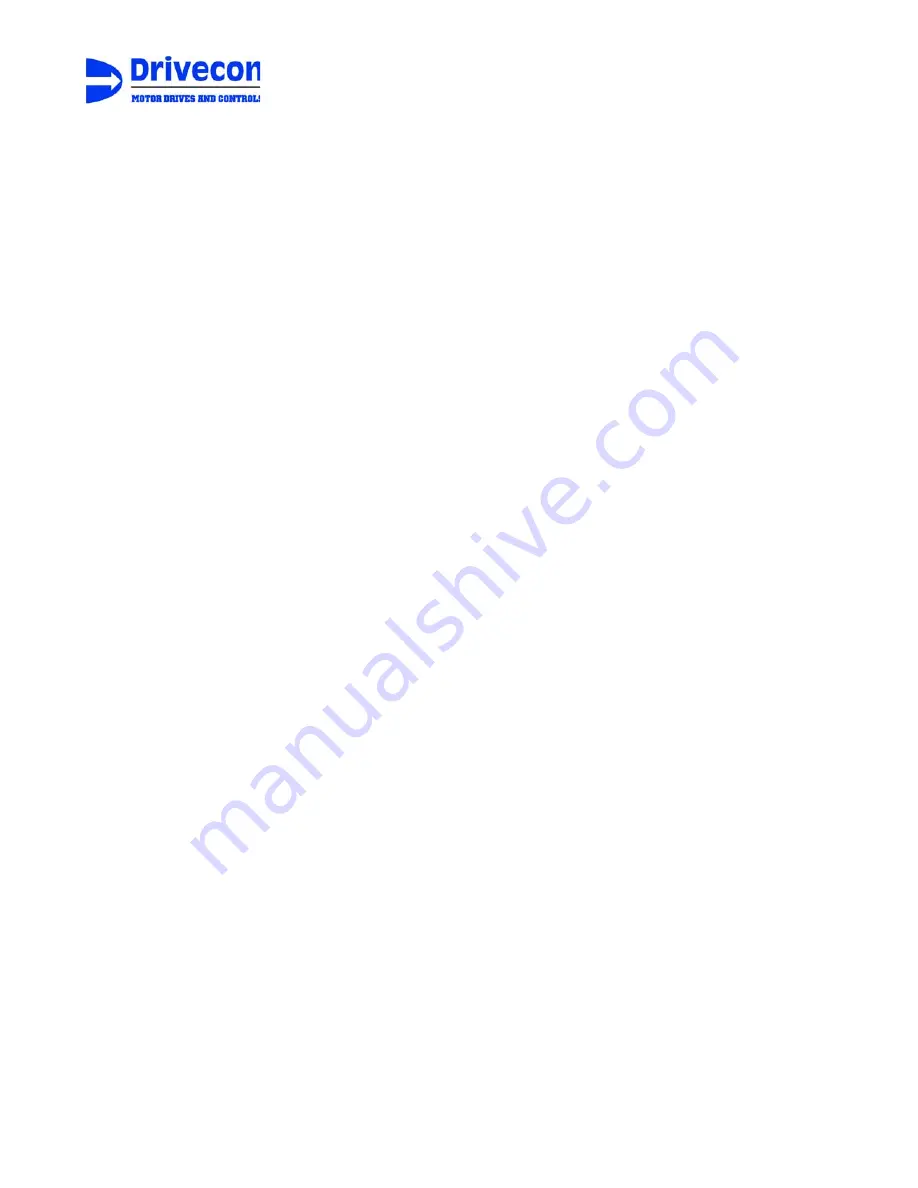
Service Manual
rev 5.0 with software Ind1V022
7 SPEED SUPERVISION SETTINGS
SSU is a hoist motion speed supervision unit, which reads the pulse frequency from the hoist motor sensor
bearing, encoder or pulse sensor. This pulse frequency is compared with a fixed oscillator frequency and D2L
frequency reference. As a result of frequency comparison, there are three different speed supervision
functions available:
- overspeed supervision (rush control)
- stall
supervision
- speed difference supervision
Overspeed supervision (F61)
is totally implemented by hardware.
Switches S2-2 and S2-3 divide the full frequency range to four frequency areas.
Selected frequency area is the same for normal and ESR speeds.
The four frequency areas are each divided to lower and upper frequency ranges
Switch S2-1 selects the frequency range at normal speed.
Switch S2-4 selects the frequency range at ESR speed (Extended Speed Range).
The exact tripping frequency level is selected with rotary switches.
Switch S1 sets the tripping level at normal speed (value shown in V4.8.1).
Switch S3 sets the tripping level at ESR speed (value shown in V4.8.2).
Overspeed tripping levels are shown at display as % of the nominal speed. The overspeed setting should be
15-25% above the full speed.
Switches S2-2 and S2-3 select range for overspeed detection level. Range of detection level is the same for
both, normal and ESR (Extended Speed range) use.
Fine adjustment for normal use is done by rotary switch S1 and switch S2-1.
Fine adjustment for ESR use is done by rotary switch S3 and switch S2-4.
Overspeed detection levels are shown at display panel as % of nominal speed. Overspeed setting should be
15-25% above the full speed.
Adjusted overspeed detection level for normal use is shown in parameter V4.8.1.
Adjusted overspeed detection level for ESR use is shown in parameter V4.8.2.
Speed difference supervision (F62)
compares the motor actual speed (= pulse frequency) with Drive
frequency reference. In practice this means that the motor slip is measured and if that exceeds a limit,
supervision stops the motion.
Stall supervision (F63)
stops the motion if there are no pulses coming from the sensor when the brake is
open (K7 energised).
SSU relay test (F64):
SSU Relay is tested in every power up. Driving is prevented if fault has been detected.
SSU Watchdog fault (F65):
Communication between SSU board and control board is tested once in 50ms.
Fault will be detected if there is communication error. When a fault is detected the drive is stopped.
SSU Overspeed Limit (F66):
maximum setting of overspeed limit is 1.4
×
maximum speed of direction S2.
Fault will be detected if overspeed limit is set over that value. When a fault is detected the drive is prevented.
39/58
Drivecon Inc. reserves the right to alter or amend the above information without notice.
Содержание D2L
Страница 59: ......