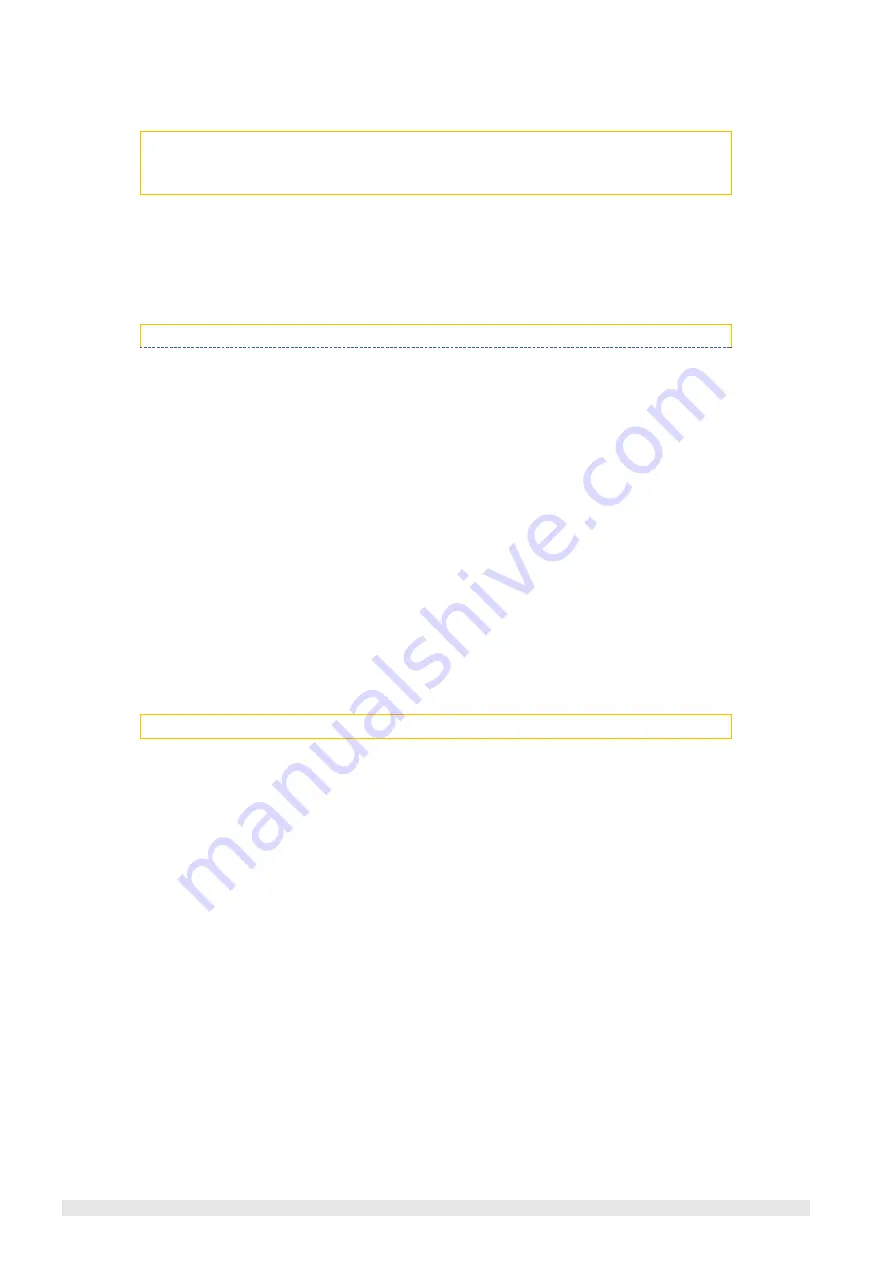
5.
Adequate ventilation is required in the disinfection area to evacuate the chemical vapors from glutaraldehyde (if used). Use lidded containers
for the disinfectant solution when appropriate. The inhalation of fumes from disinfectant solutions or skin contact with liquid disinfectants
can be hazardous to personnel.
