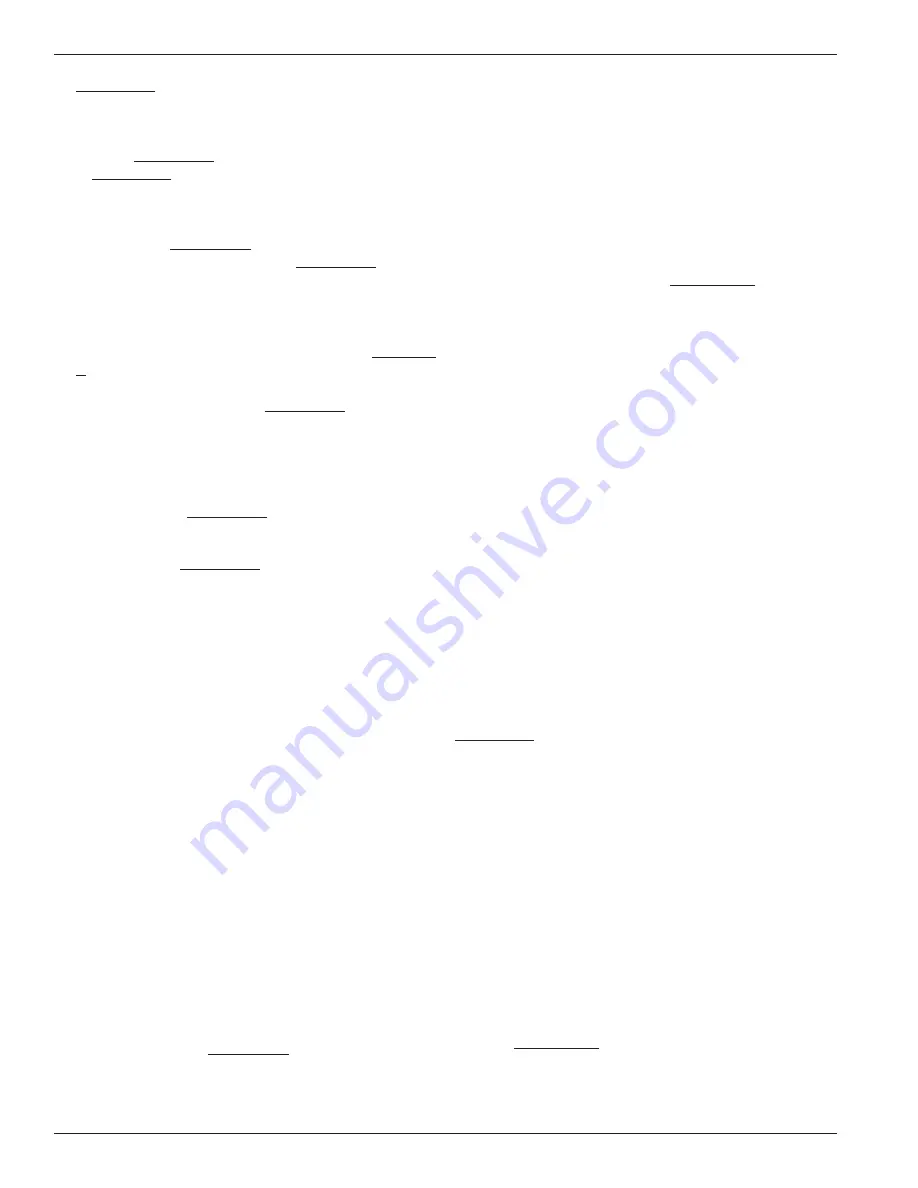
12. Torque the piston cap screws to the value listed in
13.
Install the head (or head and adjustable cap—
applies to adjustable head configuration only) as
show in Appendix D. Torque bolts to the value listed
in Appendix B.
14.
Now remove an outboard valve and measure
dimension “X” at the outboard end of the piston as
shown in the Appendix B. If this measurement does
not fall within the tolerances in Appendix B, remove
the head (or head and adjustable cap—applies to
adjustable head configuration only) and piston cap
and adjust the shims as necessary. Re-install the
piston cap and tighten the piston cap screws in an
alternating sequence to the values listed in Appendix
B. Re-install the head (or head and adjustable cap—
applies to adjustable head configuration only) and
torque to the value listed in Appendix B. Re-measure
the “X” dimension again.
15. After the “X” dimension is within tolerance, remove
the adjustable cap and install the adjustable cup
followed by the adjustable cap and adjustable screw
nut as shown in Appendix D.
16. Torque the bolts in an alternating sequence to the
values listed in Appendix B.
17. Replace the previously removed valves. Best results
will be obtained if new valve gaskets are used.
18. Follow standard startup procedures.
5 .5 Cylinder Replacement
Cylinders very seldom require replacement if the
compressor is properly maintained. The primary cause
of damage to cylinders is corrosion and the entry of solid
debris or liquid into the compression chamber. Improper
storage can also result in corrosion damage to cylinder
(for proper storage instructions see chapter 5). Damage
can also occur if the piston rings are allowed to wear so
much that the ring expander can reach the cylinder wall.
Many compressor repair operations require removal of
the cylinder. While the compressor is disassembled,
special care should be taken to avoid damage or
corrosion to the cylinder. If the compressor is to be left
open for more than a few hours, bare metal surfaces
should be coated with rust preventative.
If the cylinder does become damaged or corroded, use
a hone to smooth the cylinder bore and then polish it
to the value shown in Appendix B. If more than .005 of
an inch must be removed to smooth the bore, replace
the cylinder. Cylinder liners and oversized rings are not
available. OVERBORING THE CYLINDER WILL RESULT
IN GREATLY REDUCED RING LIFE.
1) Keep foreign material out of crosshead bore on
crankcase. Wipe inside of bore with clean rag and
coat bore with oil.
2) Inspect piston rod for cleanliness and coat with oil
before assembly.
3) Before installing adapter and packing cartridge
on piston rod, install packing installation cone
(Corken #3905) over piston rod threads. This
will aid and protect packing during installation.
Failure to use this packing cone could result in
packing damage. Refer to Appendix D for correct
installation of packing.
4) Rotate flywheel/crankshaft by hand several revolutions
to ensure proper fit of all assembled parts.
5) Orient cylinder inlet and outlet to piping installation
to ensure proper valve alignment with system.
Valves must be properly oriented with suction and
discharge piping.
6) For piston installation instructions, see section 5.4.
7) After installing the piston, again, rotate flywheel/
crankshaft by hand several revolutions to ensure
proper fit of all assembled parts.
8) Check crankcase for proper oil level.
9) See startup procedure in section 3.7. During startup,
listen to the compressor for any unusual noises. If
any problems arise during assembly, please contact
the factory.
When reassembling the compressor, make sure the
bolts are retightened using the torque values listed in
Appendix B.
5 .6 Packing Replacement
Instructions
Caution: Before installing the new piston rod packing,
bleed all pressure from the compressor and piping and
purge if necessary. After the new piston rod packing has
been installed, the unit should be pressure tested and
checked for leaks at all joints and gasket surfaces. When
the compressor is being used with toxic, dangerous,
flammable or explosive gases, this pressure and leak
testing should be done with air or a dry, inert gas such
as nitrogen.
For specific construction details and actual part numbers,
consult Appendix D in the back of this Installation,
Operation & Maintenance (IOM) manual. Use instructions
below that apply to the MODEL and SERIAL NUMBER of
the compressor.
20