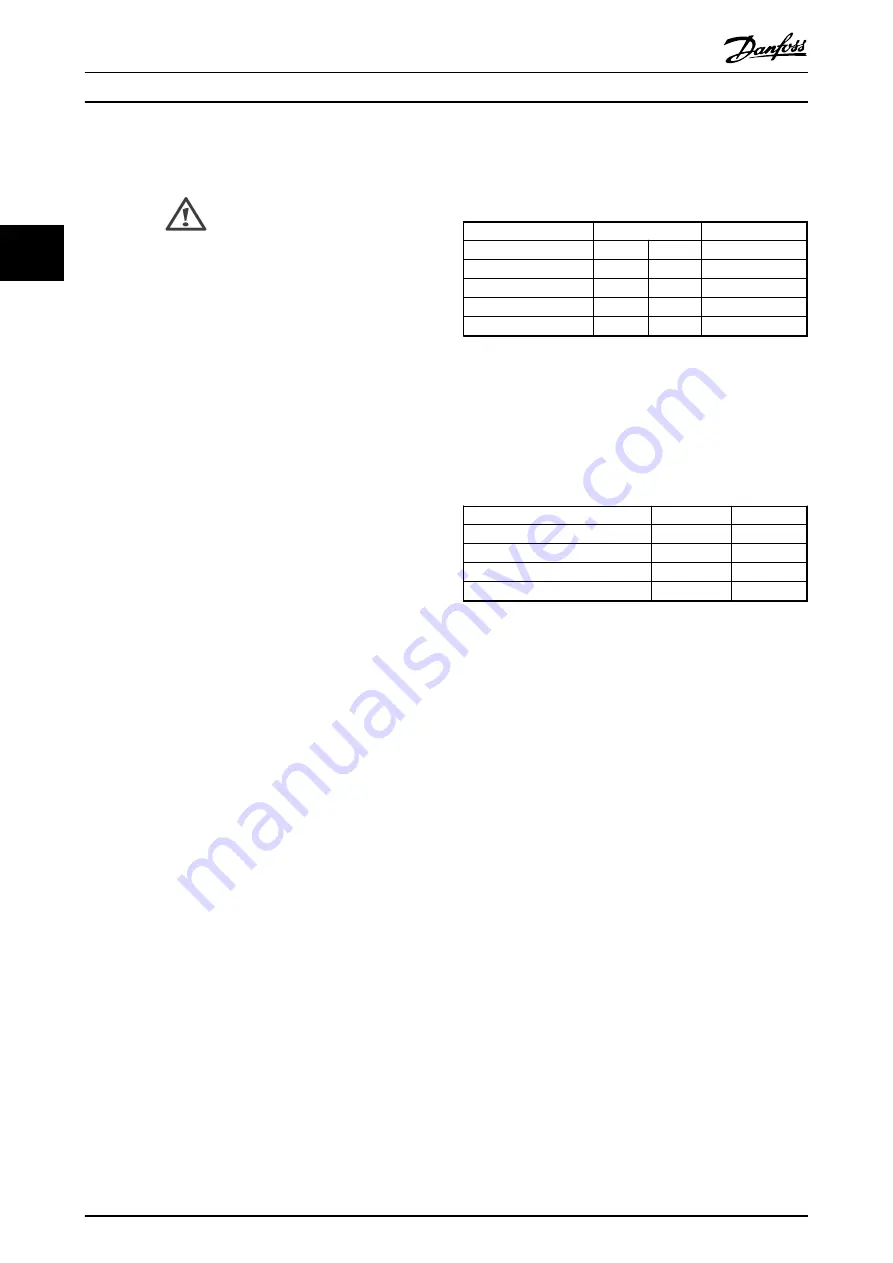
the motor cannot run. The stop will be effected in
accordance with the selected ramp (parameters 207/208).
Start
, is selected if a start/stop command is desired. Logic
'1' = start, logic '0' = stop (stand-by).
Latched start
- if a pulse is applied for min. 20 ms, the
motor will start, provided no stop command. The motor
stops if Stop inverse is activated briefly.
Reversing
is used for changing the direction of rotation of
the motor shaft. Logic "0" will not lead to reversing. Logic
"1" will lead to reversing. The reversing signal only changes
the direction of rotation; it does not activate the start
function.
Should not be used with
Process, closed loop mode
.
Start reversing
, is used for start/stop and for reversing with
the same signal. No start signal is allowed at the same
time. Acts as latch start reversing, provided latch start has
been chosen for another terminal.
Should not be used with
Process, closed loop mode
.
