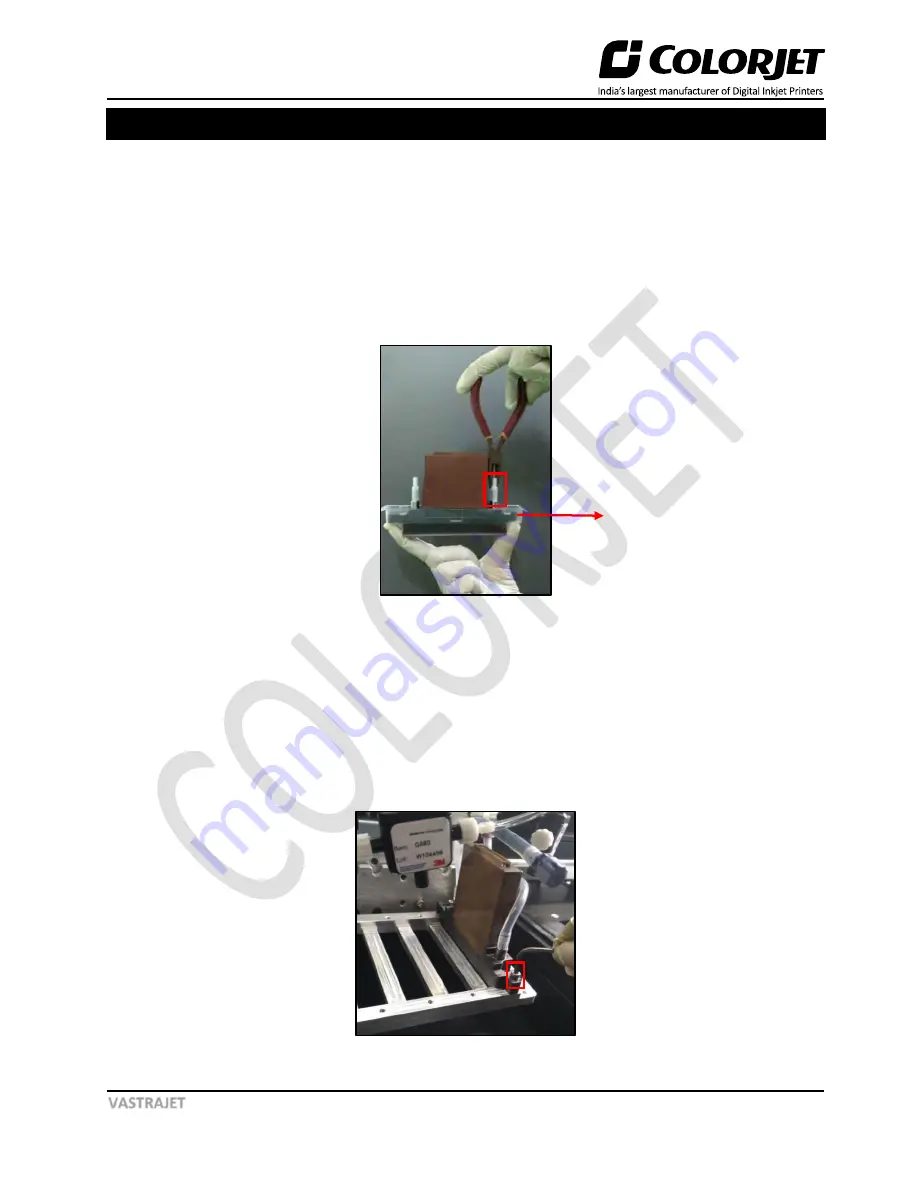
Page | 36
VASTRAJET
8. Head Installation
Use this section, if Print Head is not installed in the printer.
The installation of Print Heads is to be done only by a service engineer. If the Print Head is not installed
correctly, it can affect the printing quality.
Note: Don’t apply much pressure on
Print Head
while handling it.
Follow these steps to install the Print Head:
Step 1
: Remove the
Ink Inlet caps
gently to avoid damage to the Print Head, as shown below:
Fig 40: Removing the Ink Inlet Caps
Step 2:
Fix the
Air Releasing pipe
on one end of the
Ink Inlet Tube
(Refer to Fig 41).
Step 3:
Remove the
Nozzle Cap
from the Print Head (Refer to Fig 41).
Note:
Don’t put the Print Head (nozzle facing) on the rough or dusty surface.
Step 4:
Mount the
Print Head
in the slot on the
Head Plate
.
Step 5:
Fix all the screws (
3x16 mm screws
) gently on the Print Head, as shown below:
Fig 41: Fixing the Head Screw
Nozzle Cap