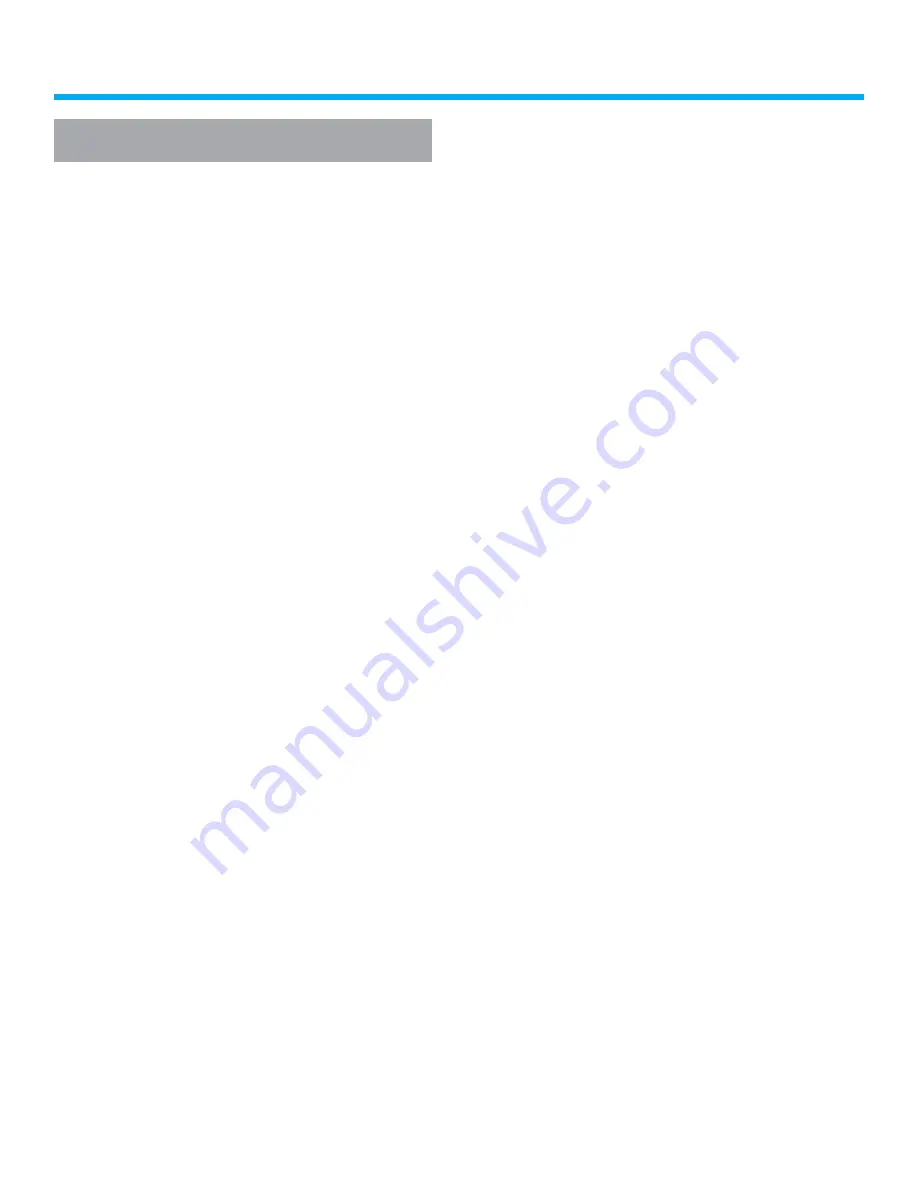
MT Series DryLine
®
Dehydrator User Manual
18
The dehydrator requires maintenance
semiannually and after each 6000 hours of
operation to ensure continued reliable operation.
Danger:
Service personnel should observe all
safety regulations. Do not perform
maintenance on equipment without
first turning off the main power supply.
Under certain conditions, dangerous
potentials may exist when the main
power supply controls are in the off
position. Only qualified technicians
should attempt to effect maintenance
or repairs on electrical equipment.
Semi-Annual Maintenance.
The semi-
annual maintenance consists of a preventive
maintenance inspection and replacement of
the compressor air filter. These tasks can be
performed easily in the field as described below.
6000 hour Overhaul. A dehydrator overhaul is
required after the compressor has run a total of
6000 hours, as indicated on the compressor run
time meter. The dehydrator overhaul includes
a compressor overhaul, water filter, high
temperature tubing and hose clamps.
The dehydrator overhaul kit, see Section
7.0, includes all the necessary parts and
instructions. Or, if you prefer, CommScope
offers a dehydrator overhaul service. Contact
CommScope Technical Service. Telephone
numbers are found in Section 9.
Refer to Sections 7.9, 7.10 and 7.11 for
procedures to replace water filter elements.
In Case of Difficulty. If the dehydrator will not
operate or if there are other problems, refer to
the troubleshooting procedures in
Section 6
.
Semi-Annual Preventive Maintenance
Inspection includes checking for loose
or damaged hoses, fittings and electrical
connections. Check the following items:
Water Filter and Coalescent Filter and
Elements
Verify there is no water build-up in the
filter bowls. If there is water, refer to the
troubleshooting procedures in Section 6 for
corrective action. Replacement of the water
filter and coalescent filter and their associated
elements and bowls is covered in the parts
replacement section of this manual. Refer to
Section 7.
Electrical Connections
Check for loose or corroded electrical
connections. A loose terminal can cause erratic
operation and unnecessary downtime. Check
the screw-on and push-on terminals and tighten
as required.
Ground Wire
Check for proper ground wire connection to
protect operations personnel. A green ground
wire is attached between the power terminal
strip and the dehydrator chassis. The ground
lug screw or stud nut must be tight to provide a
proper ground.
Hour Meter
Check the run time meter to determine the duty
cycle of the dehydrator. If the dehydrator has
been running more than 10% of the time, check
for system leaks. Also check to see if it is time
to schedule the 6000-hour maintenance.
The air filter protects the compressor from
contamination and extends the service life of the
compressor. It is made of open cell material
and should be replaced every six months or
more often if the dehydrator is located in a dusty
environment.
Carefully pull off the filter cover and remove the
filter element. Install the new filter element and
replace the filter cover, being certain that it is
completely seated. To replace the filter housing,
unscrew the housing from the compressor head
and replace with new filter housing.