Start clockwise
is used if the motor shaft is only to be able
to rotate clockwise when starting.
Should not be used with
Process, closed loop mode
.
Start counter-clockwise, on
is used if the motor shaft is to
be able to rotate counter-clockwise when started.
Should not be used with
Process, closed loop mode
.
Jog
is used for overriding the output frequency to the jog
frequency set in parameter 213. The ramp time can be set
in parameter 211. Jog is not active if a stop command has
been given (start-disable).
Jog overrides stand-by.
Freeze reference
- freezes the actual reference. The frozen
reference is now the point of enable/ condition for
Speed
up
and
Speed down
to be used.
If speed up/down is used, the speed change always follows
the normal ramp (parameters 207/208) in the range 0 -
Ref
MAX
.
Freeze output
- freezes the actual motor frequency (Hz).
The frozen motor frequency is now the point of enable/
condition for
Speed up
and
Speed down
to be used.
Freeze output overrides start/stand-by, slip compensation
and closed loop process control.
If speed up/down is used, the speed change always follows
the normal ramp (parameters 207/208) in the range 0 -
f
M,N
.
Speed up
and
Speed down
are selected if digital control of
the up/down speed is desired (motor potentiometer). This
function is only active if
Freeze reference
or
Freeze output
has been selected.
As long as there is a logic ‘1‘ on the terminal selected for
speed up, the reference or the output frequency will
increase.
As long as there is a logic ‘1‘ on the terminal selected for
speed down, the reference or the output frequency will be
reduced.
Pulses (logic ‘1‘ minimum high for 20 ms and a minimum
pause of 20 ms) will lead to a change of speed of 0.1%
(reference) or 0.1 Hz (output frequency).
Terminal
Freeze ref./
2-5
2-5
Freeze output
No speed change
0
0
1
Speed down
0
1
1
Speed up
1
0
1
Speed down
1
1
1
Table 3.12 Example:
Selection of Setup,
enables a choice of one of the two
Setups; however, this presupposes that parameter 004 has
been set to
Multi Setup
.
Catch-up/Slow-down
is selected if the reference value is to
be increased or reduced by a programmable percentage
value set in parameter 219.
Slow-down
Catch-up
Unchanged speed
0
0
Reduced by %-value
1
0
Increased by %-value
0
1
Reduced by %-value
1
1
Table 3.13
Preset reference
enables a choice of one of the two preset
references, in accordance with the table in parameter 215
and 216. To be active,
Preset reference
, on has to be
selected.
Preset reference
is used for shifting between external
reference and preset reference. It is assumed that
[2]
External/preset
has been selected in parameter 214. Logic
'0' = external references active; logic '1' = one of the two
preset references is active.
Precise stop
corrects the ramp-down time to obtain a high
repetitive accuracy of the stopping point.
Pulse reference
is selected if a pulse sequence (frequency)
of 0 Hz is used, corresponding to Ref
MIN
, parameter 204.
The frequency is set in parameter 327, corresponding to
Ref
MAX
.
Pulse feedback
is selected if a pulse sequence (frequency) is
selected as a feedback signal. See also parameter 327.
Analogue reference
is selected to enable change of
reference by means of an analogue reference signal.
If other inputs are connected, these are added up, taking
account of their signs.
Analogue feedback
is selected if closed loop regulation with
an analogue signal is used.
Reset and start
is used for activating start at the same time
as reset.
Freeze reference and start,
both a START and a FREEZE
REFERENCE command will be initiated. When using SPEED
UP/SPEED DOWN both FREEZE REFERENCE and START must
be activated. By implementing this feature a digital input
can be spared.
Programming
VLT
®
DriveMotor FCM Series
50
MG03BA02 - VLT
®
is a registered Danfoss trademark
3
3
Содержание VLT Brook Crompton Motor FCM 300
Страница 1: ...MAKING MODERN LIVING POSSIBLE Design Guide VLT Brook Crompton Motor FCM 300 www danfoss com drives...
Страница 2: ......
Страница 26: ...Illustration 2 5 Installation VLT DriveMotor FCM Series 24 MG03BA02 VLT is a registered Danfoss trademark 2 2...
Страница 37: ...Programming VLT DriveMotor FCM Series MG03BA02 VLT is a registered Danfoss trademark 35 3 3...
Страница 101: ...Index VLT DriveMotor FCM Series MG03BA02 VLT is a registered Danfoss trademark 99...
Страница 102: ...www danfoss com drives MG03BA02 175R0087 MG03BA02 Rev 2011 12 22...