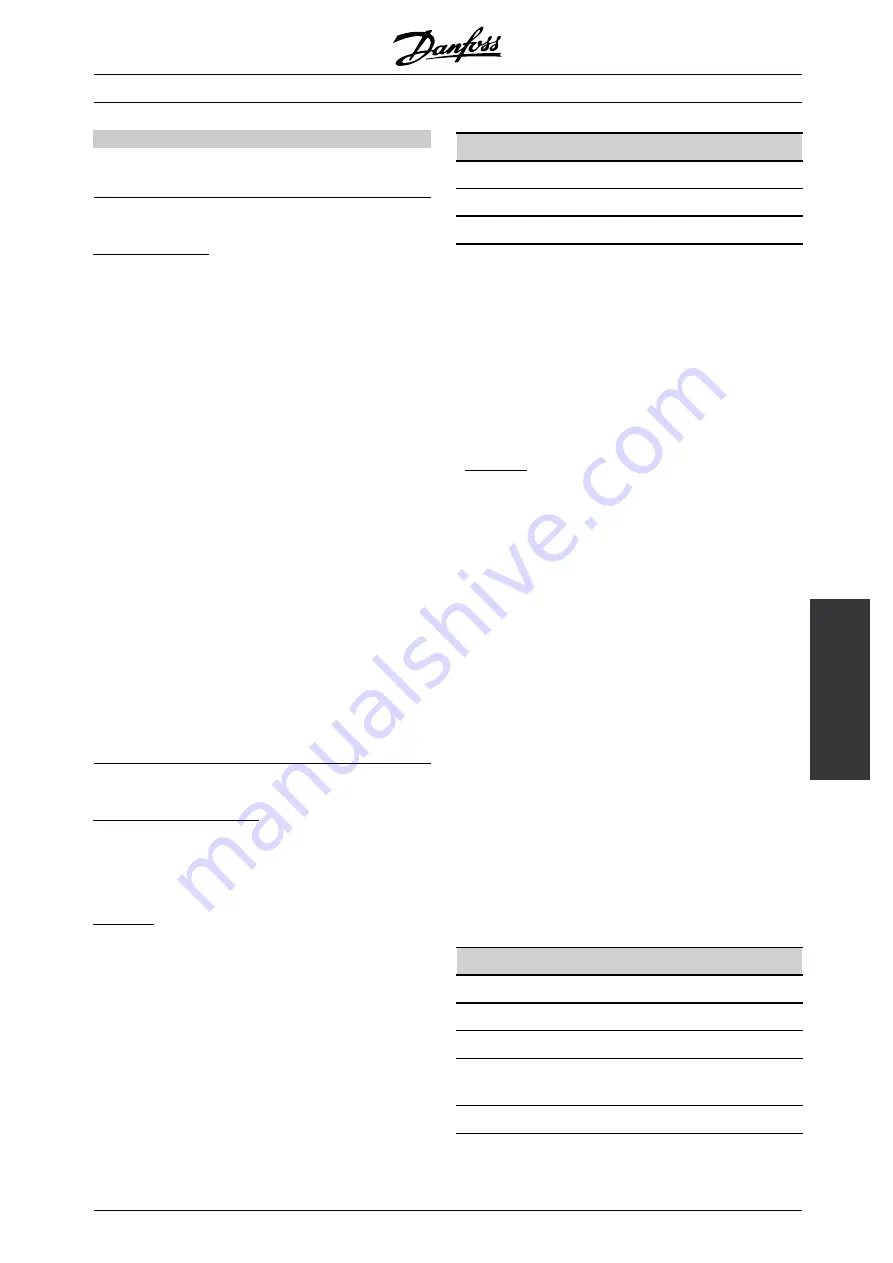
VLT
®
FCM Series
Programming
Description of choice:
Select the desired unit for the reference/feedback signal.
■
FCM 300 Regulator
Process regulation
The PID regulator maintains a constant process
mode (pressure, temperature, flow, etc.) and
adjusts the motor speed on the basis of the
reference/setpoint and feedback signal.
A transmitter provides the PID regulator with a
feedback signal from the process as an expression
of the process
’
s actual mode. The feedback signal
varies as the process load varies.
This means that there is a variance between the
reference/setpoint and the actual process mode.
This variance is compensated by the PID regulator
by means of the output frequency being regulated
up or down in relation to the variance between the
reference/setpoint and the feedback signal.
The integrated PID regulator in the frequency converter
has been optimised for use in process applications.
This means that there are a number of special functions
available in the frequency converter.
Previously it was necessary to obtain a system to
handle these special functions by installing extra I/O
modules and programming the system. With the
frequency converter the need to install extra modules
can be avoided. The parameters that are specific to the
Process Regulator are parameter 437 to parameter 444.
■
PID functions
Unit of reference/feedback
When
Process regulation, closed loop
is selected
in parameter 100
Configuration
the unit is defined
in parameter 416
Reference/feedback unit:
Feedback
A feedback range must be preset for the regulator. At
the same time this feedback range limits the potential
reference range so that if the sum of all references
lies outside the feedback range, the reference will
be limited to lie within the feedback range.
The feedback signal must be connected to a
terminal on the frequency converter. If feedback
is selected on two terminals simultaneously, the
two signals will be added together.
Use the overview below to determine which terminal is to
be used and which parameters are to be programmed.
Feedback type
Terminal
Parameters
Pulse
3
333, 327
Voltage
2
332, 338, 339
Current
1
331, 336, 337
A correction can be made for loss of voltage
in long signal cables when a transmitter with a
voltage output is used. This is done in parameters
338/339
Min./Max scaling
.
Parameters 414/415
Minimum/Maximum feedback
must also be preset to a value in the process unit
corresponding to the minimum and maximum scaling
values for signals that are connected to the terminal.
Reference
In parameter 205
Maximum reference, Ref
MAX
it is
possible to preset a maximum reference that scales the
sum of all references, i.e. the resulting reference.
The minimum reference in parameter 204 is
an expression of the minimum value that the
resulting reference can assume.
All references will be added together and the sum
will be the reference against which regulation will
take place. It is possible to limit the reference range
to a range that is smaller than the feedback range.
This can be an advantage if you want to avoid
an unintentional change to an external reference
making the sum of the references move too far away
from the optimal reference. The reference range
cannot exceed the feedback range.
If preset references are desired, they are preset
in parameters 215 to 216
Preset reference
. See
description
Reference Function
and
Handling of
References
in parameter 214.
If a current signal is used as the feedback signal,
it will only be possible to use voltage as an
analogue reference. Use the overview below to
determine which terminal is to be used and which
parameters are to be programmed.
Reference type
Terminal
Parameters
Pulse
3
333, 327
Voltage
2
332, 338, 339
Current
1
331, 336, 337
Preset
references
215-216
(241-247)
Bus reference
68+69
✭
= factory setting. () = display text [] = value for use in communication via serial communication port
MG.03.H3.02 - VLT is a registered Danfoss trademark
63