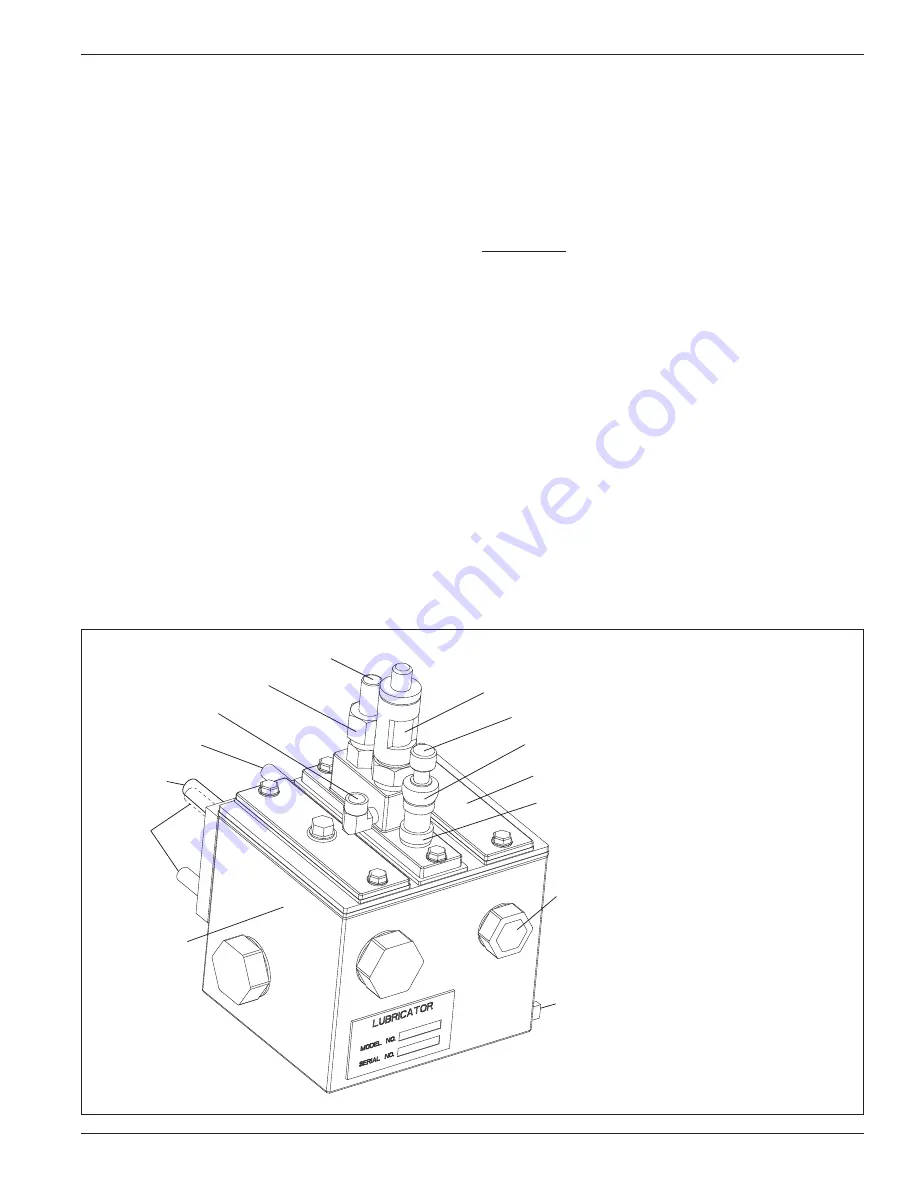
3 .4 Compressor Speed and
Rotation Direction
The lubrication system of the Corken horizontal
compressor is designed to operate at a minimum of 400
RPM. If lower speeds are necessary, consult the factory.
The maximum speed is 1200 RPM. The crankshaft may
be rotated in either direction.
3 .5 Compressor Cooling
AIR COOLED: Double acting units generate a lot of
heat around the valve area. It is very important that
the compressor be located where good air flow and
ventilation can be provided. In extreme cases external
cooling fans can be used to provide additional air flow
across the cylinders.
WATER COOLED: If the compressor has water cooled
cylinders (optional), be sure that the cooling system
has been inspected for leaks and proper circulation.
Purge air from the cooling jackets to eliminate air
pockets in the cooling system. If chilled water systems
are used be sure that water shut-off valves are
installed to stop water flow when compressor stops.
Monitor system for any signs of internal sweating. If
internal moisture is detected, water temperatures and
flow rates should be checked. Normal flow rate for
cylinders is approximately 1–2 gpm.
3 .6 Force Feed Cylinder
Lubrication (Lubed models only)
An external lubricator is bolted directly to the crankcase
and is driven by a chain inside the crankcase at 80%
of crankshaft speed. To ensure each cylinder receives
the same volume of lubrication, an oil divider valve
assembly is also mounted to the opposite end of
the crankcase (see lubricator assembly details in
Appendix D). Since lubricators supplied with Corken
compressors are made by a number of different
manufacturers, refer to the manufacturer’s instructions
provided with the lubricator for specific details on
priming, adjusting, and maintaining the lubricator.
Basic operating instructions and flow rate adjustments
are also listed on the side of the lubricator reservoir.
At the initial setup of the compressor, the lubricator
flow should be set to maximum capacity. After the first
hour, reduce the flow to normal operating levels. Normal
operating levels range from three to six drops per minute
depending upon the cylinder size.
NOTE: The lubricator supplied with a CORKEN
compressor must be supplied with oil from an external
supply tank and NOT from the compressor crankcase
or lubricator reservoir.
Oil types: Refer to section 2.6 (crankcase lubrication).
Reservoir
sight glass
Priming button
Oil inlet (1/8
″
)
Drive shaft
Drip tube sight glass
Lock nut
Mounting
studs
Oil outlet (1/8
″
)
Union nut
Mounting stud
Reservoir
Flushing unit
Oil fill opening
Drain
plug
Typical lubricator shown above.
NOTE:
1) Since Corken uses more than
one vendor when purchasing
lubricators, the lubricator shown
and respective operational
instructions may vary from the
one used on the compressor.
2) Operational instructions can
be found on the side of the
lubricator reservoir.
3) Oil used in the reservoir is for
lubricating the internal parts of
the lubricator only and not the
compressor.
4) Depending on the cylinder
size, the oil flow rate for the
drip tube site glass is three to
six drops per minute during
normal operations.
15