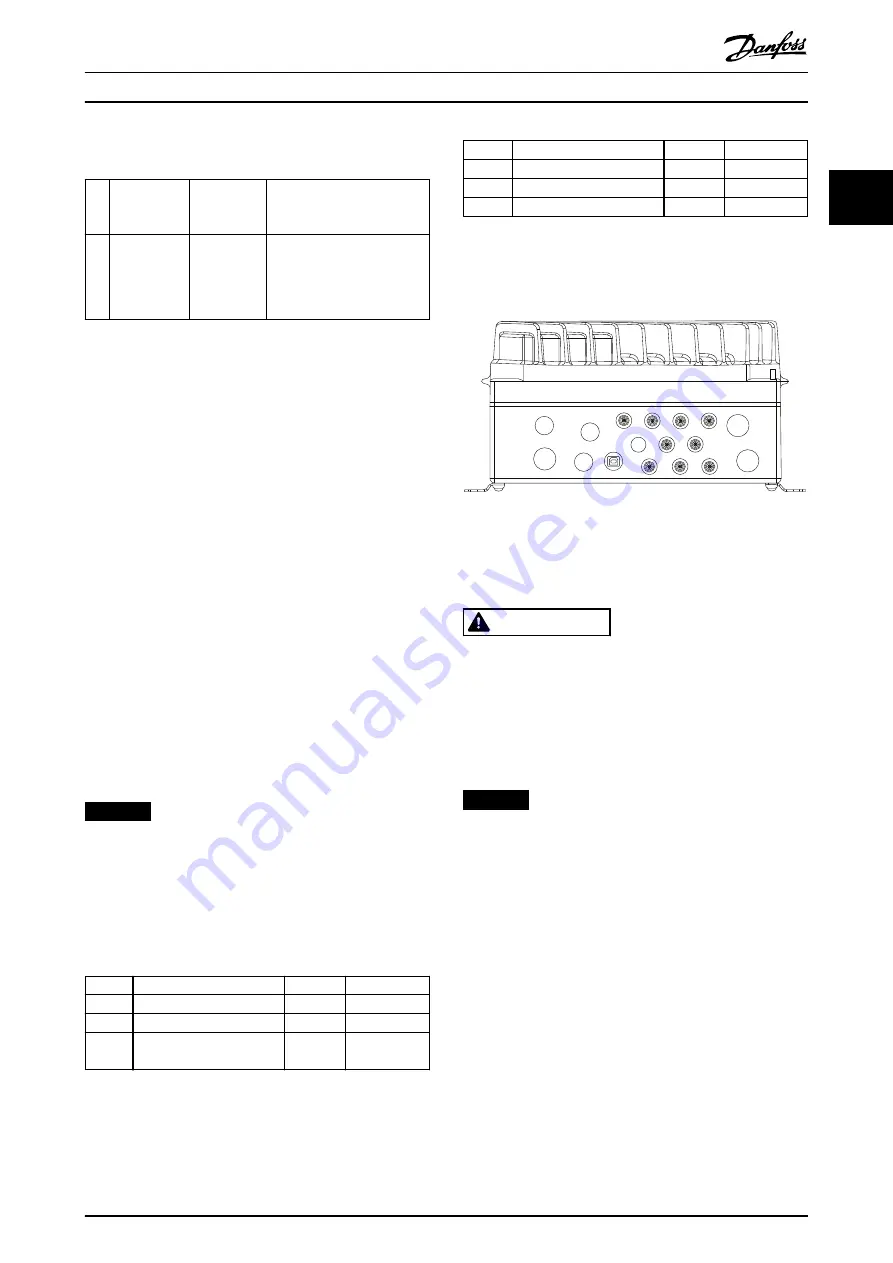
2.4.9 Mechanical Brake
No. 122 (optional
function)
123
(optional
function)
MBR+
MBR-
Mechanical brake
UDC = 0.45 x RMS mains
voltage
max. current = 0.8 A
Table 2.5 Mechanical Brake Terminals
In hoisting/lowering applications, control of electro-
mechanical brake is required:
•
The brake is controlled using the special
mechanical brake control/supply terminals 122
and 123.
•
Select
[32] Mechanical brake control
in parameter
group 5-4*,
[1] Array,
Relay 2 for applications with
an electro-mechanical brake.
•
The brake is released when the motor current
exceeds the preset value in
parameter 2-20 Release Brake Current
.
•
The brake is engaged when the output frequency
is less than the frequency set in
parameter 2-21 Activate Brake Speed [RPM]
or
parameter 2-22 Activate Brake Speed [Hz]
. The
brake engages only when the frequency
converter performs a stop command.
When the frequency converter enters alarm mode or is
exposed to an over-voltage situation, the mechanical brake
immediately cuts in. For more detailed information, refer to
the
VLT
®
Decentral Drive FCD 302 Programming Guide
.
NOTICE
When the Mechanical Brake Control/Supply terminals 122
and 123 are set through parameter group 5-4*,
[1] Array
,
Relay 2, only one relay output (Relay 1) is available for
free programming.
2.4.10 Connection of Sensors/Actuators on
M12 Sockets
Pin
Wire colour
Terminal
Function
1
Brown
12
+24 V
3
Blue
20
0 V
4
Black
18, 19, 32,
33
Digital input
Table 2.6 4xM12 Connection Input
Pin
Wire colour
Terminal
Function
1
Brown
Reserved* Reserved
3
Blue
20
0 V
4
Black
02, 05
N.O. (24 V)
Table 2.7 2xM12 Connection Output
* When reserved wires for option are used. If not utilised, they can be
cut off.
130BC389.10
1
2
3
4
1
2
3
4
1
2
3
4
1
2
3
4
1
2
3
4
1
2
3
4
1
2
3
4
LCP
RL2
RL1
33
USB
32
19
FB2
FB1
18
1
2
3
4
1
2
3
4
Illustration 2.17 Connectors for Sensors/Actuators
2.4.11 Earth (Grounding) Requirements
WARNING
GROUNDING HAZARD
For operator safety, it is important to ground frequency
converter properly in accordance with national and local
electrical codes as well as instructions contained within
this manual. Ground currents are higher than 3.5 mA.
Failure to ground frequency converter properly could
result in death or serious injury.
NOTICE
It is the responsibility of the user or certified electrical
installer to ensure correct grounding (earthing) of the
equipment in accordance with national and local
electrical codes and standards.
•
Proper protective grounding for equipment with
ground currents higher than 3.5 mA must be
established, see
Leakage Current (3.5 mA)
following.
•
A dedicated ground wire is required for input
power and motor.
•
Use the clamps provided with on the equipment
for proper ground connections.
•
Use of high-strand wire to reduce electrical noise
is recommended.
Installation
Operating Guide
MG04F402
Danfoss A/S © 05/2016 All rights reserved.
21
2
2