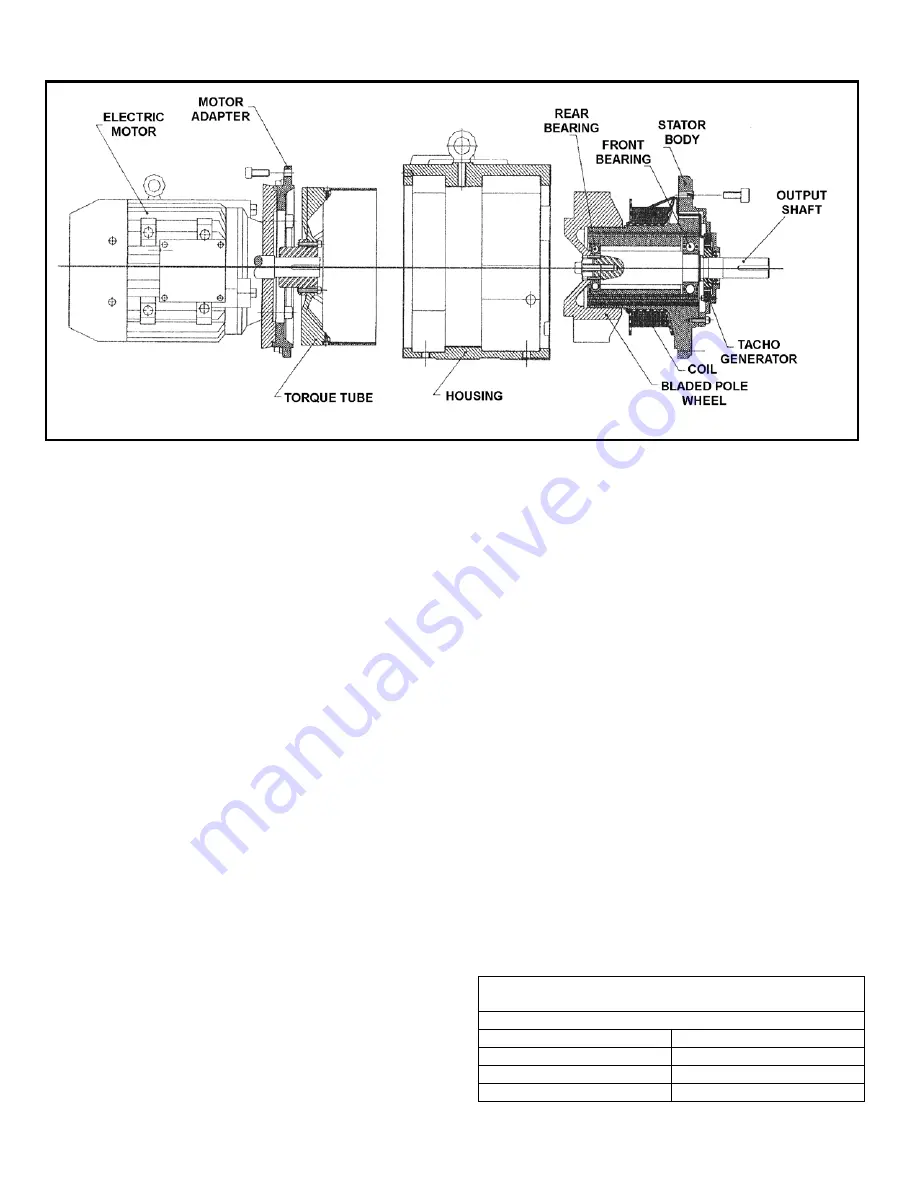
27
Typical Assembly Drawing of DCD Drive
Figure 6-1
Lubrication
The only parts in the clutch requiring lubrication are two
bearings. Standard units are grease lubricated and are
provided with large grease chambers next to the bearings
to permit a long period of operation before greasing is
required. Grease fitting locations are shown in Figures 6-
1 and 6-2.
The outboard bearing is greased through a grease fitting
located over the bearing in the output end bracket. The
motor bearings are greased through grease fittings
located in the end brackets over the bearings. Plugged
relief vents are located below the bearings. Smaller
motors have permanently sealed non-regreaseable
bearings.
Since the two most prevalent causes of bearing failure are
contamination and over greasing, do not over grease. For
most operating conditions the bearings should not be
greased more than twice a year. However, if the drive is
to be run continuously or operated in a high ambient
temperature [86ºF to 104ºF (30ºC to 40ºC)] or at a high
slip RPM, re-greasing should be done more frequently.
The grease specification is per Dynamatic Engineering
Standard MML 4-1.3. This is a premium grade of lithium
base N.L.G.I. #2 EP grease. Recommended greases are
listed in Table 6-2. Mobilux E.P. #2 is used at the factory.
Recommended amounts of grease for the bearings are
listed in Table 6-3. Any equivalent and compatible grease
may be used. Special greases may be specified at the
time of order entry. Consult your order papers if a special
grease has been specified.
When lubrication is required, use the following procedure
to grease the bearings:
1. Stop the motor and clutch and allow both to coast to
a complete stop.
2. Wipe the surfaces on and around the grease fittings
and relief holes clean. This is important and
necessary to prevent contaminating the bearings.
3. Remove the plugs from the relief holes (when
plugged). The relief hole for the center support
bearing is inside the housing and is not accessible.
4. Pump specified amount of grease into output end
bracket bearing through grease fitting above bearing.
If the unit is a separate clutch (without a motor
attached), pump two ounces of grease into each input
shaft bearing.
5. Pump two ounces of grease into each motor bearing
through grease fittings above the bearings. Smaller
motors have permanently sealed non-regreaseable
bearings
6. Allow the drive to run for 20 minutes with the relief
plugs removed to expel excess grease.
7. Wipe off all excess grease. Replace the plug button if
removed in step 4.
Recommended Greases
Table 6-2
Grease Specification for Ball & Spherical Roller
Bearings - N.L.G.I. Grade #2 EP - MML 4-1.3
Approved sources:
Shell
Alvania EP #2
Gulf
Gulfcrown EP #2
Texaco
Multifak EP #2
Mobil
Mobilux EP #2