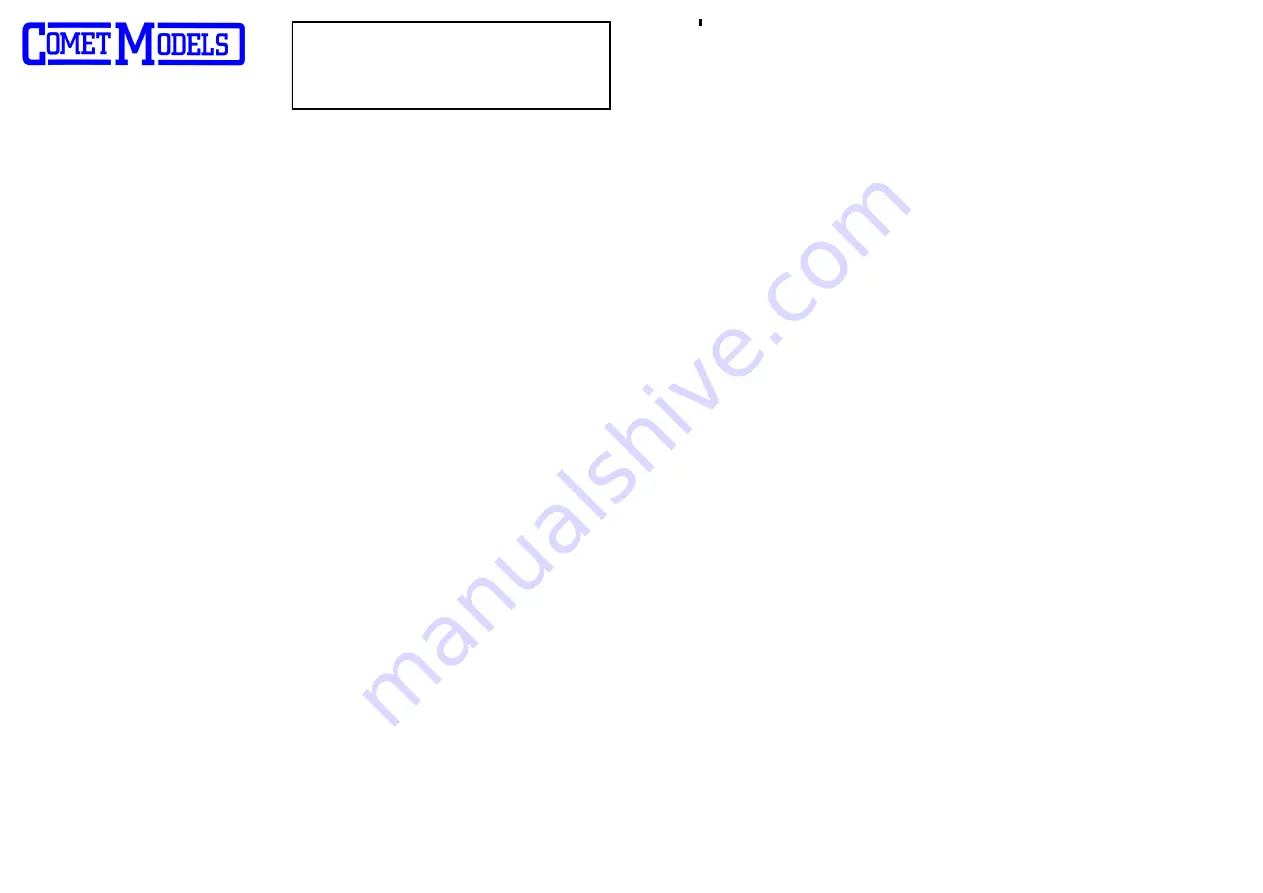
This etch contains sideframes, brake shoes, brake pull rods, balance weights and coupling rods to produce
a basic chassis of the correct scale dimensions and appearance which can be used as a substitute for a kit
or RTR chassis. A separate fret of 00 spacers is included, which can be exchanged for EM (LS10) or P4
(LS60) by returning them to us in a stamped, self-addressed envelope.
As supplied the chassis is suitable for the Mainline, Replica or Bachmann RTR bodies.
We recommend the Mashima MH1620 motor with our gearbox GB1/20 for this model, and can supply the
latter together with Markits driving wheels if required.
Please note that all bends should be made with the half-etched lines to the inside and reinforced with a fillet
of solder.
Assembly Instructions
1.
The frames may be assembled rigid, or with sprung axles using our hornblocks and springs code
LS55. If you wish to spring the chassis cut through the spring hangers using a piercing saw and
remove them together with the centre portion of etch within the hornway. The sides of the
hornways are etched at 5.85mm approx. so as to ensure that any slight variations in the width of
the machined grooves in the hornblocks do not result in any one of them having a loose fit within
the hornway. Each hornway must be carefully dressed with a file to achieve a good sliding fit to
each hornblock, which should then be marked up or placed into a labelled bag to ensure it is
assembled only into the hornway to which it has been precisely matched. Take time and care over
this stage, removing material slowly and from each face equally. The hornblock must drop in freely
under gravity but must not show any fore and aft play which might cause the coupling rods to bind.
