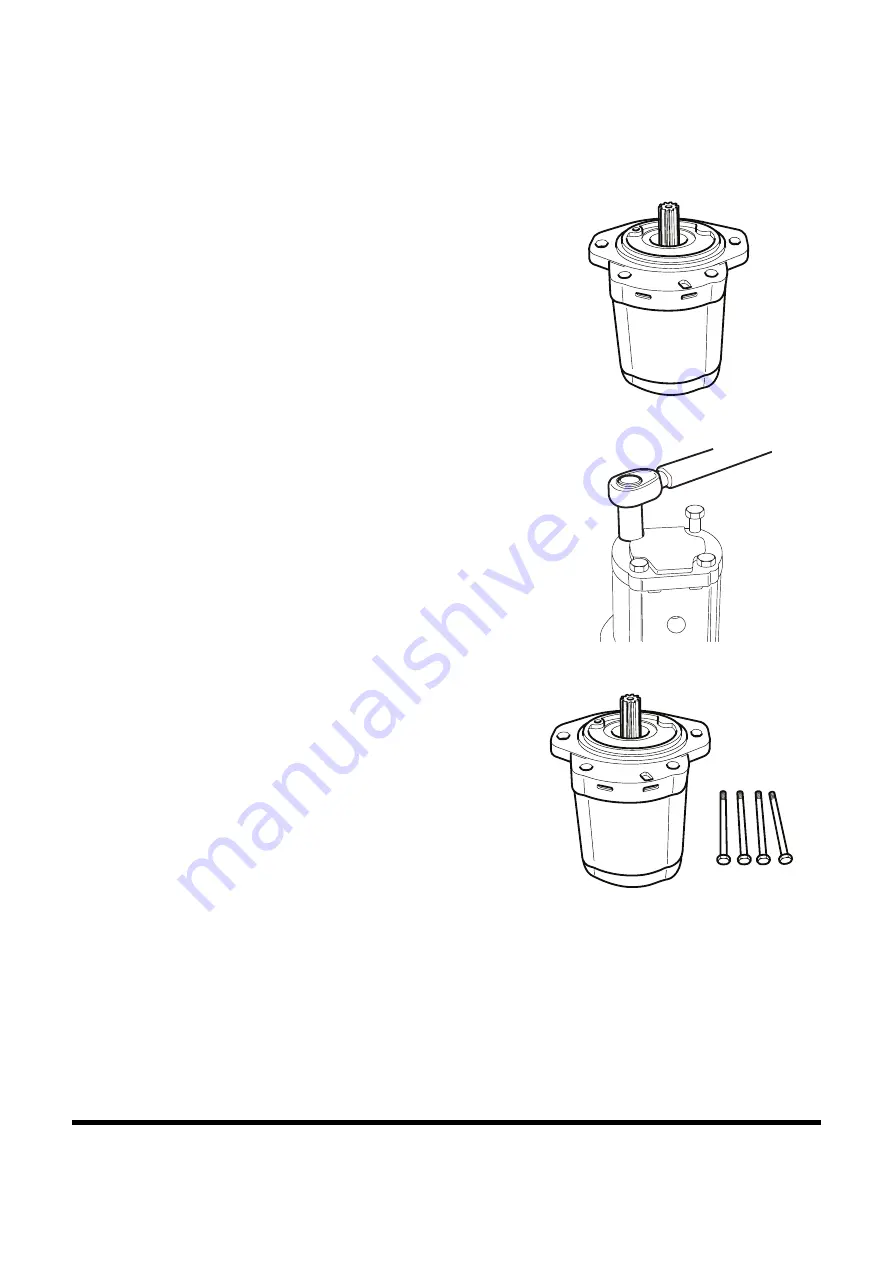
Gear Pump
Page 6
SINGLE GEAR PUMP
Disassembly
1.
Clean exterior of pump.
2.
Remove clamp bolts.
3.
Cover sharp edges of driveshaft with adhesive tape and
coat shaft end extension with clean grease, to avoid any
damage to lip of shaft seal when removing mounting
flange.
FG001072
Figure 1
FG001074
Figure 2
FG001073
Figure 3
Содержание DX225LC-3
Страница 4: ......
Страница 6: ......
Страница 9: ...1Safety ...
Страница 10: ......
Страница 12: ...SP002322 Track Excavator Maintenance Safety Page 2 MEMO ...
