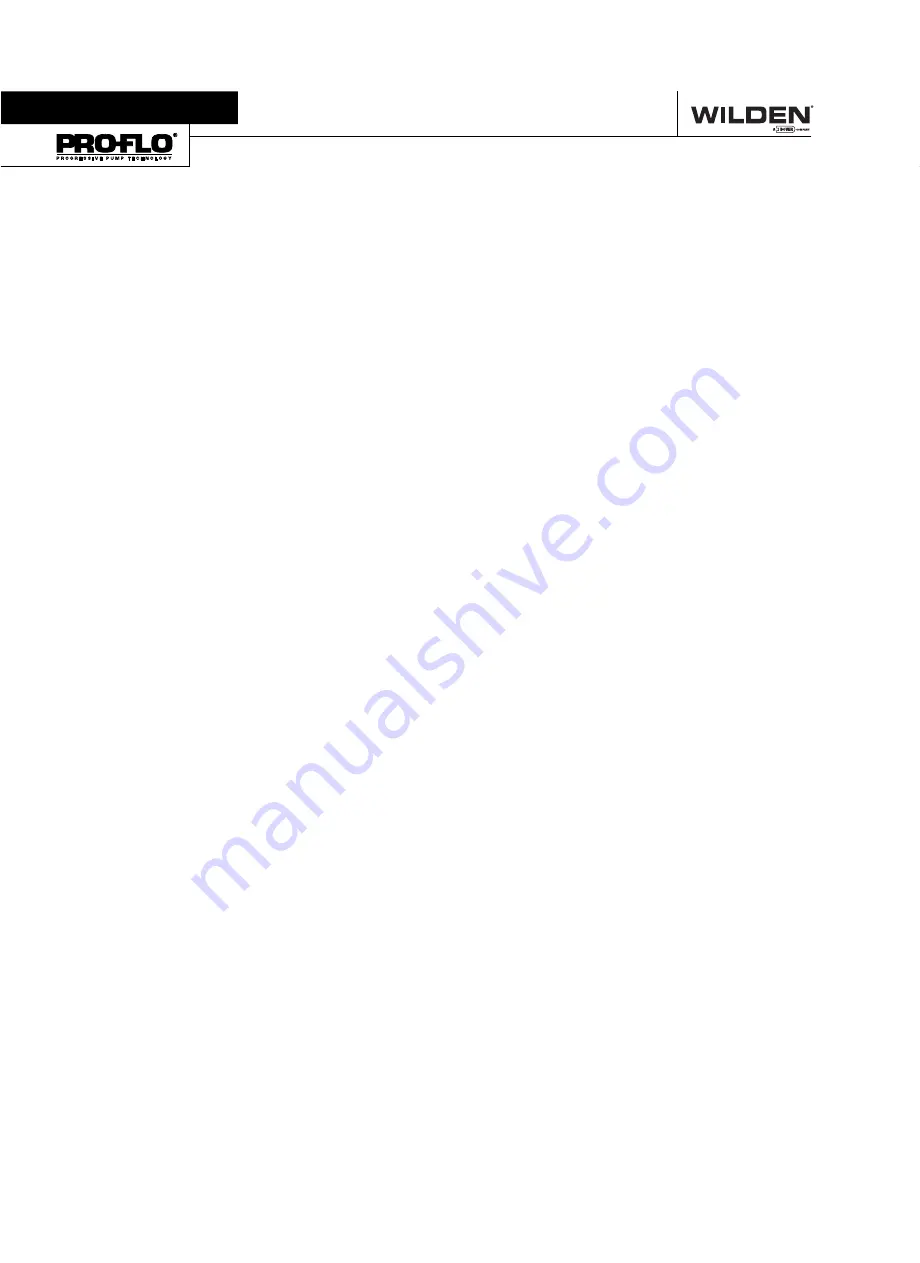
WILDEN PUMP & ENGINEERING, LLC
16
WIL-11100-E-05
S e c t i o n 6
S U G G E S T E D I N S T A L L A T I O N
Wilden pumps are designed to meet the performance
requirements of even the most demanding pumping
applications. They have been designed and manufactured
to the highest standards and are available in a variety of
liquid path materials to meet your chemical resistance
needs. Refer to the performance section of this manual for
an in-depth analysis of the performance characteristics of
your pump. Wilden offers the widest variety of elastomer
options in the industry to satisfy temperature, chemical
compatibility, abrasion resistance and fl ex concerns.
The suction pipe size should be at least the equivalent or
larger than the diameter size of the suction inlet on your
Wilden pump. The suction hose must be non-collapsible,
reinforced type as these pumps are capable of pulling a high
vacuum. Discharge piping should also be the equivalent
or larger than the diameter of the pump discharge which
will help reduce friction losses. It is critical that all fi ttings
and connections are airtight or a reduction or loss of pump
suction capability will result.