This might sound daunting, but the patient builder will be rewarded with a chassis having superior
ride, track holding and traction compared to an unsprung chassis.
2.
For rigid axle assembly, carefully open out the axle bearing holes in the frames until the bearings
are a close fit, ensuring the bearing flanges fit snugly against the frames. This is best done using a
five sided broach. If you are using our chassis jigs (see below), DO NOT solder the bearings in
place at this stage. Open out the holes for the brake cross-shafts to 0.75mm.
3.
Select the appropriate frame spacers- the size and position of them will depend on the siting of the
body fixings and your preferred motor/gearbox and pick-up arrangements. Our own preferences
are, where possible, for a tongue and slot fixing at the front buffer beam and the original screw
fixing under the cab. A suitable layout of spacers is shown (sketch 1) to suit this and our gearbox
GB1 and Mashima MH1624 motor.
4.
If you are springing the chassis drill out the holes at each side of the hornways and those in the
separate spring etches to 0.5mm as shown in sketch 2. The frame spacers fold to right angles on
the half-etched line. Solder your chosen ones to one of the frames, then assemble by clamping the
other side frame to the first using the wheelsets to check alignment before soldering the second
side frame. This crucial stage of the assembly can be achieved more easily and with greater
accuracy by using our frame assembly jigs (code LS16 for 00, LS17 for EM and LS61 for P4). Full
instructions are provided with them. If you are springing the chassis using our hornblocks please
note that you will need a set of four turnings (code LS59) which are intended to locate in the
hornway during this stage of assembly.
5.
For a sprung chassis insert the spring and hornblock, ensuring that they are placed into their
correct hornways only. Note that the grooves in the hornblock are not on the centre line. This
allows you to choose a greater or lesser amount of sideplay on each axle. Use 0.45mm wire to
locate the spring detail and solder in place using a minimum of flux. This captures the hornblock
and the protruding centre shackle should ensure that the bottom of the hornblock is slightly above the
bottom edge of the chassis giving approximately 1.0mm of movement only. Do not be tempted to file
too much material from the top of the centre shackle. Greater travel should not be necessary and
there is then a risk that the spring could become dislodged if there is too much downward travel.
6.
Solder lengths of 0.7mm wire through the brake hanger holes. Solder the brake overlays to the brake
rear etches (sketch 3) then thread them on and solder in place. Alignment is made easier if
something of suitable thickness is used to space out the brake shoe from the frame, with a wheelset
fitted to ensure correct spacing relative to the wheel treads.
7.
Lengths of 0.7mm wire are next threaded through the bottom brake hanger holes and soldered in
place. Temporarily fit the brake pull rods outside the brake hangers. They can be held in place by
using short lengths of small diameter electrical flex sheathing pushed on over the 0.7mm wire. Insert
a length of 0.7mm wire through the rear holes in the pull rods, at the same time capturing the two
brake pivot brackets. Turn the brackets until they are vertical and solder them to the inside face of the
frames (sketch 7), then remove the brake pull rods.
8.
The coupling rods can be articulated if desired by cutting the full length backing rod as shown before
soldering on the overlays. Whether you articulate the rods or not, this operation is simplified if the
crankpin holes are first drilled, (1.2mm for Markits crankpins) and the backing rod tinned along its
length. Both the backing rod and the overlay can now be threaded onto the drill which will keep one
end in alignment whilst the other is squared up and the rods soldered together. Note that on this loco
the half-etched surface of the coupling rods should face inwards towards the frames.
9.
The chassis can now be washed to remove any flux residues, but before painting we suggest that
you fit the wheels and check the fit of the body. You may find some slight filing is required to obtain a
perfect fit. If using Markits wheels you will need to use a paper washer between the coupling rod and
the crankpin washer to prevent the rods being soldered to the crankpins
10.
With the wheelsets and drivetrain fitted, the brake pull rods can now be fitted outside the wheels.
Make sure that you have the pull rods the right way round, and that sufficient clearance is left to allow
for any axle sideplay.
Our preference is for wiper pick-ups made from 26swg phosphor bronze wire (sketch 8) as offered in our
product code LS23. The wire is soldered to PCB strip which is bolted to a frame spacer. We recommend that,
if possible, you arrange the pick-up to be “bolt on” since this allows for easy removal and adjustment of the
wire wipers.
LCP22
Chassis pack
for Collett GWR
5700/8750
0-6-0PT
Components required to construct a complete
chassis:
6 Markits 4'7" short throw driving wheels (WH201)
3 axles
6 crankpins and washers (RM2)
Mashima MH1624 motor and gearbox GB1/20
Comet Models is part of Wizard Models Limited, PO Box 70, Barton upon Humber DN18 5XY
Tel 01652 635885, web www.wizardmodels.ltd, e-mail [email protected]
© Wizard Models Limited 2020