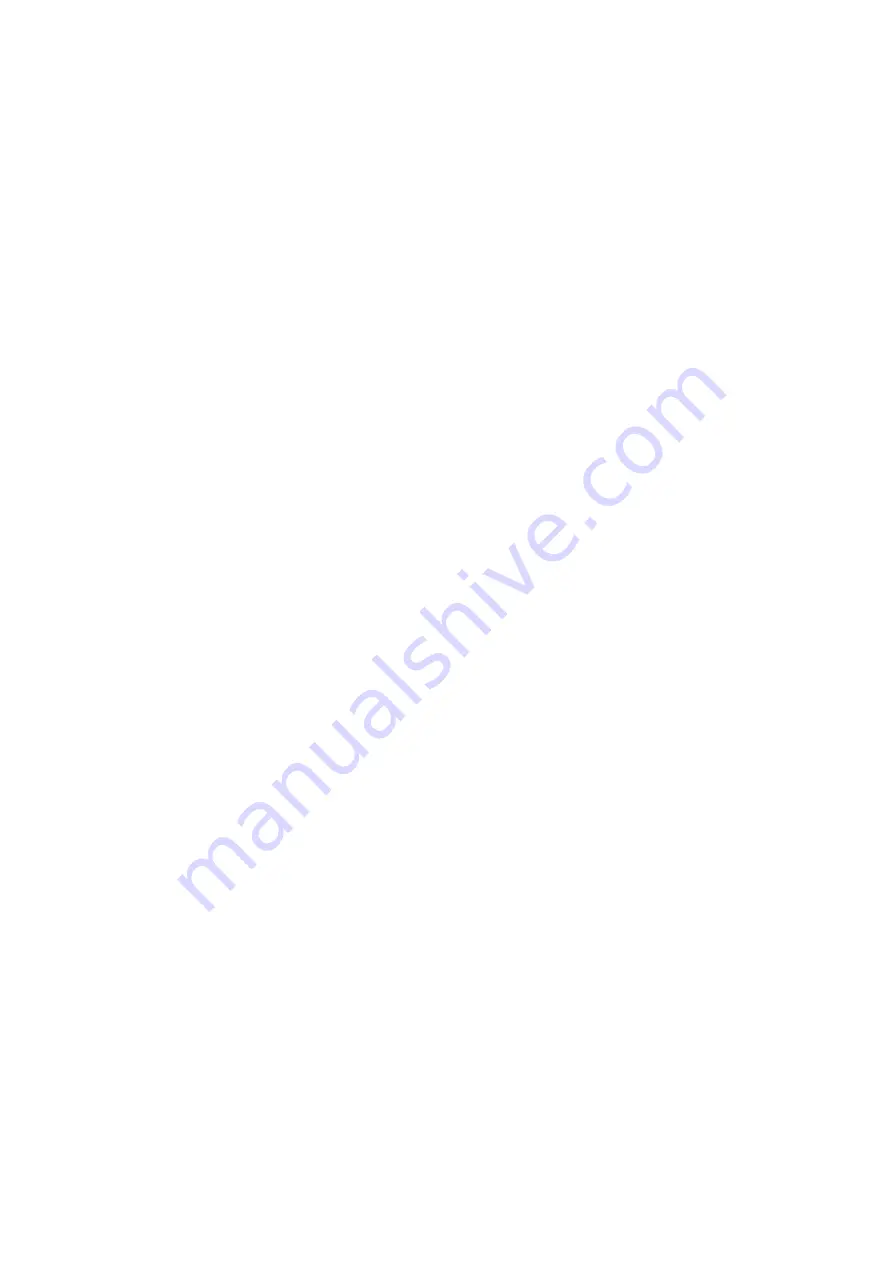
2 Engineering
2.9 Three-phase motors
DB1 variable frequency drive
11/20 MN040031EN
Eaton.com
48
2.9.5 Synchronous reluctance motor (SyncRM)
Synchronous reluctance motors have the same configuration as a three-
phase asynchronous motor. In order to prevent eddy currents, their rotor is
made of a soft magnetic material such as electrical steel, and in general
terms can have one of two different sheet cross-sections.
In the case of reluctance motors intended to be run as mains-connected
systems, the rotor additionally features a rotor cage (similar to that used in
asynchronous motors). This cage makes it possible for the motor to start
asynchronously on the mains until it synchronizes (“falls into step”) to it and
is able to follow the rotating field.
In the case of reluctance motors with a rotor that features salient poles with
flux directing sections and flux barrier sections, a variable frequency drive
with sensorless vector control is required (DC1-…E1). This combination
makes it possible to have a rotor speed that is synchronous with the rotating
field and achieve optimum operation even when there are load changes.
The losses in the rotor are virtually negligible here.
Compared to a standard asynchronous motor, this synchronous reluctance
motor is more effective and achieves international efficiency standard IE4.
These are primarily used in rotating equipment in process engineering invol-
ving pumps, fans, compressors, and turbines, as well as mixers, centrifuges,
and conveyor systems.
→
In order to use vector control with brushless DC motors, the
values for parameters P-60, P-61, and P-62 on DB1 variable
frequency drives need to be changed:
•
Change the value for P-60 to 3 ("Brushless DC motor speed
control").
•
Change the value for P-61 to 1 (“Motor identification”).
Automatic autotune to determine the motor parameters
when the motor is stationary.
•
P-62 (“MSC gain”). Adjust the gain factor for the speed
controller.
→
In order to use vector control with synchronous reluctance
motors, the values for parameters P-60, P-61, and P-62 on DB1
variable frequency drives need to be changed:
•
Change the value for P-60 to 4 (“SyncRel motor speed con-
trol”).
•
Change the value for P-61 to 1 (“Motor identification”).
Automatic autotune to determine the motor parameters
when the motor is stationary.
•
P-62 (“MSC gain”): Adjust the gain factor for the speed
controller.