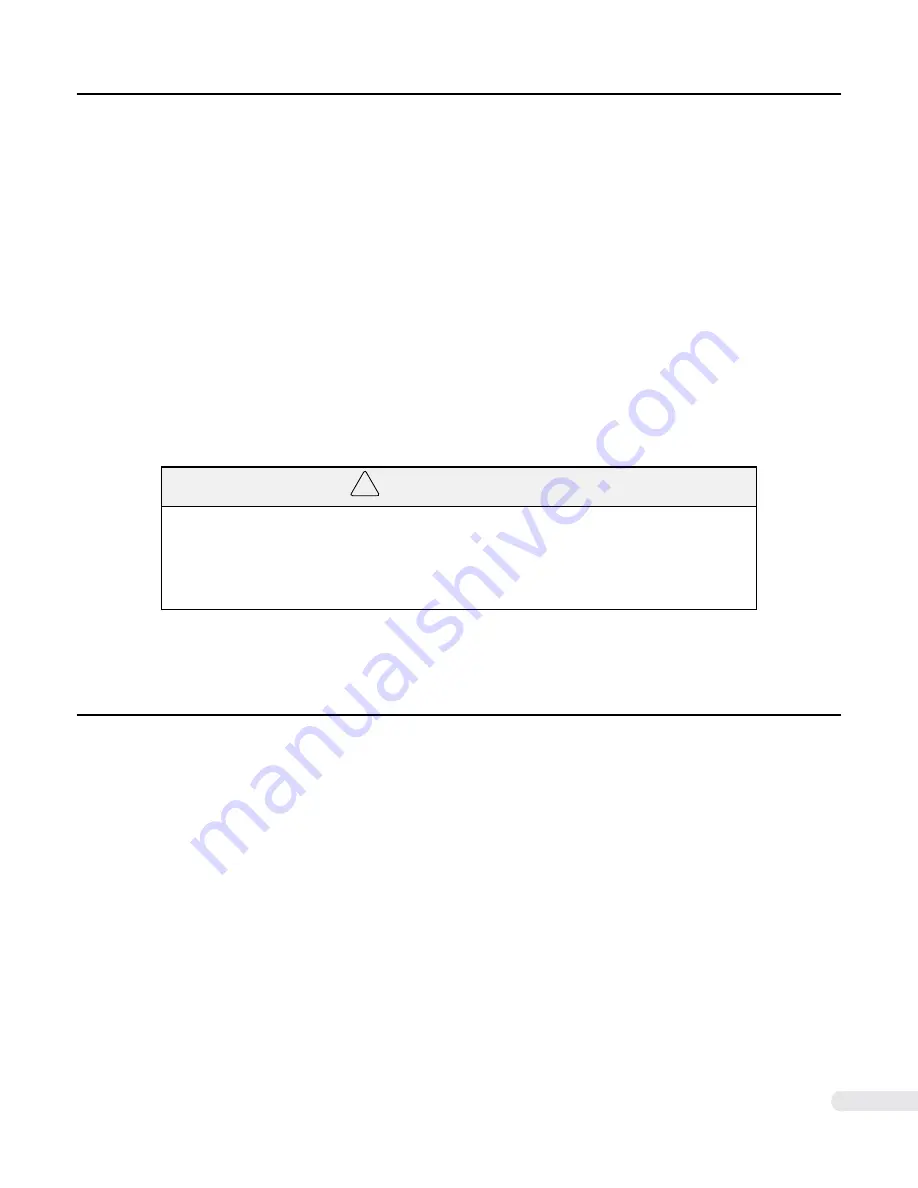
39
DYN2MS-02F-0116A17
6.1 Alarm Specifications
♦ Alarm Reset
♦ Alarm Motor Stop
The power to the servo motor will be stopped when an alarm is triggered. Internal servo control turns off
and servo motor shaft becomes free. Power still remains in the logic circuit for drive diagnostic and drive
status reading. All commands including pulse, analog and RS232 will be ignored and will not accumulate
the internal position error.
6.2 - Drive Maintenance
Do not perform maintenance on the servo drive unless instructed to do so by DMM. The servo drive cover
or chassis should never be removed as high voltage components can cause electric short, shock or other
damage upon contact. Disassembly, repairs or any other physical modification to the servo drive is not
permitted unless approved by DMM.
♦ Regular Inspection
Inspect the servo drive regularly for:
● Dirt, dust or oil on the servo drive - make sure the servo drive cooling duct and heat
sink are free from debris
● Environment - ambient temperature, humidity and vibration according to servo drive
specification
● Loose screws
● Physical damage to servo drive or internal components
Once servo drive triggers an alarm, the user should use the DMMDRV program to read out the alarm
condition then inspect the machine, load or operation for cause to the alarm. The problem should be fixed
before re-setting the servo drive and running again. The servo drive main power should be cycled to fully
re-set and clear the servo alarm status.
WARNING
!
● If the servo motor is coupled to a vertical axis that can drop due to gravity when the shaft
becomes free, take measure to prevent injury or damage when the drive alarm is triggered.
A motor with brake option may be necessary to stop vertical axis, or any axis acted on by an
external force, from dropping or crashing.