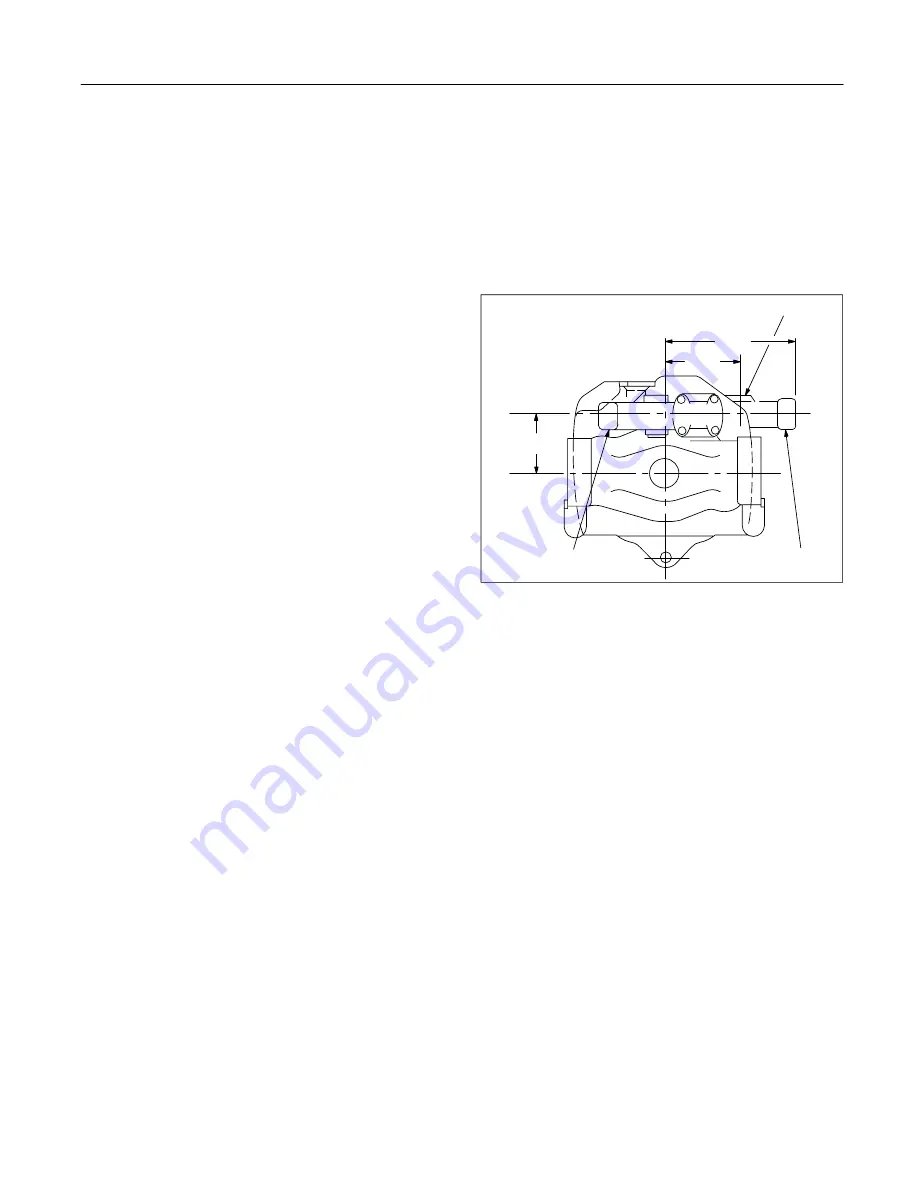
13
Sound Level
Noise is only indirectly affected by the fluid selection, but the
condition of the fluid is of paramount importance in obtaining
optimum reduction of system sound levels.
Some of the major factors affecting the fluid conditions that
cause the loudest noises in a hydraulic system are:
1. Very high viscosities at start-up temperatures can
cause pump noises due to cavitation.
2. Running with a moderately high viscosity fluid will
impede the release of entrained air. The fluid will not be
completely purged of such air in the time it remains in the
reservoir before recycling through the system.
3. Aerated fluid can be caused by ingestion of air
through the pipe joints of inlet lines, high velocity discharge
lines, cylinder rod packings, or by fluid discharging above the
fluid level in the reservoir. Air in the fluid causes a noise
similar to cavitation.
F. Overload Protection
Relief valves limit pressure in the system to a prescribed
maximum and protect components from excessive pressure.
The setting of the relief valve depends on the work
requirements of the system components.
H. Start-Up
Before starting pump the case MUST be filled with clean
hydraulic fluid.
With a minimum drive speed of 650 rpm, a pump should
prime almost immediately if provision is made to initially
purge the air from the system.
Failure to prime within a reasonable length of time may result
in damage due to lack of lubrication. Inlet lines must be tight
and free from air leaks. However, it may be necessary to crack
a fitting on the outlet side of the pump to purge trapped air.
Figure 7. C/CV/CVP Compensator Positions for Right and
Left Hand Shaft Rotation
2.19
5.18
2.94
Compensator Position
for L.H. Rotation
Compensator Position
for R.H. Rotation
Load Sensing Control Port Location for L.H. Rotation