Страница 14: ...SP002322 Track Excavator Maintenance Safety Page 4 MEMO ...
Страница 77: ...1Specifications ...
Страница 78: ......
Страница 80: ...SP002491 Specifications for DX225LC 3 Page 2 MEMO ...
Страница 82: ...SP002491 Specifications for DX225LC 3 Page 4 MEMO ...
Страница 84: ...SP002491 Specifications for DX225LC 3 Page 6 ...
Страница 106: ...SP002491 Specifications for DX225LC 3 Page 28 ...
Страница 107: ...1General Maintenance ...
Страница 108: ......
Страница 110: ...SP002454 General Maintenance Instructions Page 2 MEMO ...
Страница 112: ...SP002454 General Maintenance Instructions Page 4 MEMO ...
Страница 128: ...SP002454 General Maintenance Instructions Page 20 ...
Страница 129: ...SP002404 Page 1 Standard Torques SP002404 STANDARD TORQUESSP002404 Standard Torques Edition 2 ...
Страница 130: ...SP002404 Standard Torques Page 2 MEMO ...
Страница 132: ...SP002404 Standard Torques Page 4 MEMO ...
Страница 145: ...1Upper Structure ...
Страница 146: ......
Страница 147: ...SP002324 Page 1 Cabin SP002324 CABIN SP002324 Cabin Edition 3 ...
Страница 148: ...SP002324 Cabin Page 2 MEMO ...
Страница 150: ...SP002324 Cabin Page 4 MEMO ...
Страница 161: ...SP002492 Page 1 Counterweight SP002492 COUNTERWEIGHT SP002492 Counterweight Edition 1 ...
Страница 162: ...SP002492 Counterweight Page 2 MEMO ...
Страница 164: ...SP002492 Counterweight Page 4 MEMO ...
Страница 170: ...SP002492 Counterweight Page 10 ...
Страница 171: ...SP002493 Page 1 Fuel Tank SP002493 FUEL TANK SP002493 Fuel Tank Edition 1 ...
Страница 172: ...SP002493 Fuel Tank Page 2 MEMO ...
Страница 174: ...SP002493 Fuel Tank Page 4 MEMO ...
Страница 186: ...SP002493 Fuel Tank Page 16 ...
Страница 188: ...SP002534 Fuel Transfer Pump Option Page 2 MEMO ...
Страница 190: ...SP002534 Fuel Transfer Pump Option Page 4 MEMO ...
Страница 196: ...SP002534 Fuel Transfer Pump Option Page 10 ...
Страница 197: ...SP002329 Page 1 Swing Bearing SP002329 SWING BEARING SP002329 Swing Bearing Edition 2 ...
Страница 198: ...SP002329 Swing Bearing Page 2 MEMO ...
Страница 200: ...SP002329 Swing Bearing Page 4 MEMO ...
Страница 206: ...SP002329 Swing Bearing Page 10 ...
Страница 207: ...1Lower Structure and Chassis ...
Страница 208: ......
Страница 209: ...SP002494 Page 1 Track Assembly SP002494 TRACK ASSEMBLY SP002494 Track Assembly Edition 1 ...
Страница 210: ...SP002494 Track Assembly Page 2 MEMO ...
Страница 212: ...SP002494 Track Assembly Page 4 MEMO ...
Страница 218: ...SP002494 Track Assembly Page 10 Track Shoe 8 9 10 11 2 7 2 7 FG023178 1 3 6 4 5 Figure 4 ...
Страница 229: ...SP002494 Page 21 Track Assembly ...
Страница 234: ...SP002494 Track Assembly Page 26 UPPER ROLLER Parts List FG022519 Track Frame 12 14 8 11 9 13 7 10 6 4 3 2 5 1 Figure 35 ...
Страница 240: ...SP002494 Track Assembly Page 32 ...
Страница 241: ...1Engine and Drivetrain ...
Страница 242: ......
Страница 244: ...SP002328 Engine Coolant Heater Option Page 2 MEMO ...
Страница 246: ...SP002328 Engine Coolant Heater Option Page 4 MEMO ...
Страница 260: ...SP002328 Engine Coolant Heater Option Page 18 ...
Страница 261: ...SP002495 Page 1 Drive Coupling Main Pump SP002495 DRIVE COUPLING MAIN PUMP SP002495 Drive Coupling Main Pump Edition 1 ...
