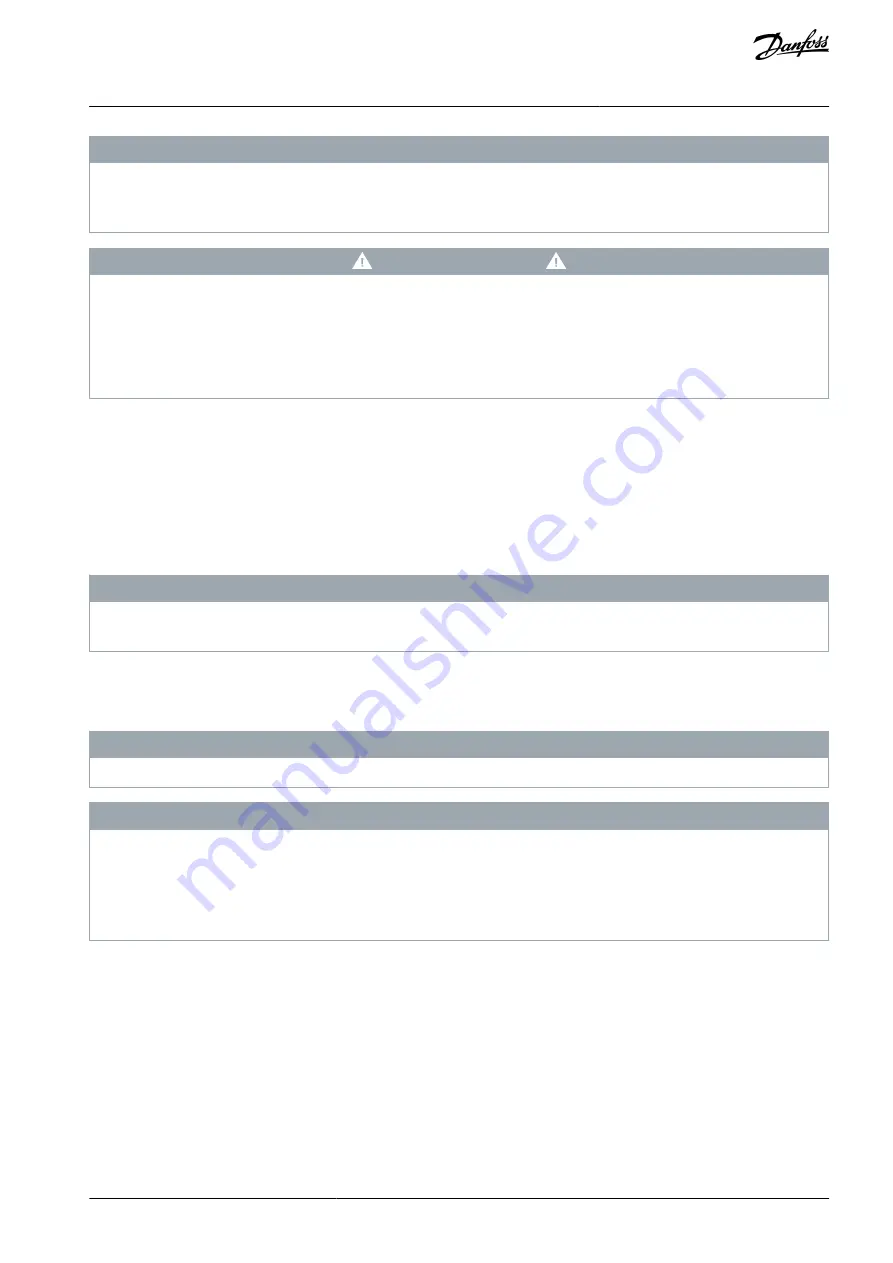
-
-
N O T I C E
If a short circuit occurs in the brake transistor, power dissipation in the brake resistor is only prevented by using a mains switch or
contactor to disconnect the mains from the drive. Alternatively, use a switch in the brake circuit. Uninterrupted power dissipation
in the brake resistor can cause overheating, damage, or fire.
W A R N I N G
RISK OF FIRE
The brake resistors become hot during braking. Failure to place the brake resistor in a secure area can result in property damage
and/or serious injury.
Ensure that the brake resistor is placed in a secure environment to avoid fire risk.
Do no touch the brake resistor during or after braking to avoid serious burns.
10.9.2 Control with Brake Function
A relay/digital output can be used to protect the brake resistor against overloading or overheating by generating a fault in the drive.
If the brake IGBT is overloaded or overheated, the relay/digital output signal from the drive to the brake turns off the brake IGBT. The
relay/digital output signal does not protect against a short circuit in the brake IGBT or a ground fault in the brake module or wiring.
If a short circuit occurs in the brake IGBT, Danfoss recommends a means to disconnect the brake.
Furthermore, the brake enables reading out the momentary power and the average power of the latest 120 s. The brake can moni-
tor the power energizing and make sure that it does not exceed the limit selected in the brake monitor function. Consult the Oper-
ating Guide for more details.
N O T I C E
Monitoring the brake power is not a safety function. A thermal switch connected to an external contactor is required for that
purpose. The brake resistor circuit is not ground-leakage protected.
Overvoltage control (OVC) can be selected as an alternative brake function in parameters for overvoltage control. This function is
active for all units and ensures that if the DC-link voltage increases, the output frequency also increases to limit the voltage from the
DC link, which avoids a trip.
N O T I C E
OVC cannot be activated when running a PM motor, while parameters for motor construction is set to PM non-salient SPM.
N O T I C E
MORE REQUIREMENTS FOR BRAKING APPLICATIONS
When the motor brakes the machinery, the DC-link voltage of the drive increases. The effect of the increase equals an increase of
the motor supply voltage of up to 20%. Consider this voltage increase when specifying the motor insulation requirements if the
motor will be braking a large part of its operational time.
Example:
Motor insulation requirement for a 400 V AC mains voltage
application must be selected as if the drive were supplied with 480 V.
10.10 Residual Current Device
Use RCD relays, multiple protective earthing, or grounding as extra protection to comply with local safety regulations. If a ground
fault appears, a DC content may develop in the faulty current. If RCD relays are used, local regulations must be observed. Relays
must be suitable for protection of 3-phase equipment with a bridge rectifier and for a brief discharge on power-up using RCDs.
10.11 Leakage Current
Follow national and local codes regarding protective earthing of equipment where leakage current exceeds 3.5 mA.
Drive technology implies high frequency switching at high power. This generates a leakage current in the ground connection.
The ground leakage current is made up of several contributions and depends on various system configurations, including:
AJ300847815559en-000101 / 130R0337 | 141
Danfoss A/S © 2020.09
Electrical Installation
Considerations
VLT® AQUA Drive FC 202
Design Guide