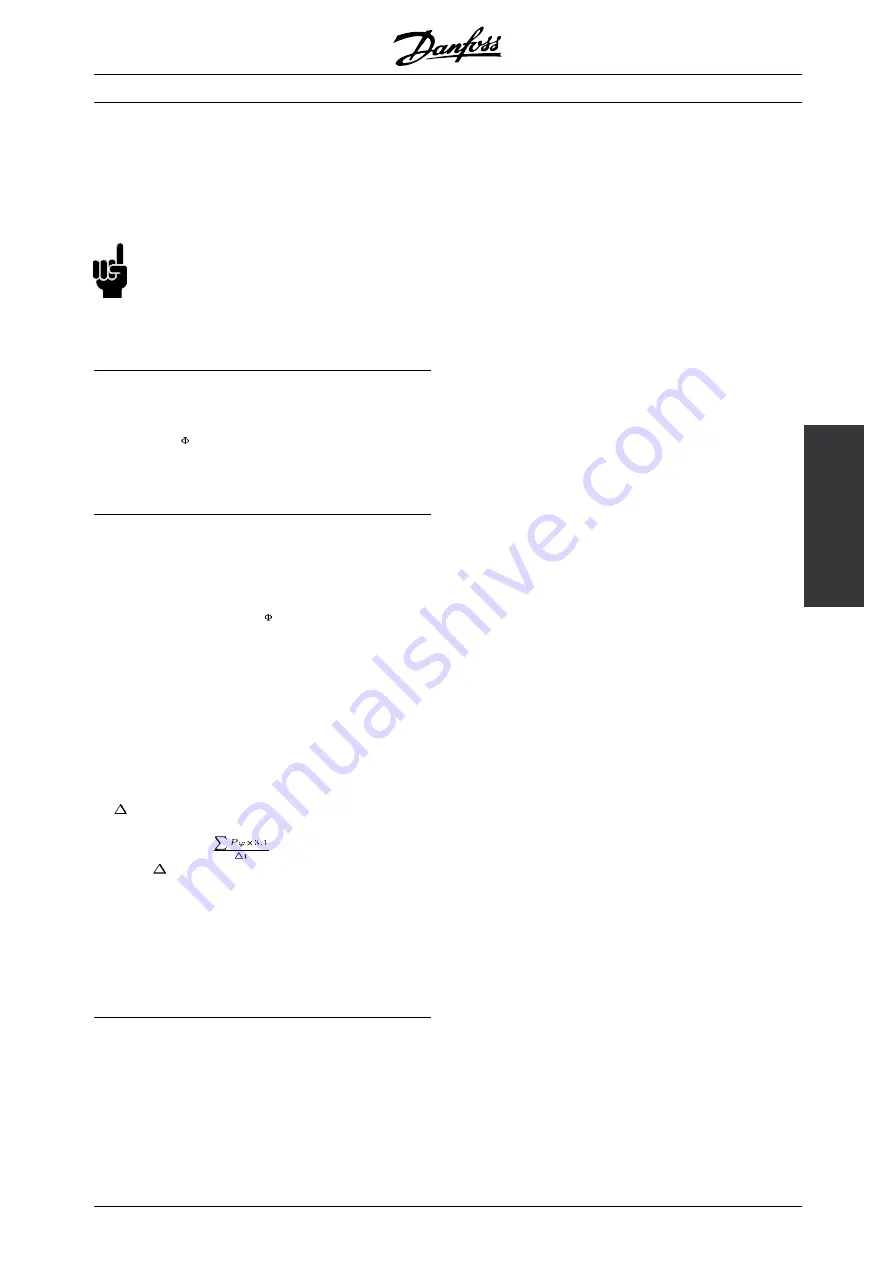
VLT
®
6000 HVAC Series
Installation
■
High voltage test
A high voltage test can be carried out by short-circuiting
terminals U, V, W, L1, L2 and L3 and energizing
by max. 2.5 kV DC for one second between
this short-circuit and the chassis.
NB!:
The RFI switch must be closed (position
ON) when high voltage tests are carried out.
The mains and motor connection must be
interrupted in the case of high voltage tests of the total
installation if the leakage currents are too high.
■
Heat emission from VLT 6000 HVAC
The tables in
General technical data
show the
power loss P
(W) from VLT 6000 HVAC. The
maximum cooling air temperature t
IN MAX
, is 40°
at 100% load (of rated value).
■
Ventilation of integrated VLT 6000 HVAC
The quantity of air required for cooling frequency
converters can be calculated as follows:
1.
Add up the values of P
for all the frequency
converters to be integrated in the same panel.
The highest cooling air temperature (t
IN
) present
must be lower than t
IN, MAX
(40°C). The day/night
average must be 5°C lower (VDE 160). The
outlet temperature of the cooling air must not
exceed: t
OUT, MAX
(45° C).
2.
Calculate the permissible difference between
the temperature of the cooling air (t
IN
) and
its outlet temperature (t
OUT
):
t = 45° C-t
IN
.
3.
Calculate the required
quantity of air =
m
3
/h
insert
t in Kelvin
The outlet from the ventilation must be placed above
the highest-mounted frequency converter. Allowance
must be made for the pressure loss across the
filters and for the fact that the pressure is going
to drop as the filters are choked.
■
EMC correct electrical installation
Following these guidelines is recommended in cases
where compliance with EN 61000-6-3/4, EN 55011
or EN 61800-3
First environment
is required. If the
installation is in EN 61800-3
Second environment
, then
it is acceptable to deviate from these guidelines. It is
however not recommended. See also
CE labelling,
Emission
and
EMC test results
under special conditions
in the Design Guide for further details.
Good engineering practice to ensure EMC
correct electrical installation:
•
Use only braided screened/armoured motor
cables and control cables.
The screen should provide a minimum coverage
of 80%. The screen material must be metal,
not limited to but typically copper, aluminium,
steel or lead. There are no special requirements
for the mains cable.
•
Installations using rigid metal conduits are not
required to use screened cable, but the motor
cable must be installed in conduit separate from
the control and mains cables. Full connection
of the conduit from the drive to the motor is
required. The EMC performance of flexible
conduits varies a lot and information from the
manufacturer must be obtained.
•
Connect the screen/armour/conduit to earth
at both ends for motor cables and control
cables. See also
Earthing of braided screened/
armoured control cables.
•
Avoid terminating the screen/armour with twisted
ends (pigtails). Such a termination increases the
high frequency impedance of the screen, which
reduces its effectiveness at high frequencies. Use
low impedance cable clamps or glands instead.
•
Ensure good electrical contact between the
mounting plate and the metal chassis of the
frequency converter. This does not apply
to IP54 units as they are designed for wall
mounting and VLT 6152-6602, 380-480 V, VLT
6102-6652, 525-600 V, VLT 6042-6062, 200-240
VAC in IP20/NEMA1 enclosure.
•
Use starwashers and galvanically conductive
installation plates to secure good electrical
connections for IP00, IP20, IP21 and
NEMA 1 installations.
•
Avoid using unscreened/unarmoured motor
or control cables inside cabinets housing the
drive(s), where possible.
•
An uninterrupted high frequency connection
between the frequency converter and the motor
units is required for IP54 units.
The illustration shows an example of an EMC correct
electrical installation of an IP20 or NEMA 1 frequency
converter. The frequency converter has been fitted
in an installation cabinet with an output contactor
and connected to a PLC, which in this example
is installed in a separate cabinet. Other ways of
MG.61.A5.02 - VLT is a registered Danfoss trademark
53