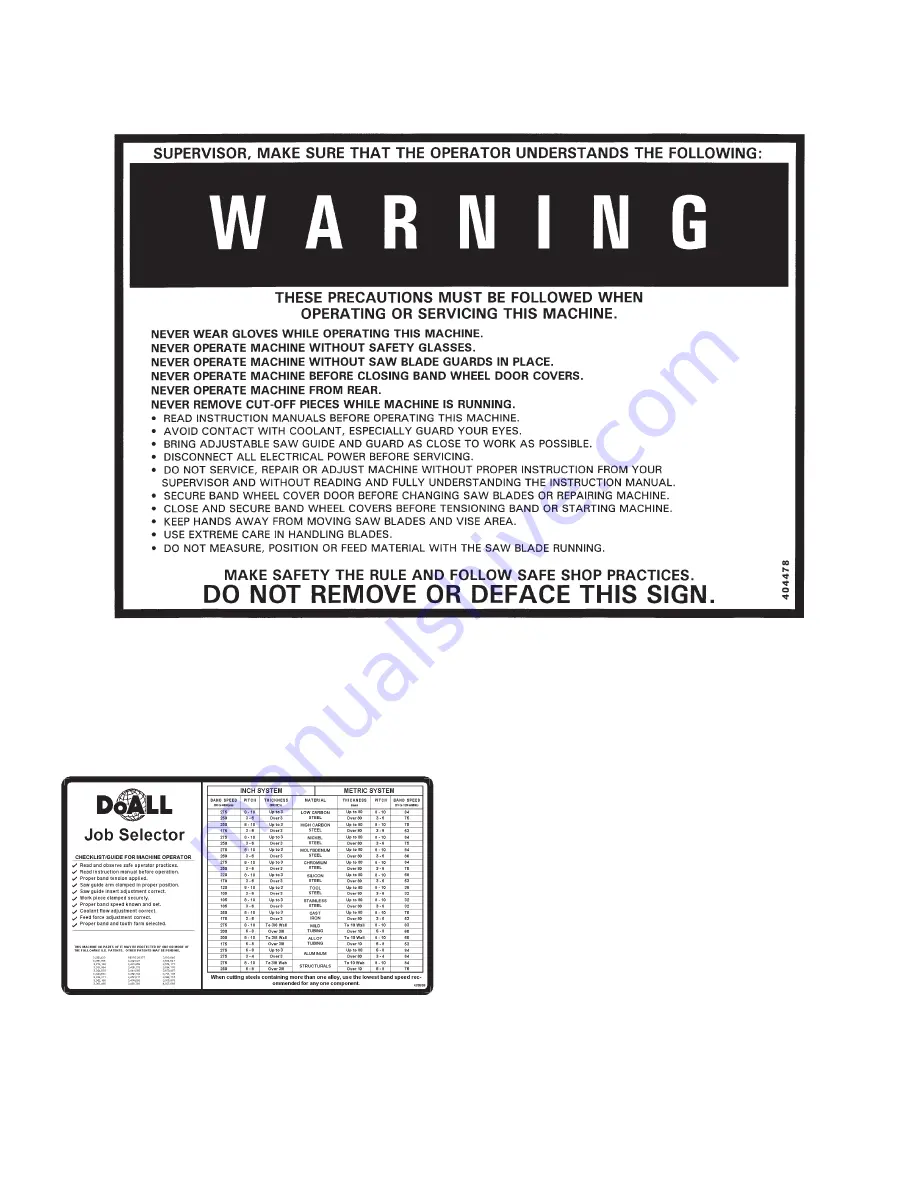
10
OPERATION
Warning Label - READ and UNDERSTAND.
USING THE JOB SELECTOR
1.
Refer to the Job Selector on the left bandwheel door
for information about suggested band speed and
band pitch for material type and thickness.
Job Selector.
2.
For example, to cut low carbon steel which is two
(2) inches (50.8 mm) thick, you would choose a
saw band with 8-10 pitch, and set the band speed
for 275 fpm (84 m/min).
MACHINE CAPACITIES
1.
Your machine is designed to cut retangular stock
up to 12 inches (304.8 mm) high and 12 inches
(304.8 mm) wide. It will also cut round stock up to
12 inches (304.8 mm) in diameter.
2.
The maximum index length (without multiple index)
is 16 inches (406.4 mm) or 160 inches (4064.0 mm)
with multiple index; the minimum indexable length
is 1/2 inch (12.7 mm).
3.
Recommended smallest diameter work piece that
can be cut is 1/2 inch (12.7 mm). Minimum butt
end non-nested length during automatic indexing
is three (3) inches (76.2 mm).
•
See the
"Accessories"
section for capacities of the
optional Nesting Fixture.
4.
Vise bed capacity is approximately 3000 pounds
(1360.8 kg) evenly distributed.
SAFETY PRECAUTIONS
Содержание DC-330NC
Страница 1: ......
Страница 5: ...MACHINE DIMENSIONS FLOOR PLAN INCHES 03 MILLIMETERS 1 mm...
Страница 6: ...MACHINE DIMENSIONS Continued INCHES 03 MILLIMETERS 1 mm FRONT VIEW...
Страница 7: ...MACHINE DIMENSIONS Continued INCHES 03 MILLIMETERS 1 mm SIDE VIEW...
Страница 8: ...MACHINE FEATURES FRONT VIEW...
Страница 9: ...MACHINE DIMENSIONS Continued REAR VIEW...
Страница 10: ...MACHINE DIMENSIONS Continued PROXIMITY LIMIT SWITCH LOCATIONS TOP VIEW...
Страница 27: ...23 LUBRICATION NEXT 2 PAGES...
Страница 29: ...25 LUBRICATION DIAGRAMS FRONT VIEW REAR VIEW...