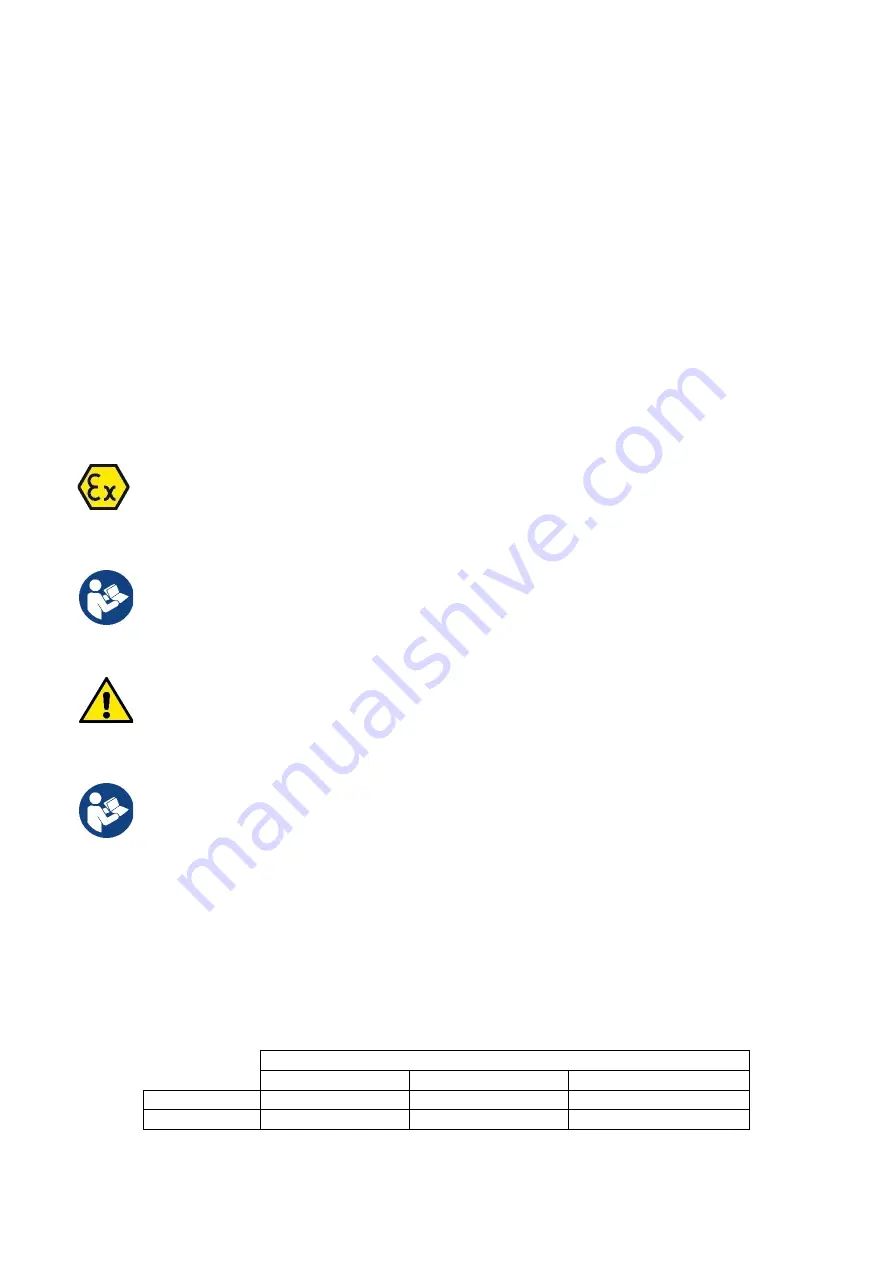
ENGLISH
16
3. Denomination and reference number of the spare parts.
4. Required number of parts.
8.1
Routine maintenance
Pumps running normal operation should be inspected every 3000 operating hours or at least once a year. If the pumped liquid is very
muddy or sandy, inspect the pump at shorter intervals.
