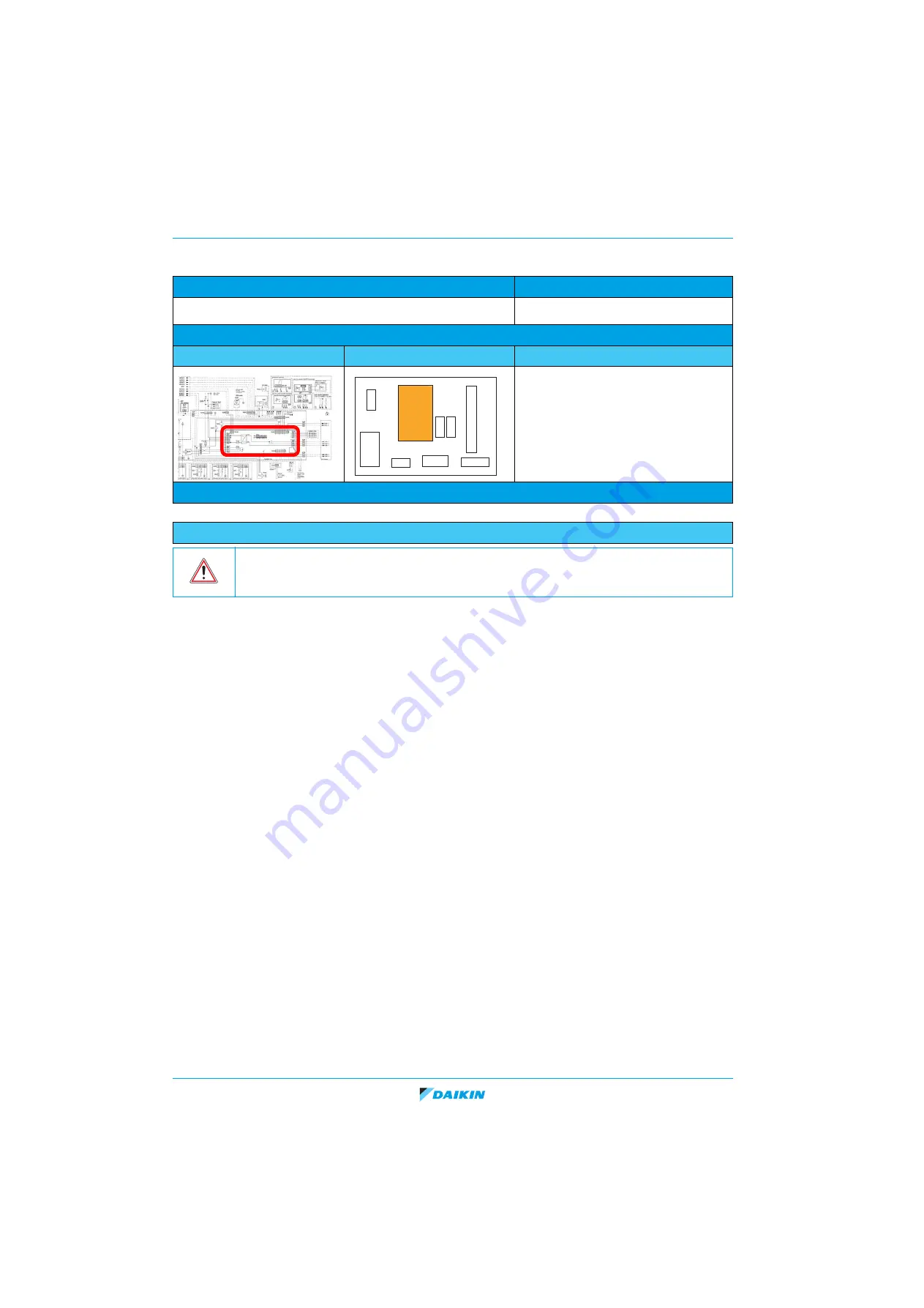
ESIE15-08B
|
Part 2. Troubleshooting
4. Component checklist - Water Circuit
Page 86
19/07/16
Daikin Altherma Monobloc CA
4.11. Extension PCB A4P
1.
Switch off the Daikin Altherma Monobloc CA via the user interface.
2.
Switch off the Daikin Altherma Monobloc CA with the field supplied circuit breaker.
3.
Remove the hydrobox top plate assembly, refer to
"Removing the hydrobox top plate assembly" on page 110
4.
Remove the hydrobox front plate, refer to
"Removing the hydrobox front plate" on page 111
.
5.
Remove the switch box cover.
6.
LED:
If LED 5 is blinking = communication error between PCB A4P and PCB A1P:
-
Check connectors on PCB.
-
Check connection between PCB A4P (X10A) and A6P (X10A)
-
Check connection between PCB A2P (X1A) and A1P (X10A)
-
Check power supply to PCB A1P.
-
If all above checks are OK, replace PCB A4P.
If LED 2 is not blinking:
- Replace
PCB
A4P.
Technical specification
Description
-
The extension PCB A4P is used to control the unit
from the control box.
Location
Wiring diagram
Switch box - Control Box
Unit
Check procedure
Electrical check
W
ARNING
: R
ISK
OF
F
IRE
•
When reconnecting a connector to the PCB, do not apply force or damage the connector or the connector pins on
the PCB.
X1M
X8M
X2M
K2A
K3M
K1A
A4P
F2B
X4M
Not applicable