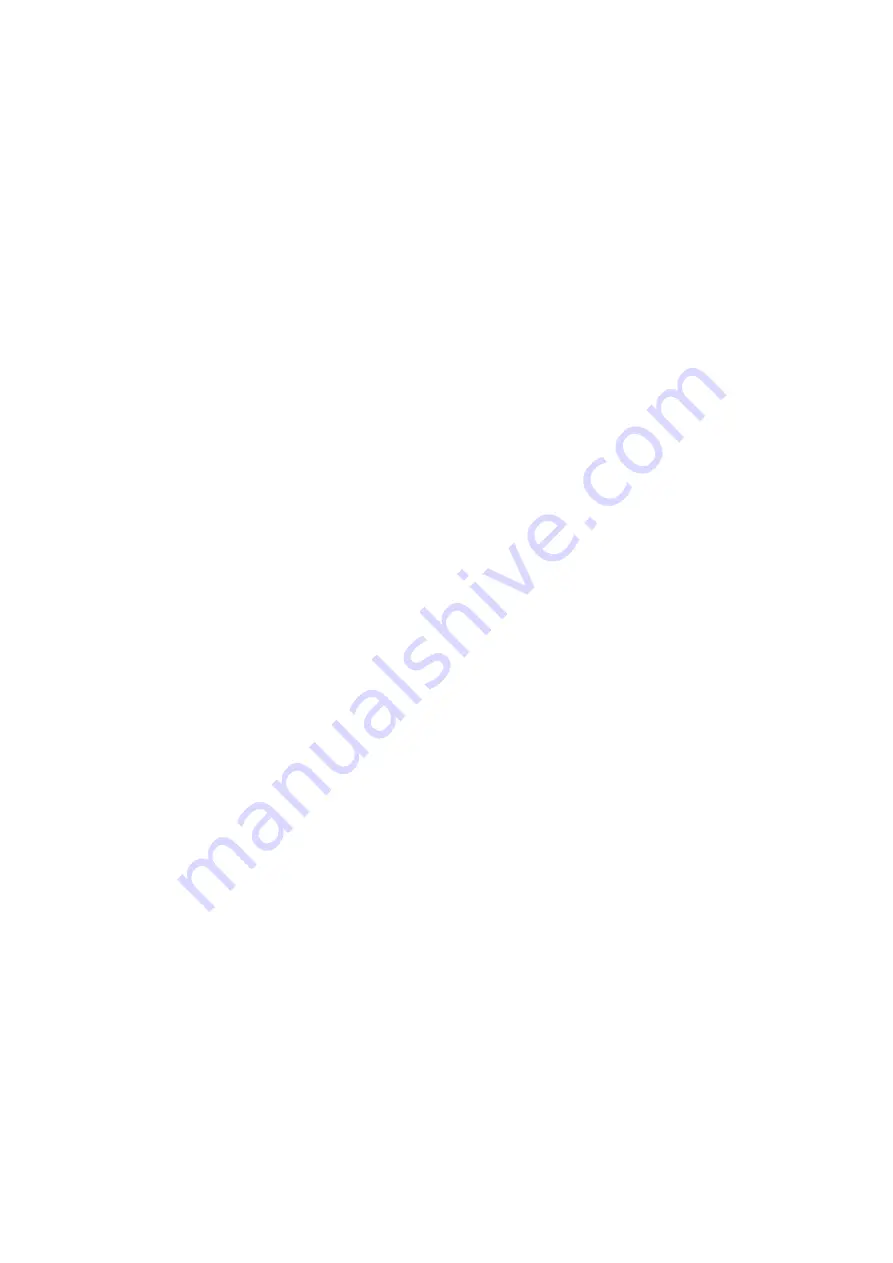
D
– EIMWC00509-13EN - 22/48
Description of the refrigeration cycle with partial heat recovery
The low-temperature refrigerant gas from the evaporator is drawn by the compressor through the electric motor, which is
cooled by the refrigerant. It is subsequently compressed and during this process the refrigerant mixes with the oil from
the oil separator.
The high-pressure oil-refrigerant mixture is introduced into the centrifuge -type high-efficiency oil separator, where the oil
is separated from the refrigerant. The oil accumulated on the bottom of the separator is forced by the pressure difference
back into the compressor while the oil-free refrigerant is sent to the condenser. The upper part of the condenser has
cooling tubes through which about 10% of the heat rejection of the unit is recovered.
These condensers, with partial heat recovery tubes, have crowns with special couplings by which they can be connected
to the hot water pipes. W hen partial recovery is activated, condenser performance is improved since the condenser
temperature is lowered further in as much as the surface dedicated to heat discharge is greater.
After passing through the cooling tubes, the gas starts to condense in the central part of the condenser.
The condensed fluid at saturation temperature passes through the subcooling section where it looses even more heat,
increasing the efficiency of the cycle. The subcooled fluid flows through the high-efficiency filter dryer and then reaches
the expansion element (expansion valve) through which a fall in pressure starts off the expansion process resulting in the
vaporisation of part of the refrigerant liquid.
The result at this point is a low-pressure and low-temperature liquid-gas mixture entering the evaporator, where it takes
the heat required for vaporisation.
When the refrigerant liquid-vapour is uniformly distributed in the direct expansion evaporator tubes, heat is exchanged
with the cooling water, thus reducing the temperature until complete evaporation, followed by superheating.
Once it has reached the superheated-vapour state, the refrigerant leaves the evaporator and is once again taken into the
compressor to repeat the cycle.
Controlling the partial recovery circuit and installation recommendations
The partial heat recovery system is not managed and/or controlled by the machine. The installer should follow the
suggestions below for best system performance and reliability:
1)
Install a mechanical filter on the heat exchanger inlet pipe.
2)
Install shut-off valves to isolate the heat exchanger from the water system during periods of inactivity or
system maintenance.
3)
Install a drain valve that allows the heat exchanger to be emptied in the even that air temperature is
expected to fall below 0°C during periods of inactivity of the machine.
4)
Install flexible anti-vibration joints on the heat recovery water inlet and outlet piping, so that
transmission of vibrations, and therefore of noise, to the water system is kept as low as possible.
5)
Do not load exchanger joints with the weight of the heat recovery piping. The water joints of the
exchangers are not designed to support the weight of the piping.
6)
Should heat recovery water temperature be lower than ambient temperature, it is advised to switch off
the heat recovery water pump 3 minutes after having switched off the last compressor.
Compressor
The single-screw compressor is of the semi-hermetic type with an asyncronous three-phase, two-pole motor which is
directly splined on the main shaft. The suction gas from the evaporator cools the electric motor before entering the
suction ports. There are temperature sensors inside the electric motor which are completely covered by the coil winding
and constantly monitor motor temperature. Should the coil winding temperature become very high (120°C), a special
external device connected to the sensors and to the electronic controller will deactivate the corresponding compressor.
There are only two moving rotating parts and there are no other parts in the compressor with an eccentric and/or
alternating movement.
The basic components are therefore only the main rotor and the satellites that carry out the compression process,
meshing perfectly together.
Compression sealing is done thanks to a suitably shaped special composite material that is interposed between the main
screw and the satellite. The main shaft on which the main rotor is splined is supported by 2 ball bearings. The system
made up in this way is both statically and dynamically balanced before assembly.
Содержание EWWQ380B-SS
Страница 8: ...D EIMWC00508 16EN 8 48 Fig 1 Lifting the unit...
Страница 45: ...D EIMWC00508 16EN 45 48...
Страница 46: ...D EIMWC00508 16EN 46 48...
Страница 47: ...D EIMWC00508 16EN 47 48...