot arms to prevent risks of
workpiece falling when robot’s claws grip workpieces.
10. For safety concern, the maximum speed of the robot is limited to 250mm/s (safe
operating speed) in teaching or inspection mode. However, after teaching is
completed or robot is recovered from errors, the operator should set the speed as low
as possible in verifying teaching data.
11. In the teaching process, both the operator and the supervisor should continuously
monitor the robot for abnormal movements, possible collisions and squeezing points
on and around the robot. Meanwhile, please confirm the safe passage for the operator
is clear in case of emergency evacuation.
12. Please set the robot's software limit beyond the robot’s motion range after
teaching is completed. Refer to the EFORT Industrial Robot Operation Manual for
the setting.
1.3.6 Safety in Automatic Operation
Danger
Because teaching program repeats fast, please strictly follow the precautions below
and refer to national/international standards.
The design of safety functions should comply with Robot Safety Requirements
(GB11291.1-2011/ISO10218-1:2006).
Please confirm all switches function properly before repair.
1.Please read and understand all manuals, specifications, and other relevant
documents provided by EFORT before operation. In addition, completely understand
procedures of operation, teaching, and maintenance. Meanwhile, make sure all safety
measures are effective in place.
2. In automatic operation, any part of the body should never enter the safety fence.
Please confirm no humans or obstacles left are within the safety fence before starting
operation.
3. In automatic operation, the robot may seem to stop while waiting for the delay of
the timer or external signal input. However, do not approach it at this time because it
immediately resumes operation when the two conditions mentioned above are met.
4. In automatic operation, this situation will be extremely dangerous: if the gripping
force of the workpiece is not enough, the workpiece may be thrown off during the
movement of the robot. Be sure to confirm that the workpiece has been firmly
grasped. When the workpiece is grasped by a pneumatic gripper, an electromagnetic