Страница 262: ...SP002495 Drive Coupling Main Pump Page 2 MEMO ...
Страница 264: ...SP002495 Drive Coupling Main Pump Page 4 MEMO ...
Страница 271: ...1Hydraulics ...
Страница 272: ......
Страница 274: ...SP002535 Hydraulic System Troubleshooting Testing and Adjustment Page 2 MEMO ...
Страница 306: ...SP002535 Hydraulic System Troubleshooting Testing and Adjustment Page 34 ...
Страница 307: ...SP002455 Page 1 Accumulator SP002455 ACCUMULATOR SP002455 Accumulator Edition 1 ...
Страница 308: ...SP002455 Accumulator Page 2 MEMO ...
Страница 310: ...SP002455 Accumulator Page 4 MEMO ...
Страница 315: ...SP002456 Page 1 Center Joint Swivel SP002456 CENTER JOINT SWIVEL SP002456 1Center Joint Swivel Edition 2 ...
Страница 316: ...SP002456 Center Joint Swivel Page 2 MEMO ...
Страница 318: ...SP002456 Center Joint Swivel Page 4 MEMO ...
Страница 320: ...SP002456 Center Joint Swivel Page 6 ...
Страница 329: ...SP002497 Page 1 Cylinders SP002497 CYLINDERS SP002497 Cylinders Edition 1 ...
Страница 330: ...SP002497 Cylinders Page 2 MEMO ...
Страница 332: ...SP002497 Cylinders Page 4 MEMO ...
Страница 353: ...SP002497 Page 25 Cylinders Slipper Seal Jig ARS4770L A 2 A A 14 B B 40 5 R 1 0 R1 1 0 Figure 11 ...
Страница 356: ...SP002497 Cylinders Page 28 Slipper Seal Straightening Jig ARS4780L 2 R1 50 25 100 A 15 A 2 5 R 2 C 1 Figure 12 ...
Страница 368: ...SP002497 Cylinders Page 40 ...
Страница 369: ...SP002498 Page 1 Swing Device SP002498 SWING DEVICE SP002498 Swing Device Edition 1 ...
Страница 370: ...SP002498 Swing Device Page 2 MEMO ...
Страница 372: ...SP002498 Swing Device Page 4 MEMO ...
Страница 418: ...SP002498 Swing Device Page 50 ...
Страница 419: ...SP002499 Page 1 Travel Device SP002499 TRAVEL DEVICE SP002499 Travel Device Edition 1 ...
Страница 420: ...SP002499 Travel Device Page 2 MEMO ...
Страница 422: ...SP002499 Travel Device Page 4 MEMO ...
Страница 426: ...SP002499 Travel Device Page 8 Basic Structure and Diagram Basic Structure of TM Motor Figure 1 ...
Страница 440: ...SP002499 Travel Device Page 22 External Specifications Diagrams Figure 14 ...
Страница 441: ...SP002499 Page 23 Travel Device Basic Structure and Diagrams Assembly Cross Section Figure 15 ...
Страница 477: ...SP002502 Page 1 Main Pump SP002502 MAIN PUMP SP002502 Main Pump Edition 1 ...
Страница 478: ...SP002502 Main Pump Page 2 MEMO ...
Страница 480: ...SP002502 Main Pump Page 4 MEMO ...
Страница 496: ...SP002502 Main Pump Page 20 ...
Страница 497: ...SP002503 Page 1 PTO Server SP002503 PTO SERVER SP002503 PTO Server Edition 1 ...
Страница 498: ...SP002503 PTO Server Page 2 MEMO ...
Страница 500: ...SP002503 PTO Server Page 4 MEMO ...
Страница 508: ...SP002503 PTO Server Page 12 ...
Страница 509: ...SP002500 Page 1 Gear Pump SP002500 GEAR PUMP SP002500 Gear Pump Edition 1 ...
Страница 510: ...SP002500 Gear Pump Page 2 MEMO ...
Страница 512: ...SP002500 Gear Pump Page 4 MEMO ...
Страница 520: ...SP002500 Gear Pump Page 12 ...
Страница 521: ...SP002403 Page 1 Main Control Valve SP002403 MAIN CONTROL VALVESP002403 Main Control Valve Edition 1 ...
Страница 522: ...SP002403 Main Control Valve Page 2 MEMO ...
