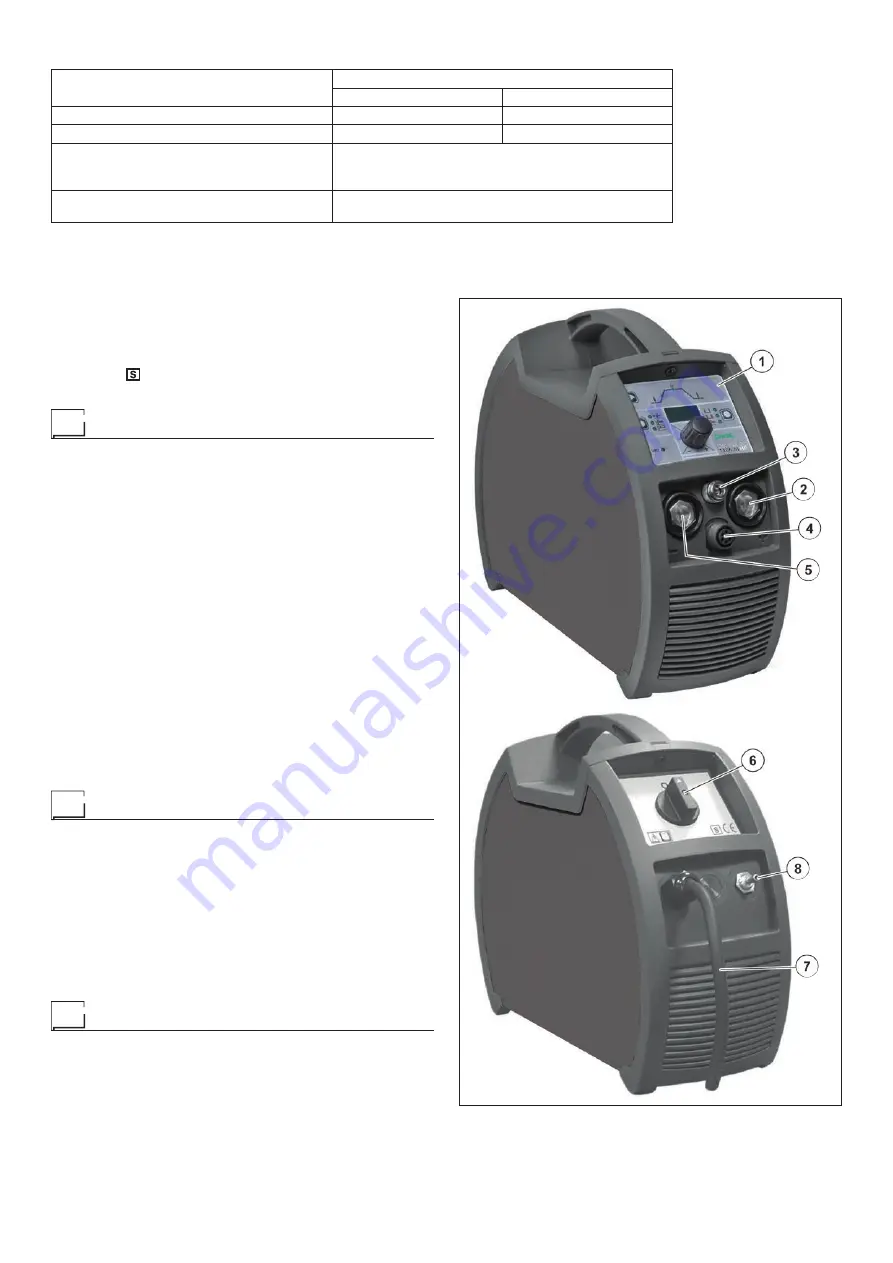
4
must therefore be placed in such a way that the air may be easily
sucked in and expelled through the apertures made in the frame.
The welding unit is characterised by the following levels:
•
Protection level IP 23 S indicates that the equipment can be used
both indoors and outdoors.
•
Use class
means that the equipment can be used in condi-
tions subject to heightened electrical shock.
Connection to the electrical supply
Before connecting the welder to the electrical supply, check
that the welding power source’s plate rating corresponds to
the supply voltage and frequency and that the line switch of
the welder is in the “O” position.
Connection to the power supply must be carried out using the trip-
olar cable supplied with the system, of which:
•
2 conducting wires are needed for connecting the welding pow-
er source to the supply.
•
The third, which is YELLOW GREEN in colour is used for mak-
ing the “EARTH” connection.
Connect a suitable load of normalised plug (2P + e) to the
power cable and provide for an electrical socket complete
with fuses or an automatic switch. The earth terminal must
be connected to the earth conducting wire (YELLOW-GREEN)
of the supply.
Table 2 shows the recommended load values for retardant sup-
ply fuses.
NOTE 1: Any extensions to the power cable must be of a suitable
diameter, and absolutely not of a smaller diameter than the spe-
cial cable supplied with the welding power source.
NOTE 2: It is not advisable to plug up the welder to motor-driv-
en generators, as they are known to supply an unstable voltage.
Instructions for use
COMMAND AND CONTROL UNITS (Fig. A)
Pos. 1
Command and control panel.
Pos. 2
Positive pole quick connection.
Pos. 3
Fast coupling TIG torch gas tube.
Pos. 4
TIG weld auxiliary control connector (torch button, re-
mote controlpedal, etc.).
Pos. 5
Negative pole quick connection.
Pos. 6
Power supply switch.
In the “O” position the welder is off.
Pos. 7
Mains cable.
Pos. 8
Weld gas inlet coupling.
TIG welding
In the TIG process welding is achieved by melting the two metal
pieces to be joined, with the possible addition of material from the
outside, using an arc ignited by a tungsten electrode. The molten
bath and the electrode are protected by and inert gas (e.g. Argon,
and a flow rate of around 8-14 litres per minute). If necessary, to
complete the welded joint, suitable additional material is added.
The type of additional material and welding current are determined
according to the type of thickness of the base material, the shape
of the joint, and the position of the weld.
1) Connecting the welding cables (Fig. B):
•
Connect the gas hose to the Argon cylinder.
FIG. A
Table 2
Model
DIX TIG GO 1406.M HF
TIG DC
MMA
Power input @ I
2
Max
kVA
8,5
9,0
Duty cycle @ X% (40°C)
A
200 (25%)*
160 (30%)*
Supply connection cable
Length
Section
m
mm
2
2,5
2,5
Earth cable
Section
mm
2
25
*
Factor of efficiency
Содержание DIX TIG GO 1406.M HF
Страница 9: ...9...