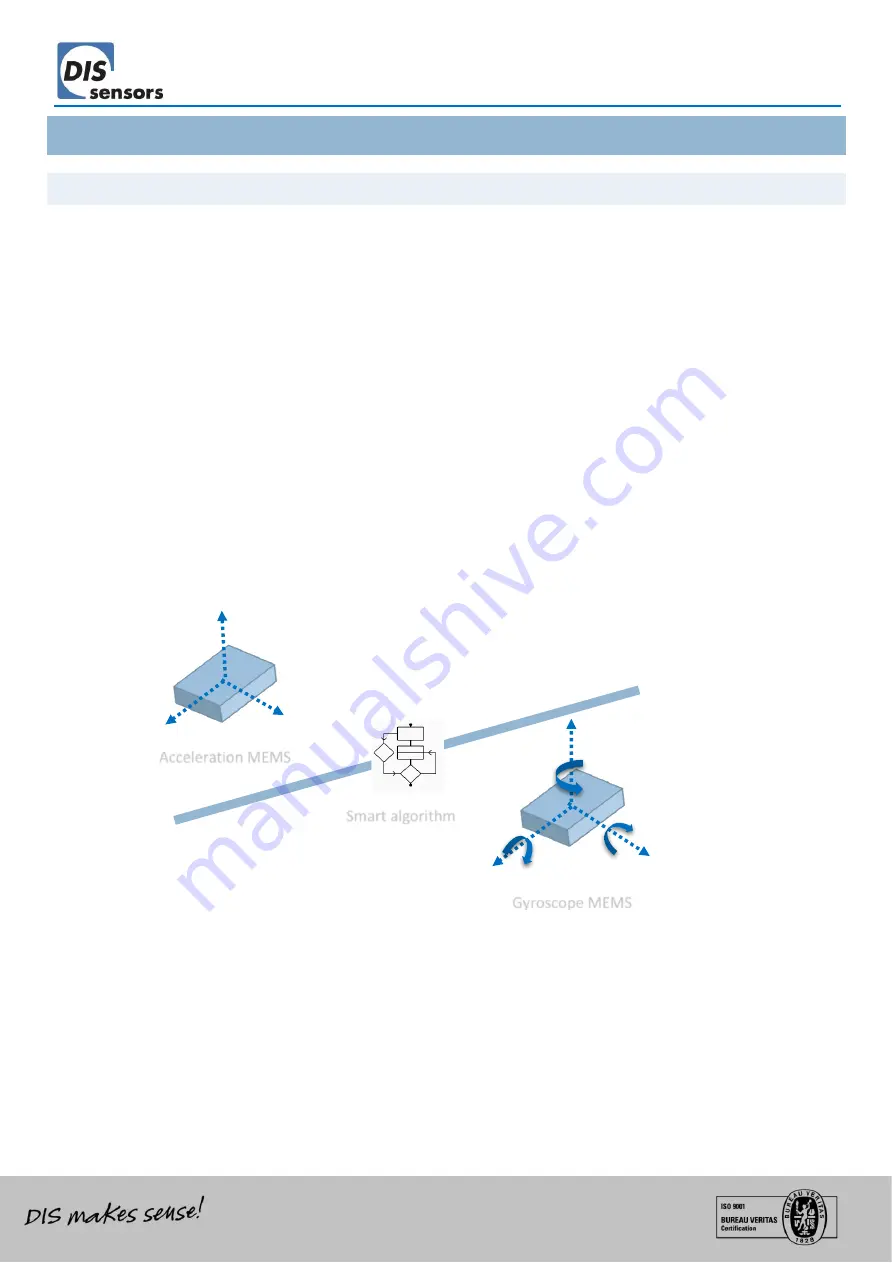
Page
10
of
50
User Manual - QG65D CANopen Dynamic Inclinometer (Type H) V2.3
6.
Functional description
6.1.
Dynamic inclination measurement principle
Conventional inclinometers measure inclination by measuring g-forces using an accelerometer. In static conditions,
inclination measurement by this principle is accurate and reliable. However, the vibrations or movements present on
almost all industrial machines generate undesirable g-forces. These dynamic g-forces accumulate and overlay the
static g-
forces, causing a ‘dirty’
inclination output that includes spurious or noise components.
In certain applications, a low-pass filter can be used to stabilize the output. The downside of this filtering is that it
significantly increases the
inclinometer’s reaction time (latency)
. In a control system, this results in a limit on the
speed of movements, and reduced machine efficiency.
A gyroscope measures the speed of rotation, which can be integrated to get the actual inclination value. But
gyroscopes are subject to bias drift, integrating constant bias will cause angular errors and these errors will
accumulate over a long term. Therefore, this calculation is only accurate for a relatively short period.
The QG65D dynamic inclinometer combines accelerometer MEMS and gyro MEMS. This device is unaffected by
vibration or movement, and can therefore measure the true angle at the sensor position in real-time. Our smart
algorithms (such as Kalman filtering) within the device can determine the balance between the accelerometer MEMS
(best result in static situations) and the gyro MEMS (best result in dynamic situations).
Figure 8 - Measurement principle of the dynamic inclinometer
Acceleration MEMS
Gyroscope MEMS
Smart algorithm