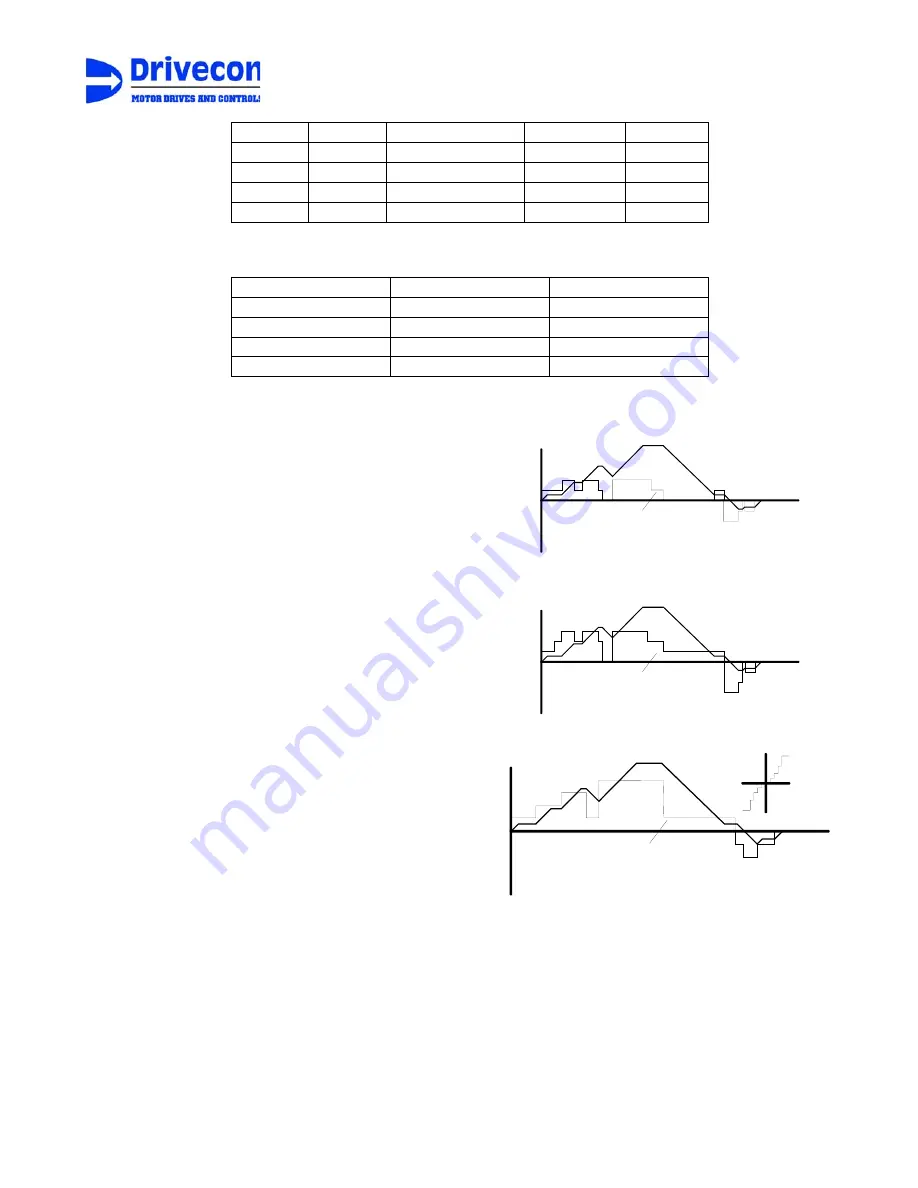
Service Manual
rev 5.0 with software Ind1V022
DID1 X1:38 FWE
FWE
FWE
DID2 X1:39 S11
S11
S11
DID3 X1:40 S21
S21
S21
DID4 X1:41 S12
S12
S12
DID5 X1:42 S22
S22
S22
Desired speed levels for multi-step control mode are selected with following parameters
Speed Parameter
Input
Speed 1
P2.2.8. / P2.2.9.
S1/ S2
Speed 2
P2.1.7.
MS 2
Speed 3
P2.1.8.
MS 3
Speed 4
P2.1.9.
MS 4
1.6.1 Description of the control methods
EP-control
requires two 2-step pushbuttons, one for
each direction. The operation is as follows:
-
the rest position means standstill (0-position)
-
during run the rest position means deceleration
-
step one (switch S1 or S2) means hold speed
-
when starting, step one means acceleration up to the minimum speed
-
step two (switch AP) means acceleration (up to the maximum speed if
desired)
-
at the maximum speed step two means hold speed, because the
maximum speed cannot be exceeded
Pushbutton position
rest = deceleration
step 1 = hold speed
step 2 = acceleration
speed
pushbutton
position
fwd
rev
time
EP-mode
EP3-control
requires a 3-step controller. The
operation is as follows:
-
the rest position means standstill (0-position)
-
step one (switch S1 or S2) is the minimum speed command
-
step two (EP hold command) means hold speed
-
step three (switch AP) means acceleration (up to the maximum speed
if desired)
-
when releasing the controller, step one means deceleration down to
the minimum speed
speed
Pushbutton position
rest = stop
step 1 = minimum speed
step 2 = hold speed
step 3 = acceleration
pushbutton
position
fwd
rev
time
EP3-mode
MS-control
requires a 2 to 4-step controller. The
operation is as follows:
-
each step has its own frequency
-
the frequencies are freely selectable
-
when controller is set to a certain step, the speed changes to equal
value
speed
controller
position
fwd
rev
time
speed
controller
position
MS-mode
1.7 Mechanical brake control
D2L has a brake contactor to control electromechanical disk brake of hoisting motor. The disk brake is opened
and kept open during run by DC-voltage. When there is no voltage present the brake is closed and also kept
closed by spring force.
The brake is controlled so that during starting the motor first generates torque and after that the brake is
opened. The same applies for stopping; while the brake is being closed, the motor still generates torque.
8/58
Drivecon Inc. reserves the right to alter or amend the above information without notice.
Содержание D2L
Страница 59: ......