INSTALLATION: Months of careful planning, study,
and selection efforts can result in unsatisfactory pump
performance if installation details are left to chance.
Premature failure and long term dissatisfaction can be
avoided if reasonable care is exercised throughout the
installation process.
LOCATION: Noise, safety, and other logistical factors usually
dictate where equipment will be situated on the production
fl oor. Multiple installations with confl icting requirements
can result in congestion of utility areas, leaving few choices
for additional pumps.
Within the framework of these and other existing conditions,
every pump should be located in such a way that six key
factors are balanced against each other to maximum
advantage.
ACCESS: First of all, the location should be accessible. If
it’s easy to reach the pump, maintenance personnel will
have an easier time carrying out routine inspections and
adjustments. Should major repairs become necessary, ease
of access can play a key role in speeding the repair process
and reducing total downtime.
AIR SUPPLY: Every pump location should have an air line
large enough to supply the volume of air necessary to
achieve the desired pumping rate. Use air pressure up to
a maximum of 8.6 bar (125 psig) depending on pumping
requirements.
For best results, the pumps should use a 5µ (micron) air
fi lter, needle valve and regulator. The use of an air fi lter
before the pump will ensure that the majority of any pipeline
contaminants will be eliminated.
SOLENOID OPERATION: When operation is controlled by a
solenoid valve in the air line, three-way valves should be
used. This valve allows trapped air between the valve and
the pump to bleed off which improves pump performance.
Pumping volume can be estimated by counting the number
of strokes per minute and then multiplying the fi gure by the
displacement per stroke.
MUFFLER: Sound levels are reduced below OSHA
specifi cations using the standard Wilden muffl er. Other
muffl ers can be used to further reduce sound levels, but
they usually reduce pump performance.
ELEVATION: Selecting a site that is well within the pump’s
dynamic lift capability will assure that loss-of-prime issues will
be eliminated. In addition, pump effi ciency can be adversely
affected if proper attention is not given to site location.
PIPING: Final determination of the pump site should not be
made until the piping challenges of each possible location
have been evaluated. The impact of current and future
installations should be considered ahead of time to make
sure that inadvertent restrictions are not created for any
remaining sites.
The best choice possible will be a site involving the shortest
and straightest hook-up of suction and discharge piping.
Unnecessary elbows, bends, and fi ttings should be avoided.
Pipe sizes should be selected to keep friction losses within
practical limits. All piping should be supported independently
of the pump. In addition, the piping should be aligned to
avoid placing stress on the pump fi ttings.
Flexible hose can be installed to aid in absorbing the forces
created by the natural reciprocating action of the pump. If the
pump is to be bolted down to a solid location, a mounting
pad placed between the pump and the foundation will assist
in minimizing pump vibration. Flexible connections between
the pump and rigid piping will also assist in minimizing
pump vibration. If quick-closing valves are installed at any
point in the discharge system, or if pulsation within a system
becomes a problem, a surge suppressor (SD Equalizer
®
)
should be installed to protect the pump, piping and gauges
from surges and water hammer.
If the pump is to be used in a self-priming application, make
sure that all connections are airtight and that the suction lift is
within the model’s ability. Note: Materials of construction and
elastomer material have an effect on suction lift parameters.
Please refer to the performance section for specifi cs.
When pumps are installed in applications involving fl ooded
suction or suction head pressures, a gate valve should be
installed in the suction line to permit closing of the line for
pump service.
Pumps in service with a positive suction head are most effi cient
when inlet pressure is limited to 0.5–0.7 bar (7–10 psig).
Premature diaphragm failure may occur if positive suction
is 0.7 bar (10 psig) and higher.
SUBMERSIBLE APPLICATIONS: Pro-Flo V™ pumps can be
used for submersible applications, when using the Pro-Flo
V™ submersible option. Turbo-Flo™ pumps can also be
used for submersible applications.
NOTE: Pro-Flo
®
and Accu-Flo™ pumps are not submersible.
ALL WILDEN PUMPS ARE CAPABLE OF PASSING SOLIDS.
A STRAINER SHOULD BE USED ON THE PUMP INTAKE TO
ENSURE THAT THE PUMP'S RATED SOLIDS CAPACITY IS
NOT EXCEEDED.
CAUTION: DO NOT EXCEED 8.6 BAR (125 PSIG) AIR
SUPPLY PRESSURE.
Содержание Wilden Advance Pro-Flo V PV400 Series
Страница 37: ...WIL 11100 E 05 35 WILDEN PUMP ENGINEERING LLC...
Страница 38: ...WILDEN PUMP ENGINEERING LLC 36 WIL 11100 E 05...