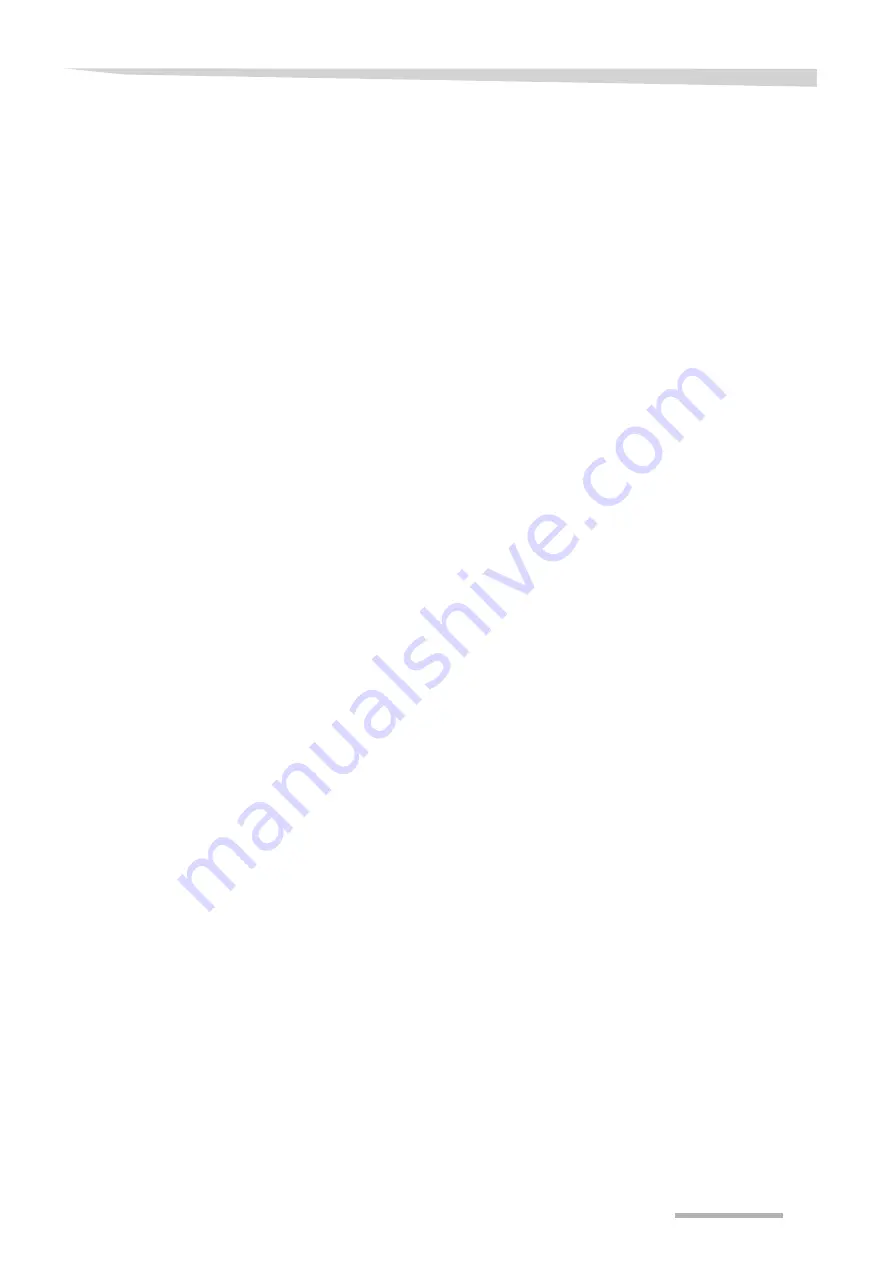
Safety
5
Safety
For your safety
Read and pay close attention to the safety instructions in this chapter
prior to assembling the machinery. Everyone involved in assembling
or installing this machine has to read and pay close attention to the fol-
lowing assembly instructions.
Warning triangles indicate the risk of serious injuries or death. When-
ever you come across these signs in the assembly instructions, please
make sure that you implement all appropriate safety measures.
They also indicate the risk of damage to the machinery as well as fi-
nancial and legal consequences (i.e. invalidation of the warranty, or le-
gal liability).
Faulty assembly or misuse results in:
•
Danger to life and limb of the operator, third parties, and animals in
the vicinity of the machine,
•
Damage to the machine and other property belonging to the oper-
ator or third parties
•
Negative effects on the efficient and faultless operation of the ma-
chine.
Assembly in
accordance with
assembly
instructions
Non-compliance with the following rules amounts to gross negligence!
It invalidates any liability of the manufacturer for resultant damage.
Non-compliance is solely at the risk of the operator!
This machine must only be assembled by trained technicians in ac-
cordance with the current revision of the assembly instructions. Before
the machine is coupled to a tractor, transported, or commissioned, the
operating manual and its safety instructions have to be thoroughly
read and followed.
It is the responsibility of the proprietor to ensure that all personnel in-
volved in the assembly are provided with the relevant accident preven-
tion regulations, as well as generally applicable health and safety and
road safety regulations. All personnel involved in the assembly have
to be aware of these rules and regulations and adhere to them; they
also have to be instructed on the potential risks and dangers.
Unauthorized alterations to the machine invalidate any liability of the
manufacturer for resultant damage.
The following rules and regulations have to be observed:
•
Relevant accident prevention regulations pertaining to the locality,
•
Generally recognized health and safety regulations as well as road
traffic legislation,
•
Functional limits and safety regulations as set out in the technical
operating manual,