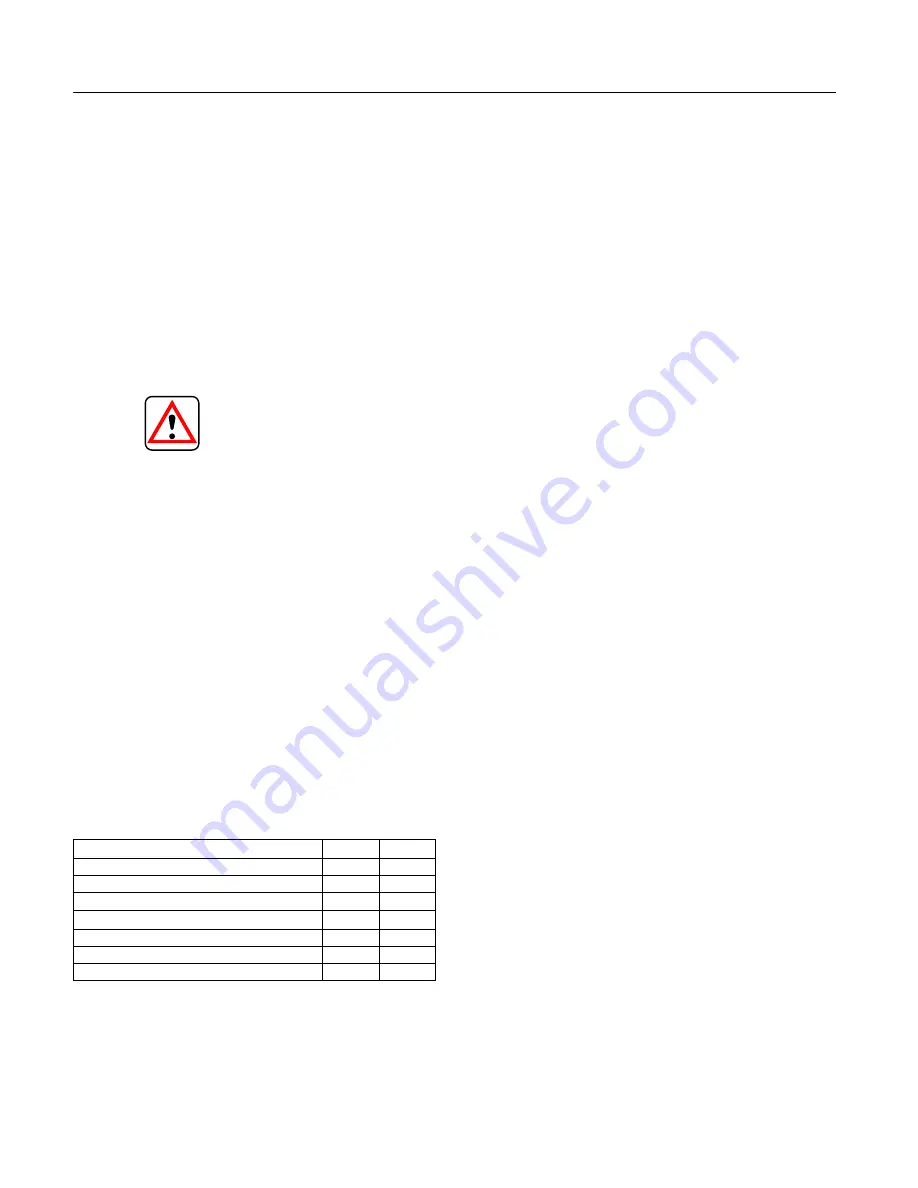
24
Section VI – Installation
A. Installation Drawings
The installation drawings listed in Table 1 show installation
dimensions, port locations and operating parameters. Man-
ifold, subplate and bolt kit information is also included.
NOTE
Detent valves must be installed with the valve spool
in the horizontal position for good machine
reliability. The mounting position of spring offset and
spring centered models is unrestricted.
NOTE
Make sure the “Y” drain port is piped directly to the
tank. Back pressure cannot be tolerated at this
valve port.
CAUTION
On solenoid operated directional valves make sure
an electrical ground is connected to the valve. This
prevents the possibility of a shock hazard if a coil
develops a short circuit to the frame.
B. Fluids and Seals
Standard seals (Nitrile) can be used with petroleum,
water-glycols, and water-oil emulsion type fluids.
F1 seals (Butyl, EPR) must be used for alkyl phosphate-es-
ter base fluids and aircraft type fire-resistant fluids. F1 seals
cannot be used with petroleum or phosphate ester-hydrocar-
bon blends.
F3 seals (Viton*) can be used with all commonly used
industrial hydraulic fluids. Viton* is compatible with
petroleum, water-base and synthetic fire-resistant fluids.
*Trademark of Dupont DeNemours Co., Inc.
Fluid Type
Skydrol
Yes
No
Pydraul 10-E
Yes
No
Pydraul 29-E-L-T, 50-E, 65-E, 115-E
Yes
Yes
Pydraul 230-C, 312-C, & 540-C
No
Yes
Fyrquel & Fyrlube
Yes
Yes
Fyrtek
No
Yes
Houghto Safe 1000 Series
Yes
Yes
The following table summarizes the compatibilities of the
most common phosphate ester fluids.
F3
F1
C. Piping and Tubing
1. All pipes and tubing must be thoroughly cleaned
before installation. Recommended cleaning methods are
sandblasting, wire brushing and pickling. Refer to instruction
sheet 1221-S for pickling instructions.
2. To minimize flow resistance and the possibility of
external leakage, use only the necessary fittings and con-
nections required for proper installation.
3. The number of bends in tubing should be kept to a
minimum to prevent excessive turbulence and friction of fluid
flow. Tubing must not be bent too sharply. The recom-
mended radius for tube bends is three times the inside
diameter.
D. Hydraulic Fluid Recommendations
Hydraulic fluid within the system performs the dual function
of lubrication and transmission of power. To insure proper
lubrication, system life, and component reliability, fluid
selection should be made carefully with the assistance of a
reputable supplier. Fluid selection should be acceptable for
use with all valves, motors and pumps within the system.
Data sheets for fluid selection are available from your local
Sales or Engineering representative to order data sheet
I-286-S.
The fluid recommendations noted in the data sheet are
based on our experience in industry as a hydraulic
component supplier. Where special considerations indicate a
need to depart from these recommendations, see your sales
representative.
E. Cleanliness
To insure your hydraulic system is clean, perform the
following steps:
1. Clean (flush) the entire system to remove paint, metal
chips, welding shot, etc.
2. Filter each oil change to prevent introduction of
contaminants.
3. Provide continuous oil filtration to remove sludge,
products of wear and corrosion generated during the life of
the system.
4. Provide protection to all areas that can introduce
airborne contaminants into the system.
5. Perform regular servicing procedures of filters,
breathers, and reservoirs.
F. Overload Protection
A relief valve must be installed in the system as close to the
pump as possible. The relief valve limits pressure in the
system to a prescribed maximum. The setting of the relief
valve depends on the work requirements of the system.