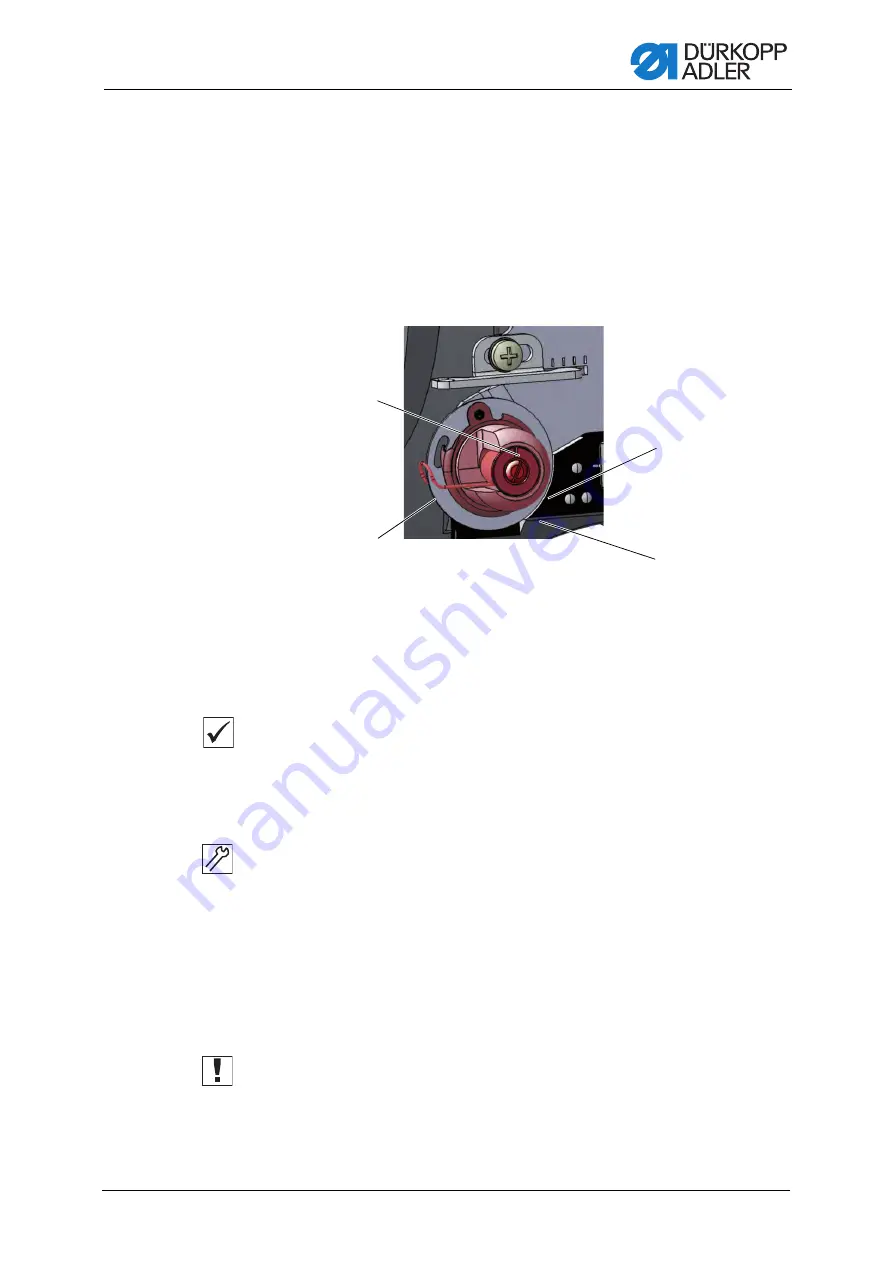
Setting the needle thread tension
Service Instructions 869-M PREMIUM - 00.0 - 07/2018
69
4. Move the needle thread regulator (2)
• Reduce needle thread tension: slide to the left
• Increase needle thread tension: slide to the right
5. Tighten the screw (1).
14.2 Setting the thread tension spring
Fig. 54: Setting the thread tension spring
The thread tension spring holds the needle thread under tension from
the top dead center of the thread lever up to the point when the needle eye
plunges into the sewing material.
Proper setting
The thread tension spring does not contact the stop until the needle eye
has plunged into the sewing material.
The setting for the thread tension spring must be varied according to
the sewing material and the required sewing result.
To set the thread tension spring:
1. Loosen the screw (4).
2. Turn the stop collar (1) to set the spring travel.
• Longer spring travel: turn counterclockwise
• Shorter spring travel: turn clockwise
3. Turn the tension disk (3) to set the spring tension.
• Greater spring tension: turn counterclockwise
• Lower spring tension: turn clockwise
Important
Do not twist the stop collar in doing so.
4. Tighten the screw (4).
(1)
- Stop collar
(2)
- Spring
(3)
- Tension disk
(4)
- Screw
①
②
③
④
Содержание 869-M Premium
Страница 1: ...869 M PREMIUM Service Instructions...
Страница 10: ...About these instructions 8 Service Instructions 869 M PREMIUM 00 0 07 2018...
Страница 120: ...Programming 118 Service Instructions 869 M PREMIUM 00 0 07 2018 Fig 89 Connecting adapter to DACcomfort...
Страница 142: ...Programming 140 Service Instructions 869 M PREMIUM 00 0 07 2018...
Страница 152: ...Maintenance 150 Service Instructions 869 M PREMIUM 00 0 07 2018...
Страница 154: ...Decommissioning 152 Service Instructions 869 M PREMIUM 00 0 07 2018...
Страница 156: ...Disposal 154 Service Instructions 869 M PREMIUM 00 0 07 2018...
Страница 168: ...Troubleshooting 166 Service Instructions 869 M PREMIUM 00 0 07 2018...
Страница 171: ...Appendix Service Instructions 869 M PREMIUM 00 0 07 2018 169 25 Appendix Fig 116 Wiring diagram...
Страница 172: ...Appendix 170 Service Instructions 869 M PREMIUM 00 0 07 2018 Fig 117 Wiring diagram...
Страница 173: ...Appendix Service Instructions 869 M PREMIUM 00 0 07 2018 171 Fig 118 Wiring diagram...
Страница 174: ...Appendix 172 Service Instructions 869 M PREMIUM 00 0 07 2018 Fig 119 Wiring diagram...
Страница 175: ...Appendix Service Instructions 869 M PREMIUM 00 0 07 2018 173 Fig 120 Wiring diagram...
Страница 176: ...Appendix 174 Service Instructions 869 M PREMIUM 00 0 07 2018 Fig 121 Wiring diagram...
Страница 177: ...Appendix Service Instructions 869 M PREMIUM 00 0 07 2018 175 Fig 122 Wiring diagram...
Страница 178: ...Appendix 176 Service Instructions 869 M PREMIUM 00 0 07 2018...
Страница 179: ......