Check the following points:
•
Power consumption
See pump nameplate.
•
Oil level and oil condition
When the pump is new or after replacement of the shaft seal, check the oil level and water content after one week of operation. If there is
more than 20 % extra liquid (water) in the oil chamber, the shaft seal is defective. The oil should be changed after 3000 operating hours
or once a year.
•
Cable entry
Make sure that the cable entry is watertight (visual inspection) and that the cable is not sharply bent and/or pinched.
•
Pump parts
Check impeller, pump housing, etc. for possible wear. Replace defective parts.
•
Ball bearings
Check the shaft for noisy or heavy operation (turn the shaft by hand). Replace defective ball bearings.
A general overhaul of the pump is usually required in case of defective ball bearings or poor motor function. This work must be done by
an assistance workshop authorised by DAB Pumps.
The ball bearings used are sealed and lubricated, using a special lubricant for high temperatures (-40°C + 150°C).
Defective bearings may reduce the Ex safety.
The bearings must be replaced every 10.000 hours.
•
O-rings and similar parts
During service/replacement, it must be ensured that the grooves for the O-rings as well as the seal faces have been cleaned before the
new parts are fitted.
Used rubber parts must not be reused.
•
Oil change (Fig.8)
After 3000 operating hours or once a year, change the oil in the oil chamber as described below.
If the shaft seal has been replaced, the oil must be changed.
When loosening the screws of the oil chamber, note that pressure may have built up in the chamber. Do not remove
the screws until the pressure has been fully relieved.
•
Draining of oil
1.
Place the pump on a plane surface with one oil screw pointing downwards.
2.
Place a suitable container (approx. 1 litre), for instance made of transparent plastic material, under the oil screw.
Used oil must be disposed of in accordance with local regulations.
3.
Remove the lower oil screw.
4.
Remove the upper oil screw. If the pump has been in operation for a long period of time, if the oil is drained off shortly after the
pump has been stopped, and if the oil is greyish white like milk, it contains water. If the oil contains more than 20 % water, it is an
indication that the shaft seal is defective and must be replaced. If the shaft seal is not replaced, the motor will be damaged. If the
quantity of oil is smaller than the quantity stated, the shaft seal is defective.
5.
Clean the faces for the gaskets for oil screws.
•
Filling with oil
1.
Rotate the pump so that one of the two oil holes in a vertical position facing upwards.
2.
Pour the oil into the chamber. The suitable amount of oil is indicated by the second oil venting hole (positioned beside the vertical
filling hole). Once the oil has reached and escapes from the hole at the side, the oil quantity is correct.
3.
Fit the oil screws with new gaskets.
The table shows the quantity of oil in the oil chamber of FX RANGE pumps. Oil type: ESSO MARCOL 152.
Motor type
2poles >= 1.5kw
2poles
<= 1.1kw
4poles
NoAtex
0.68 [l]
0.58 [l]
0.65 [l]
Atex
0.75 [l]
0.65 [l]
0.72 [l]
Содержание DRENAG FX
Страница 66: ...60 5 2 3a 4 4a 6 EN 60079 14 4mm2 10 10 10 m DAB pumps 6 1 15 15 6 2 FX RANGE k1 k2 6 1 150 C...
Страница 67: ...61 7 7 1 8 1 7 2 5 8 7 2 1 2 7 8 Dab Pumps...
Страница 68: ...62 DAB pumps DAB pumps DAB Pumps DNA 1 2 3 4 8 1 3000 20 3000 DAB Pumps 40 C 150 C 10 000 Ex 8 M 3000 1...
Страница 71: ...65 5 5 6 6 DAB 7 7 DAB 1 1 7 2 2 2 DAB 3 3 4 4 5 5 6 6 DAB...
Страница 85: ...79 10 FX RANGE MNA TNA 6 FX RANGE MNA e TNA 2 2 1 10 DAB pumps 5 2 3a 4 4a 6 EN 60079 14 4 2 10 10 10 DAB pumps...
