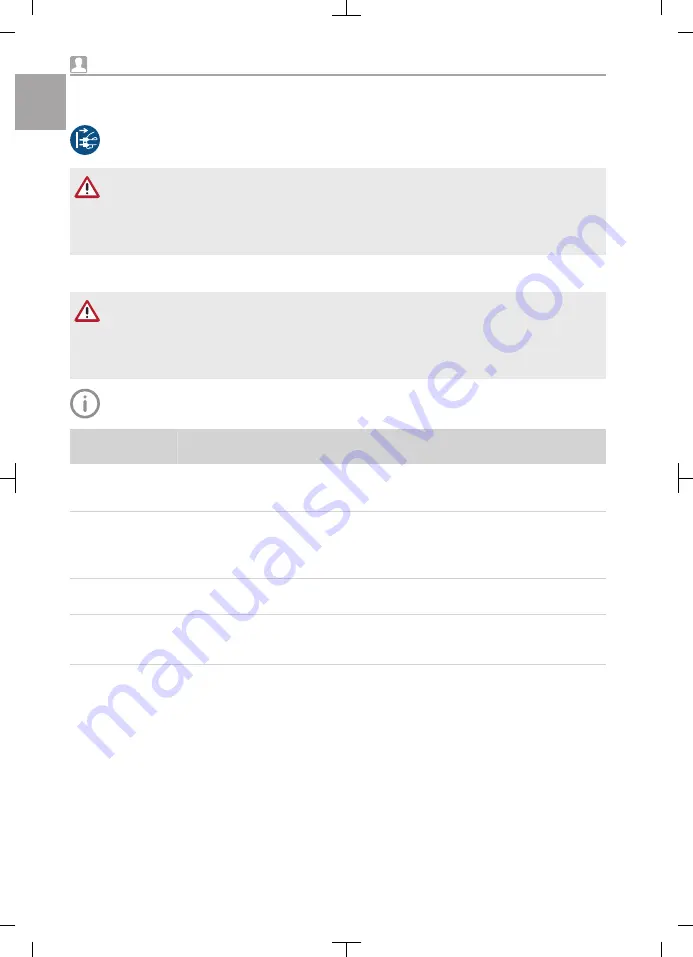
13 Maintenance
Prior to working on the unit or in case of danger, disconnect it from the mains.
CAUTION
Risk of infection due to burst filters
Particles enter the compressed air network and can therefore enter the mouth of the patient.
❯
Replace filters in accordance with the maintenance schedule.
13.1 Maintenance schedule
NOTICE
Risk of damage to the unit due to blocked filters
Continuous running due to reduced delivery. Damage to the unit due to burst filters.
❯
Replace filters in accordance with the maintenance schedule.
Every time you work with the unit, check it visually for damage to ensure safe and reliable opera-
tion. Damaged units must not be taken back into use.
Maintenance
interval
Maintenance work
At regular intervals
❯
Empty the collector tray under the membrane drying unit (the interval may vary
depending on the ambient conditions and method of working; empty it daily if
the humidity is high).
Annually
❯
Replace the air intake filter in the compressor unit – do this every six months if
there is a high concentration of dust.
❯
Replace the fine or sterile filter.
❯
Replace the sintered filter.
Every 5 years
❯
Replace the vibration reducers.
❯
Change the cup seal.
In accordance with
national law
❯
Check the safety valve.
❯
Carry out recurring safety inspections (e.g. pressure tank inspections, electrical
safety inspections) in accordance with applicable national laws.
Usage
24
5286100072L02 1909V005
EN
Содержание 5286100036
Страница 1: ...EN Tornado 2 Installation and operating instructions 0297 5286100072L02 5286100072L02 1909V005 ...
Страница 2: ......
Страница 33: ......
Страница 34: ......
Страница 35: ......