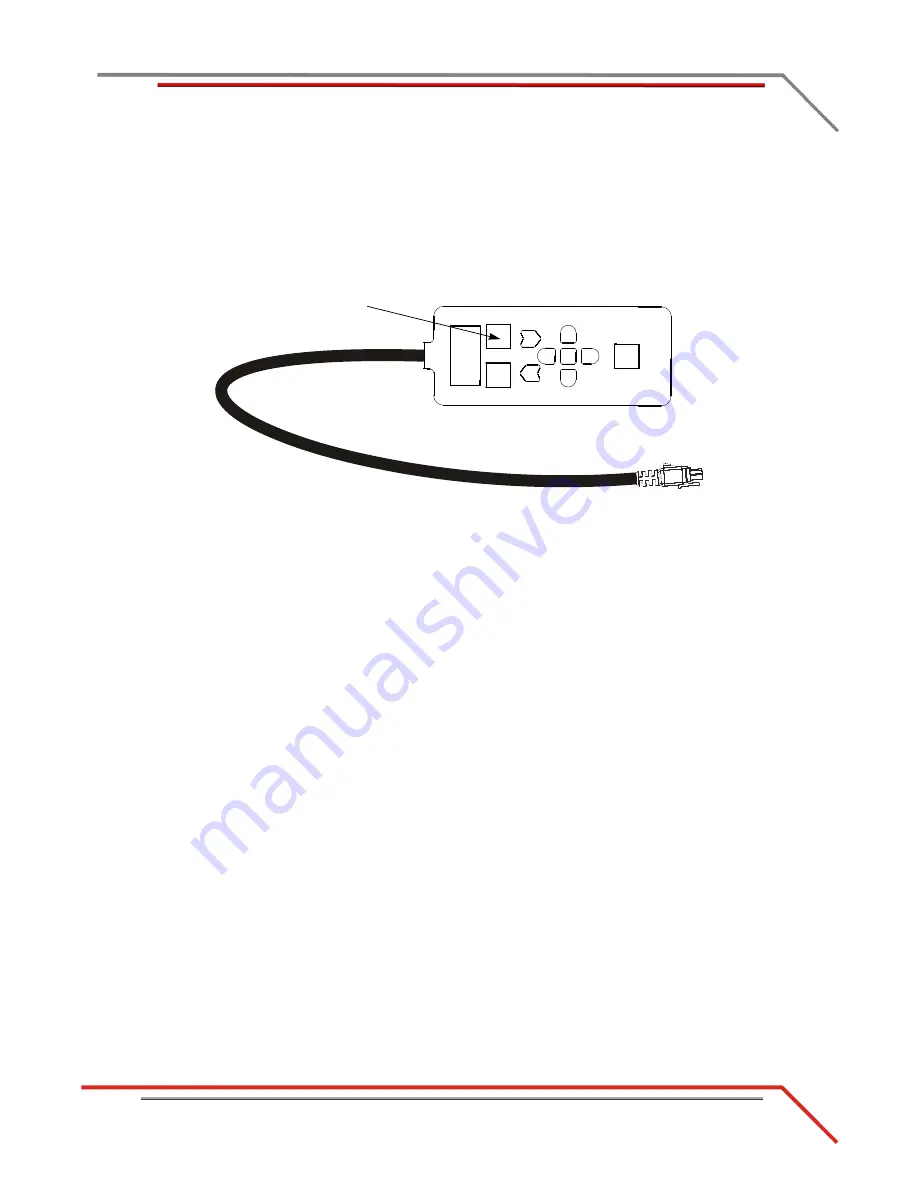
2-17
M O D E L 4 2 4 D Y N O W A R E R T U P G R A D E W I T H O U T E D D Y C U R R E N T
Testing
Version 5
DynoWare RT Upgrade for Model 424x Dynamometers Installation Guide
TESTING
1
Turn on the DynoWare RT module. This switch is located on the rear of the
module.
2
Using the pendant, release the brake.
3
Spin each drum. Look for the LED on the speed pickup cards to flash.
4
Apply the brake.
Figure 2-15: Use the Pendant to Release the Brake
release brake