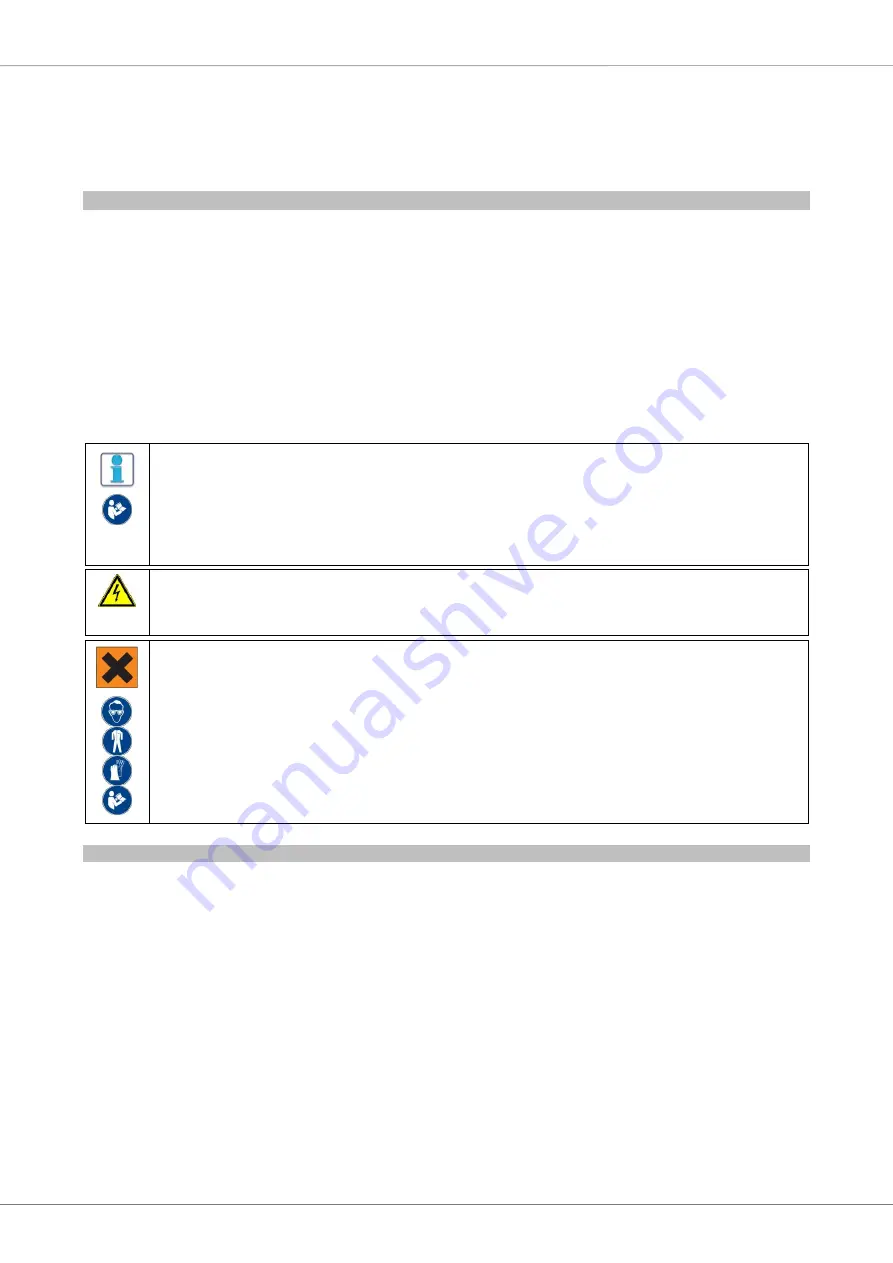
USER MANUAL
22
DESOI GmbH | Gewerbestraße 16 | D-36148 Kalbach | Phone +49 6655 9636-0 | Fax +49 6655 9636-6666 | [email protected] |
www.desoi.de
22.
As soon as there are no more air bubbles coming out of the return hose, set the desired operating pressure at the pressure
control valve. In doing so, read the pressure on the pressure gauge of the machine output. To vent and fill the material hose,
the ball valve at the end of the hose must be opened until the material escapes without air bubbles.
23.
The machine is now ready for use.
Checks after the commissioning:
It must be checked that no leaks have occurred during commissioning. Any leakage must be eliminated immediately. Increased risk of
accident!
After the first start, check the correct setting of the desired material parameters. Check the settings made. If all the desired parameters
are correct, you can start processing.
6.0
Cleaning
Contents:
Here you will learn which regular cleaning procedures are necessary in order to guarantee the functionality of the machine. Impurities
can always lead to operational disturbances. Therefore, clean when necessary, but at the latest after 8 hours:
NOTE!
•
Never leave material in the machine - always remove the material completely and clean the product and the
accessories used.
•
Always use the cleaning agent specified by the material manufacturer!
•
To keep wear to a minimum, the product should never run dry!
•
Only clean with solvents in well-ventilated rooms!
CAUTION!
Do not spray the machine with high-pressure cleaners or high-pressure steam cleaners.
•
Penetrating moisture leads to malfunctions!
CAUTION! Harmful to health!
Please note that contact with processing materials, cleaning agents, or auxiliary lubricants may cause skin irritation or
allergic shock. There may be a potential THREAT TO LIFE!
•
In the event of contact with skin, clean the affected skin areas immediately with clear water.
•
In case of contact with eyes, immediately rinse the eyes.
•
Technical data sheets and safety data sheets of the respective manufacturers of the processing medium and of
the cleaning agent must be observed and adhered to.
•
Upon any signs of infection, poisoning, or allergic reaction, seek a doctor or if necessary an emergency doctor.
•
Wear protective goggles, suitable work clothes and protective gloves.
Description:
1.
Evacuate unneeded or remaining material from the material container. Switch off the drive unit afterwards.
2.
Fill half a litre of hydraulic oil (Mobil HLP-68 or of equal quality) into the material container.
3.
Remove the overflow hose from the container, close the ball valve, open the pressure regulating valve (turn to the left, up to
the stop). Then start the drive at slow speed and convey the remaining material into a separate container.
4.
Switch off the machine and hang the overflow hose back into the material hopper. Close the pressure regulating valve (turn
to the right until it stops). Move the ball valve to the flow position and hold it in a separate container. Switch on the machine
and allow pure hydraulic oil to escape for as long as necessary. Connect them to drain the remaining hydraulic oil completely
out of the machine.
5.
Now fill 1-2 litres of cleaning agent (solvent prescribed by the material manufacturer) into the material container and start
the pump. Collect the remaining hydraulic oil from the material hose and the overflow hose and continue pumping until
clean cleaning agent escapes.
6.
Afterwards allow the system to pump the clean detergent through the circulation for five minutes (hold the material
hose into the container). Open and close the material ball valve, and increase and lower the pressure (adjust
pressure-regulation valve) during this procedure so that the detergent can reach all parts of the pump.
7.
Afterwards completely evacuate the detergent from the machine and switch the machine off.
➔