Warning:
Particular precautions should be taken when testing patients with high risk communicable diseases (i.e.
Tuberculosis, Multidrug Resistant Staphylococcus infections, etc.). When such conditions are present the clinical need
for performing the test should justify the risks.
When performing the disinfection:
•
Do not use alcohol or other liquids containing Gluteraldehyde on the exterior surface of the equipment.
•
Do not use abrasive powders or glass cleaners containing alcohol or ammonia on the plexiglas component (mixing chamber or canopy) of
the equipment.
•
Do not steam autoclave any component other then rubber reusable masks (plastic adapter and clips should be removed).
Warning:
Do not immerse any parts in liquid unless indicated (see following sections)
Introduction
Decontamination is a multi-step process that includes preparation at point of use, thorough cleaning and rinsing and a microbicidal process.
Thorough cleaning and rinsing are the first and most important steps in the reprocessing of any reusable medical device. Without thorough
cleaning and rinsing it might not be possible to achieve high level disinfection or sterilization of the device. The purpose of cleaning and rinsing is to
remove all adherent visible soil, to reduce the number of particulates and microorganisms, and to reduce the amount of pyrogenic and antigenic
material. Any organic material, lubricants, or residual cleaning agents remaining on a device can inactivate liquid chemical disinfectants/sterilants
as well as protect microorganisms from destruction.
The second step in decontamination is the microbicidal process which is defined as a process to provide a particular level of microbial lethality (kill).
COSMED components are classified as "semi-critical" items which are devices that come into contact with intact mucous membranes. Semi-critical
devices at a minimum require a high-level disinfection procedure. Sterilization is not absolutely essential.
COSMED components require complete or partial disassembly for cleaning and disinfection. It is the responsibility of the user (health care
personnel) for ensuring that: the cleaning methods recommended can be duplicated in their environment, that appropriate tools, and replacement
parts are available and that instructions are followed correctly.
Cleaning
Note:
Please refer to additional, specific cleaning instructions for the turbine assembly below.
Cleaning Agents/supplies
Mild detergents with a neutral pH (7) are recommended for cleaning. Use warm water (22°-43°c) with the mild detergent. To be effective, cleaning
agents must assist in the removal of residual organic soil without damaging the device. cleaning agents should be used in the correct
dilution/concentration and at the correct temperature in accordance with the cleaning agents manufacturer's directions.
Cleaning supplies are very basic, usually consisting of a surgical scrub brush, chenille pipe cleaners, cotton or foam tipped applicators, soft brushes,
and soft cloths. Cleaning supplies should be cleaned and disinfected or sterilized daily.
Water Quality: tap water is acceptable for use in cleaning COSMED components.
COSMED components should be soaked and rinsed in tap water at 22°-43°C to prevent the coagulation of solid substances onto the device and thus
facilitate the removal of debris.
Enzymatic detergents with a neutral pH (7) are recommended when processing difficult-to-clean items with dried-on matter. Soaking mask and
valve components in an enzymatic detergent solution can effectively remove visible debris except for lubricants thus providing an acceptable
alternative to manual cleaning. Rinsing is necessary to remove all traces of detergent and extraneous debris.
Standard cleaning procedure
These steps are common to all the cleaning procedures
Step 1 Preparation at Point of Use.
The cleaning of reusable items begins soon after use. At the point of use, personnel wearing gloves and
other protective attire separate disposable items or components from reusable items and discard them in appropriate receptacles. Soil is wiped
from device surfaces with a moist sponge or towel. The soiled/contaminated items are then contained in a manner that will reduce the risk of
personal exposure to pathogens. Items are usually placed in a basket, tray or rigid container for transportation to the processing area, usually
transported in or on a cart, as hand carrying of soiled items is discouraged.
26 - System maintenance - Cleaning and disinfecting
Содержание microQuark
Страница 2: ......
Страница 4: ...2...
Страница 7: ...Getting started...
Страница 20: ......
Страница 21: ...Installation...
Страница 25: ...System maintenance...
Страница 32: ......
Страница 33: ...Appendix...
Страница 45: ......