Страница 86: ...80 6 1 15a 15b 6 2 FX RANGE k1 k2 6 1 150 C 7 7 1 8 1 7 2 5 8 7 2...
Страница 87: ...81 1 2 7 8 Dab Pumps DAB pumps DAB pumps DAB Pumps DNA 1 2 3 n 4 8 1 3000 20 3000 DAB Pumps 40 C 150 C...
Страница 89: ...83 8 3 9 1 1 2 2 3 a b a b 4 4 5 5 6 6 7 7 DAB 8 8 DAB 9 9 DAB 1 1 2 2 3 3 4 4 5 5 DAB 6 6 7 2 7 7...
Страница 90: ...84 8 8 9 9 DAB 10 10 DAB 1 1 2 2 3 3 7 2 4 4 DAB 5 5 6 6 DAB 7 7 DAB 1 1 7 2 2 2 DAB 3 3 4 4 5 5 6 6 DAB...
Страница 194: ...188 2 2 1 10 cm DAB pumps 5 2 3a 4 4a 6 EN 60079 14 4 2 10 10 10 DAB pumps 6 1 15a 15b 6 2 FX RANGE k1 k2 6 1 150 C...
Страница 195: ...189 7 7 1 8 1 7 2 5 8 7 2 1 2 7 8 Dab Pumps...
Страница 196: ...190 DAB pumps DAB pumps DAB Pumps DNA 1 2 3 4 8 1 3000 20 3000 DAB Pumps 40 C 150 C 10 000 O 8 3000 1 2 1 3...
Страница 199: ...193 2 2 DAB 3 3 4 4 5 5 6 6 DAB...
Страница 221: ...215 2 2 FX RANGE FX RANGE pH 6 5 12 pH 0 50 60 40 40 0 C 40 C m s 1 0 0 7 m s 20 3 1 3 2 3 30 60...
Страница 224: ...218 5 2 3a 4 4a 6 EN 60079 14 4mm2 10 10 10...
Страница 225: ...219 6 1 15a 15b 2 6 FX RANGE 150 C Restart Restart 7 1 7 8 1 S1...
Страница 226: ...220 S2 Restart 8 2 7 1 2 7 8...
Страница 227: ...221 DNA 1 2 3 4 1 8 3000 20 3000 150 C 40 C 8 3000 1...
Страница 229: ...223 3 8 www Dabpumps com 9 1 1 2 2 3 4 4 5 5 6 7 7 8 8 9 9 1 1 2 2 3 3...
Страница 230: ...224 4 4 5 5 6 6 7 2 7 7 8 8 9 9 10 10 1 1 2 2 3 3 7 2 4 4 5 5 6 6 7 7 1 1 7 2 2 2 3 3 4 4 5 5 6 6...
Страница 236: ...230 EN 60079 14 4mm2 10 10 10 DAB pumps 6 1 15a 15b 6 2 FX RANGE k1 k2 6 1 150 7...
Страница 237: ...231 7 1 8 1 7 2 5 8 7 2 1 2 7 8 Dab Pumps DAB pumps DAB pumps...
Страница 238: ...232 DAB Pumps DNA 1 2 3 4 8 1 3000 20 3000 DAB Pumps 40 150 Ex 10 000 8 3000 1 2 1 3 4 20...
Страница 241: ...DRAWINGS 235 Fig 3 Fig 3a Fig 4 Fig 4a...
Страница 242: ...DRAWINGS 236 Fig 5 Fig 6 Fig 7 Fig 8 Fig 9 Fig 10...
Страница 243: ...DRAWINGS 237 Fig 11 Fig 12...
Страница 244: ...DRAWINGS 238 Fig 13 Fig 14...
Страница 245: ...DRAWINGS 239 Fig 15a Wiring Diagram...
Страница 246: ...DRAWINGS 240 CB Booster for Grinder FX Fig 15b Wiring Diagram...