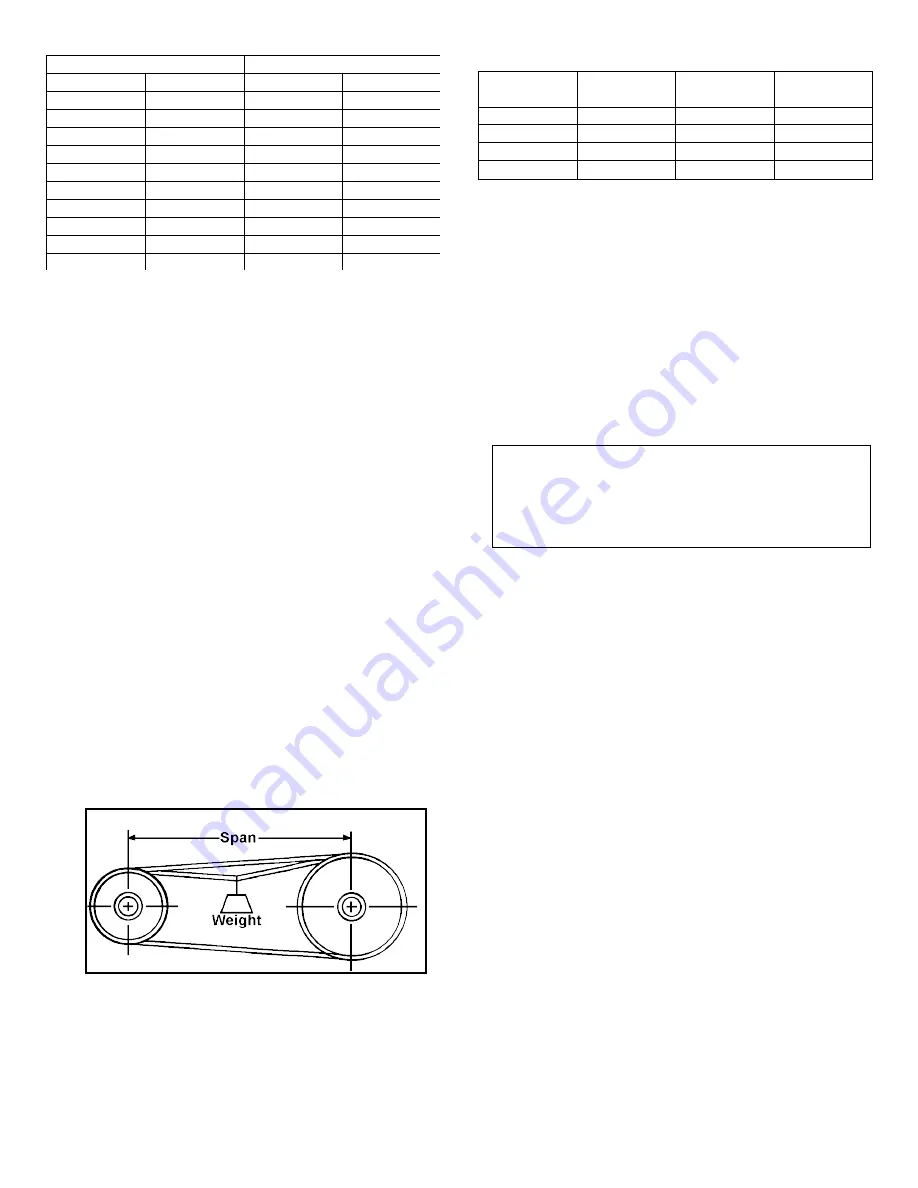
21
Belt Modulus Factors (Mf)
Table 3-4
Belt Type
Modulus
Factor
Belt Type
Modulus
Factor
A
0.500
E
5.938
B
0.813
3V
0.375
C
2.500
5V
0.750
D
5.000
8V
1.563
Pf = Position factor, a factor used to correct overhung load
capacity when the center of belt pull is not on the
center of the shaft keyway extension. Location
"L" is on the center of keyway. See Table 3-4
and Figure 3-1.
Mf = Belt Modulus Factor from Table 3-5.
2. Apply deflection pressure by hanging a weight on
each belt at the midpoint of the span as shown in
Figure 3-7. Pressure can also be applied using a
small spring scale. When properly adjusted, each belt
should deflect "1/64" for each inch of span.
3. If belts slip after tension has been properly adjusted,
sheaves or belts have been improperly sized.
4. With new belts, tensions should be checked and
adjusted after each 24 hours of operation until belts
are broken in.
Final Mounting
After completing the initial mounting procedures and
necessary alignment, secure the unit as follows:
1. Make sure unit is level and its feet are still in contact
with the mounting pads. If several thin shims were
installed during alignment, consider replacing them
with thicker shims. A few thick shims are preferred to
many thin ones.
2. Tighten mounting bolts or nuts to secure unit to base.
Recheck alignment and, if necessary, correct it.
Tightening bolts may pull unit down, especially when
many shims are used.
Precision Tension Check
Figure 3-6
3. For directly coupled units, dowel all interconnected
units to base to ensure that shaft alignment will be
maintained. For belt coupled units, recheck belt
tension arid correct it if necessary. Tightening bolts or
nuts may have moved unit, causing over- tensioning,
even though tension was proper before bolts were
tightened.
Lubrication
Bearings are grease lubricated and require no special
attention unless stored for over one year. Consult the
sections on "Storage" and/or "Maintenance" for greasing
instructions.
Shaft and Belt Guards
Before applying power and starting the unit, install guards
over all rotating shafts, couplings, belts and chain
devices. Refer to OSHA rules and regulation, paragraph
1910.219 for requirements covering guards on
mechanical power transmission apparatus. Be sure
machine is safe to operate and all safety devices have
been installed, checked out and made operable.
CAUTION
: When designing belt and shaft guards,
remember that bearings must be lubricated
periodically. Grease fittings should be accessible
through openings in guards and signs should indicate
the exact location of each grease inlet and outlet.
Electrical Wiring
All wiring to the drive, including any accessories, must
conform to the National Electrical Code and all other
applicable state and local codes. Motor leads and
transformer winding leads are terminated in a conduit box
mounted on the side of the motor. Leads for the clutch and
tachometer generator are terminated in a conduit box
mounted on the clutch housing. Accessories may also be
wired to the same conduit box or may be terminated in
another conduit box attached to the accessory.
Connections from the conduit boxes to the controller are
made by connecting each lead or terminal to the
appropriate lead or terminal in the controller as shown on
the connection diagram furnished with the controller.
Figure 3-8 shows typical connections for a standard drive
without any modifications or accessories. Section 8 of this
manual includes typical connection diagrams for common
accessories. For specially modified drives, refer to the
instructions furnished for the modification or added
accessory and to the instructions and diagrams furnished
with the controller. Tachometer generator leads and
speed signal reference leads should not be run in the
same conduit with motor power leads.
Transformer Winding (Applies to Models DCD-132
through DCD-225 ONLY)
The motor furnished with the drive DO NOT INCLUDE a
single phase, 115-volt, center tapped transformer winding
that can be used as a power source for the external
controller. The controllers requires a separate power
source.
Span
“Y” Dimension
Inches
mm
Inches
mm
60
1525
2.50
63
80
2030
2.75
70
100
2540
3.00
76
120
3050
4.00
101
140
3560
5.25
133
160
4060
6.50
165
180
4570
7.75
200
200
5080
9.00
230
220
5590
10.50
270
240
6100
12.00
305