Страница 524: ...SP002403 Main Control Valve Page 4 MEMO ...
Страница 531: ...SP002403 Page 11 Main Control Valve ...
Страница 557: ...SP002403 Page 37 Main Control Valve ...
Страница 590: ...SP002403 Main Control Valve Page 70 ...
Страница 592: ...SP002395 Remote Control Valve Work Lever Joystick Page 2 MEMO ...
Страница 594: ...SP002395 Remote Control Valve Work Lever Joystick Page 4 MEMO ...
Страница 596: ...SP002395 Remote Control Valve Work Lever Joystick Page 6 ...
Страница 614: ...SP002381 Travel Control Valve with Damper Page 2 MEMO ...
Страница 616: ...SP002381 Travel Control Valve with Damper Page 4 MEMO ...
Страница 622: ...SP002381 Travel Control Valve with Damper Page 10 Parts List Figure 3 ...
Страница 640: ...SP002381 Travel Control Valve with Damper Page 28 ...
Страница 641: ...SP002406 Page 1 Solenoid Valve Assembly SP002406 SOLENOID VALVE ASSEMBLYSP002406 1Solenoid Valve Assembly Edition 2 ...
Страница 642: ...SP002406 Solenoid Valve Assembly Page 2 MEMO ...
Страница 644: ...SP002406 Solenoid Valve Assembly Page 4 MEMO ...
Страница 652: ...SP002406 Solenoid Valve Assembly Page 12 ...
Страница 654: ...SP002458 Breaker EPPR Valve Option Page 2 MEMO ...
Страница 656: ...SP002458 Breaker EPPR Valve Option Page 4 MEMO ...
Страница 665: ...SP002529 Page 1 Dozer Valve SP002529 DOZER VALVE SP002529 3Dozer Valve Edition 1 ...
Страница 666: ...SP002529 Dozer Valve Page 2 MEMO ...
Страница 668: ...SP002529 Dozer Valve Page 4 MEMO ...
Страница 680: ...SP002507 Hydraulic Schematic DX225LC 3 Page 2 MEMO ...
Страница 682: ...SP002507 Hydraulic Schematic DX225LC 3 Page 4 MEMO ...
Страница 684: ...SP002507 Hydraulic Schematic DX225LC 3 Page 6 ...
Страница 686: ......
Страница 687: ...1Electrical System ...
Страница 688: ......
Страница 689: ...SP002337 Page 1 Electrical System 8 SP002337 ELECTRICAL SYSTEMSP002337 Electrical System Edition 2 ...
Страница 690: ...SP002337 Electrical System Page 2 MEMO ...
Страница 694: ...SP002337 Electrical System Page 6 ...
Страница 697: ...SP002337 Page 9 Electrical System ...
Страница 711: ...SP002337 Page 23 Electrical System ...
Страница 779: ...SP002337 Page 91 Electrical System ...
Страница 839: ...SP002337 Page 151 Electrical System ...
Страница 844: ...SP002337 Electrical System Page 156 ...
Страница 845: ...SP002508 Page 1 Electrical Schematic SP002508 ELECTRICAL SCHEMATICSP002508 1Electrical Schematic Edition 1 ...
Страница 846: ...SP002508 Electrical Schematic Page 2 MEMO ...
Страница 848: ...SP002508 Electrical Schematic Page 4 MEMO ...
Страница 850: ...SP002508 Electrical Schematic Page 6 ...
Страница 852: ......
Страница 853: ...1Attachments ...
Страница 854: ......
Страница 855: ...SP002505 Page 1 Boom and Arm SP002505 BOOM AND ARM SP002505 Boom and Arm Edition 1 ...
Страница 856: ...SP002505 Boom and Arm Page 2 MEMO ...
Страница 858: ...SP002505 Boom and Arm Page 4 MEMO ...
Страница 867: ...SP002506 Page 1 Bucket SP002506 BUCKET SP002506 1Bucket Edition 1 ...
Страница 868: ...SP002506 Bucket Page 2 MEMO ...
Страница 870: ...SP002506 Bucket Page 4 MEMO ...
Страница 874: ...SP002506 Bucket Page 8 5 Roll the new O ring 1 Figure 7 into the O ring groove FG019075 1 Figure 7 ...
Страница 878: ...SP002506 Bucket Page 12 ...