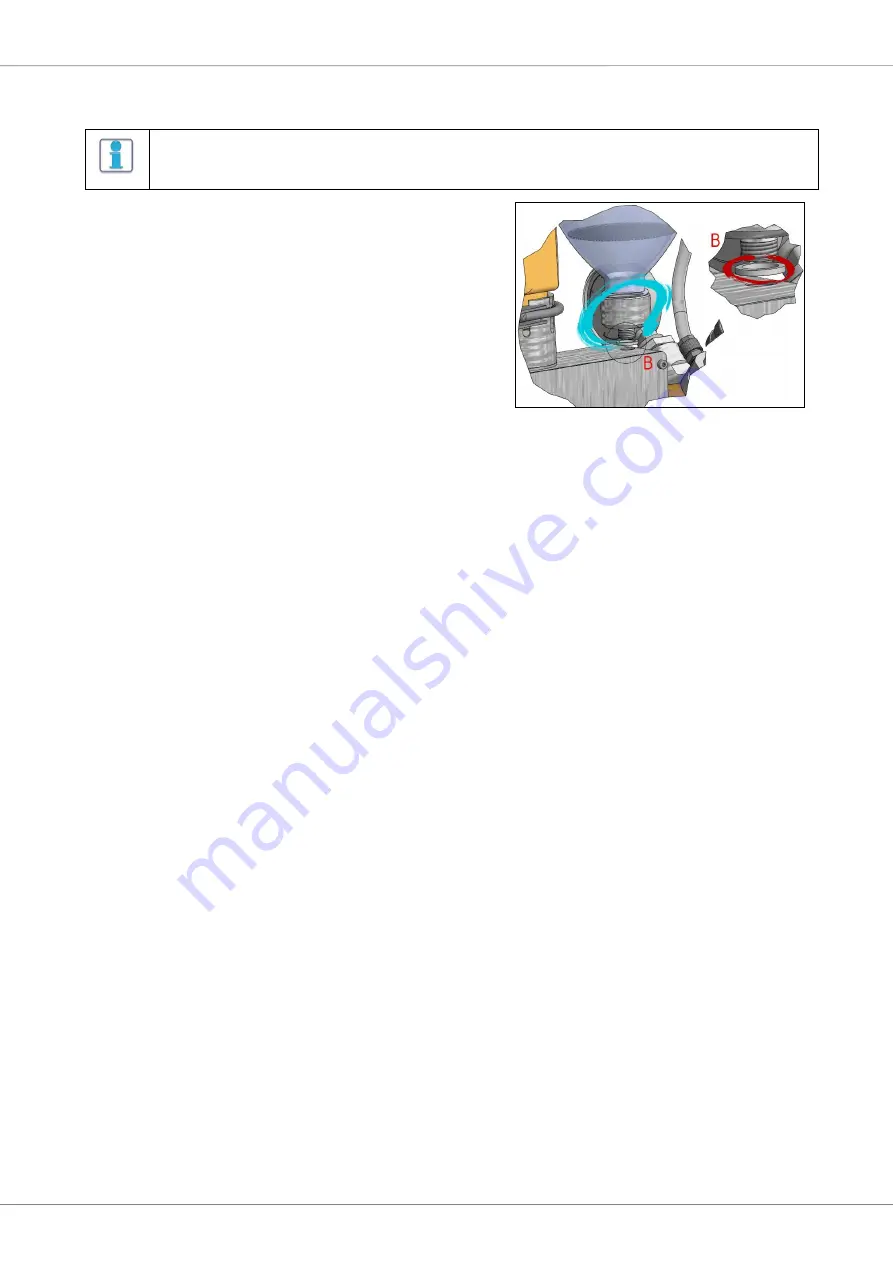
USER MANUAL
21
DESOI GmbH | Gewerbestraße 16 | D-36148 Kalbach | Phone +49 6655 9636-0 | Fax +49 6655 9636-6666 | [email protected] |
www.desoi.de
5.3 Procedure / Preparation for commissioning
NOTE!
When handling the product for the first time, it is advisable to carry out the complete first commissioning procedure purely
with hydraulic oil. In this way, any functions of the machine can be thoroughly tested without damage.
1.
Read the operating instructions in full!
2.
Check drive unit for firm and correct fit. Check safety clamp for
correct and tight fit.
3.
Check the switch positions of the drive unit
(see section 5.2 Switch
positions of the drive unit)
4.
Check material filter in the material container for cleanliness.
5.
(Fig.5.3.1)
Attach material container including the sealing ring
(
marked in red
) to the pump body. Via the adapter
(
marked in blue
), tighten the material container; if necessary a
pair of pliers may be used.
6.
Read the operating instructions in full!
Fig.5.3.1
7.
Check drive unit for firm and correct fit. Check safety clamp for correct and tight fit.
8.
Check the switch positions of the drive unit
(see section 5.2 Switch positions of the drive unit)
9.
Check material filter in the material container for cleanliness.
10.
(Fig.5.3.1)
Attach the material container including the sealing ring (
marked in red
) to the pump body. Via the adapter
(
marked in blue
), tighten the material container; if necessary a pair of pliers may be used.
11.
Attach the return line via the union screw to the thread in the area of the pressure control valve and tighten. Hook the bend
into the container.
12.
Screw the HP material hose tightly to the pump fitting provided for this purpose. Connect the ball valve to the free end of the
material hose.
13.
Connect m
ains plug to a suitable power supply (
observe safety instructions
).
14.
Pump remaining preservative oil out of the machine, plus:
•
Bring the pressure control valve to the maximum pressure position (clockwise rotation)
•
Hold the injection head in an open position over a separate container and switch on the machine. Allow the machine
to run until the entire medium has been removed.
15.
Switch off the machine.
16.
If there is any preservative oil in the return line, it can be removed in two ways.
1.
Method one: manually
▪
Ensure that the machine is switched off and depressurised. Loosen the union fitting located at the lower
end of the return line, and carefully pull the hose upwards, collecting the medium in question in a
separate container. Attach the hose and tighten the union fitting securely again.
2.
Method two: using the machine
▪
This method takes place in the course of the procedure of pumping out the remaining preservative oil
from the machine. As soon as the preservative oil, including air, escapes from the injection head, close
the injection head and bring the pressure control valve completely into the depressurised position for
approx. 3-5 seconds (
anti-clockwise rotation
). Return the pressure control valve to the maximum pressure
position. Hold the injection head over the separate container and carefully move to the open position.
Wait approx. 15 seconds before turning off the machine and closing the injection head.
17.
Add specified cleaning agent to the material container. The material filter in the container should be completely covered.
Close the injection head and move the pressure control valve to the non-pressurised open position (
anti-clockwise rotation
)
and insert the return line into the material container
18.
Start the machine and circulate the detergent for 1 minute.
19.
Hold the injection head over the material container and move it to the open position. Then return the pressure control valve
to the maximum pressure position (
clockwise rotation
) and circulate the detergent for approx. 1 minute. Then close the
injection head, the machine is pressurised.
(It may be necessary to adjust the speed via the drive unit)
20.
Hold the injection head over a separate container and carefully move it to the open position, completely removing the
cleaning agent from the machine and the return system.
21.
Add material over the side into the material container. Adjust the pressure control valve to the lowest pressure (turn to the
left until it stops). Close the injection head and turn on the pump for low speed venting (
A-B position
).