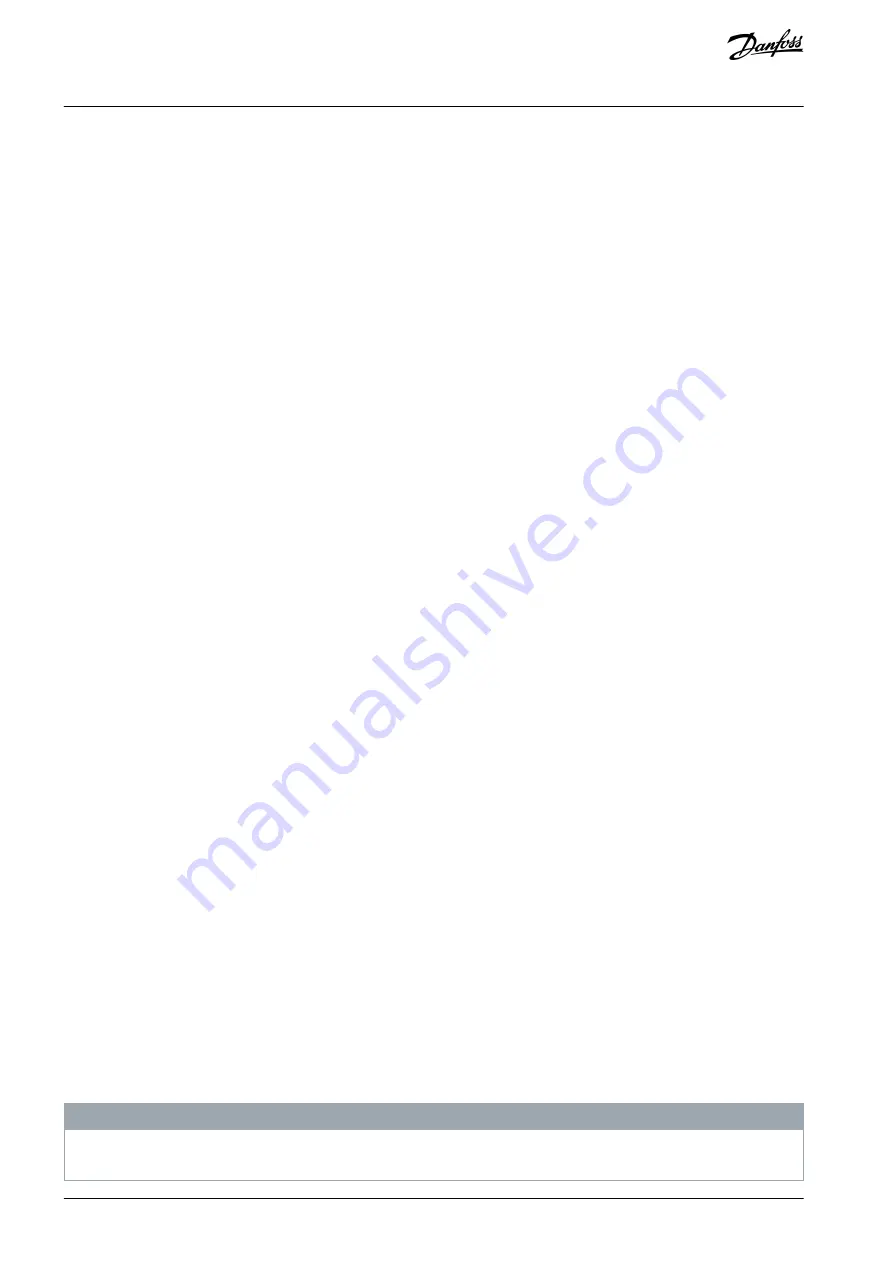
•
•
•
•
•
•
•
•
•
•
•
•
5.4 Derating
5.4.1 Manual Derating and Automatic Derating
Derating is a method used to reduce output current to avoid tripping the drive when high temperatures are reached within the
enclosure. If certain extreme operating conditions are expected, a higher-powered drive can be selected to eliminate the need for
derating. This is called manual derating. Otherwise, the drive automatically derates the output current to eliminate the excessive
heat generated by extreme conditions.
Manual derating
When the following conditions are present, Danfoss recommends selecting a drive 1 power size higher (for example P132 instead of
P110):
Low-speed – continuous operation at low RPM in constant torque applications.
Low air pressure – operating at altitudes above 1000 m (3281 ft).
High ambient temperature – operating at ambient temperatures of 10 °C (50 °F).
High switching frequency.
Long motor cables.
Cables with a large cross-section.
Automatic derating
If the following operating conditions are found, the drive automatically changes switching frequency or switching pattern (PWM to
SFAVM) to reduce excessive heat within the enclosure:
High temperature on the control card or heat sink.
High motor load or low motor speed.
High DC-link voltage.
5.4.2 Derating for Low-speed Operation
When a motor is connected to a drive, it is necessary to ensure that the cooling of the motor is adequate. The level of cooling re-
quired depends on the following:
Load on the motor.
Operating speed.
Length of operating time.
Constant torque applications (CT mode)
In a constant torque application, a motor may overheat at low speeds because the fan within the motor is providing less cooling air.
Therefore, if the motor is to be run continuously at an RPM value lower than half of the rated value, the motor must be supplied
with extra air cooling. If extra air cooling is not available, use a motor designed for low RPM/constant torque applications, or select a
larger motor to reduce the load level.
Variable (quadratic) torque applications (VT)
In variable torque applications where the torque is proportional to the square of the speed and the power is proportional to the
cube of the speed, there is no need for extra cooling or derating of the motor. Common variable torque applications are centrifugal
pumps and fans.
5.4.3 Derating for Low Air Pressure and High Altitudes
The cooling capability of air is decreased at low air pressure. For altitudes above 2000 m (6562 ft), contact Danfoss regarding PELV.
Below 1000 m (3281 ft) altitude, derating is not necessary. For altitudes above 1000 m (3281 ft), decrease the ambient temperature
or the maximum output current. Decrease the output by 1% per 100 m (328 ft) altitude above 1000 m (3281 ft) or reduce the maxi-
mum ambient cooling air temperature by 1 °C (1.8 °F) per 200 m (656 ft).
5.4.4 Derating for Ambient Temperature and Switching Frequency
Ensure that the ambient temperature measured over 24 hours is at least 5 °C (9 °F) lower than the maximum ambient temperature
that is specified for the drive. If the drive is operated at a high ambient temperature, decrease the constant output current.
N O T I C E
FACTORY DERATING
Danfoss drives have already derated for operational temperature (55 °C (131 °F) T
AMB,MAX
and 50 °C (122 °F) T
AMB,AVG
).
AJ363928382091en-000101 / 130R0983
60 | Danfoss A/S © 2021.04
Mechanical Installation
Considerations
VLT® Flow Drive FC 111
Design Guide