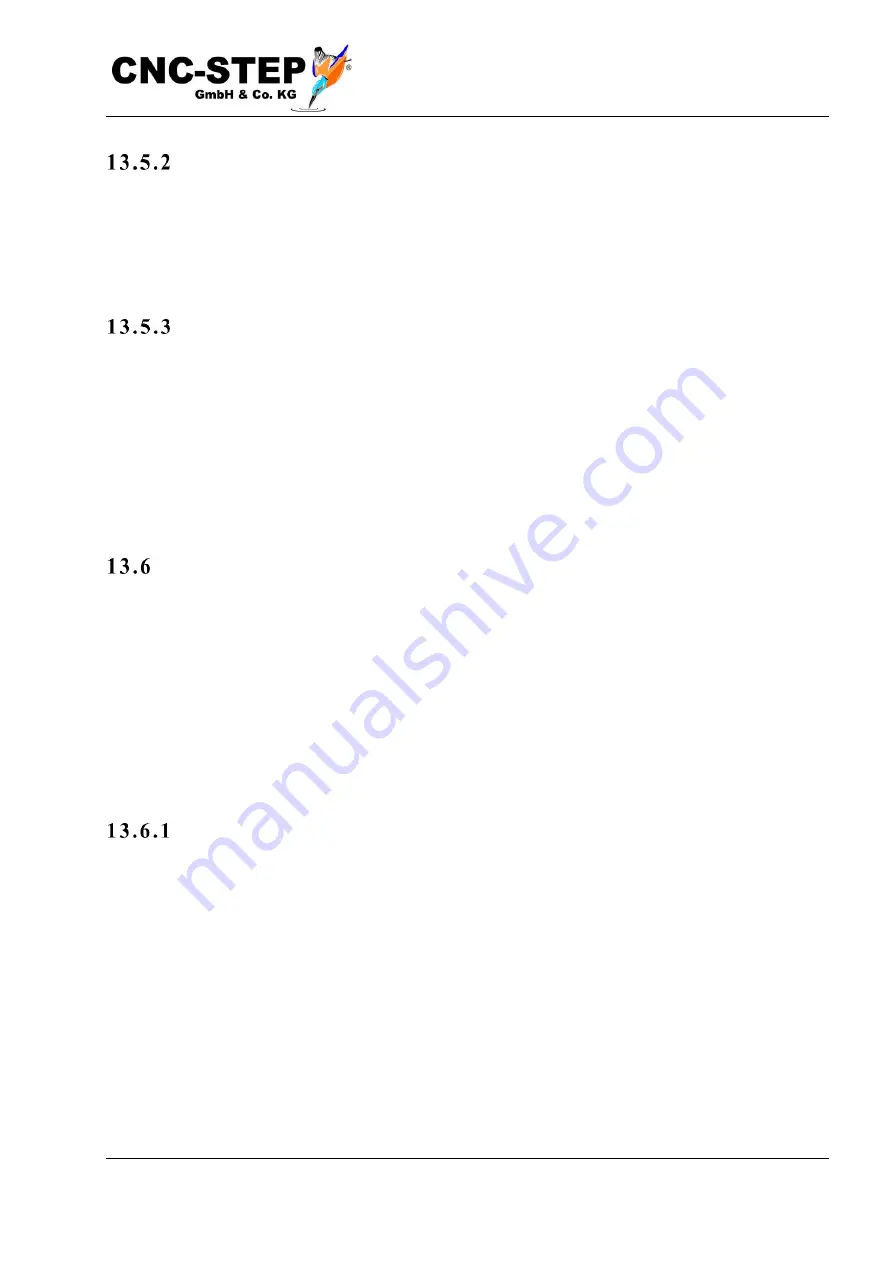
KinetiC-NC
User Manual
CNC-STEP GmbH & Co. KG ▪ Siemensstrasse 13-15 ▪ 47608 Geldern ▪ Germany
Page 99
Support: +49 (0)2831/91021-50
10.11.2018
Ma nual tool chang e (dire ct)
Even if one does not have the "luxury" of an automatic tool changer, one can work off programs
with several different tools. In this case, the setting in "Configuration -> Machine -> General" is set
to "Tool change manual". In addition, you should create at least as many tools in the tool list as
occur in the programs used, eg. T1 to T10.
Direc tly used tools
If the tool spindle does not have an exchange system with extra tool holders (usually SK = steep
taper, HSK = hollow shaft taper), but the tool with the shank is inserted directly into the collet
chuck in the motor shaft, this is called direct change. The advantage is that this can be done with
any reasonably priced tool spindle. Disadvantages are that the tool can be in a slightly different
position after each change, and that with different shank diameters each time the collet must be
replaced with. This requires more time, and usually the tool length must be re-measured after each
change.
T o o l l e n g t h s e n s o r
For this reason, when switching directly, it is strongly advised to purchase a tool length sensor. This
is the same as the height probe described above, only fixedly mounted at a certain point on the
machine. There are also combined length and height probe, where the same probe can be used for
both purposes. Such a button usually has a magnetic foot, which is firmly mounted on the machine.
There, the probe is used for tool length measurement. For mobile application to measure the
workpiece surface height, the probe can be removed from the foot and placed on the workpiece. In
contrast, if two separate buttons are used, they can nevertheless be connected to the same input of
the hardware (series connection) because the buttons are never used at the same time.
Without tool length se nsor
If you do not have a length sensor, it is best to use the "no tool change" method and separate the
programs so that each machining step is performed separately with just one tool. Alternatively, the
program can also be left "in one piece", but only one of several tools can be activated each time it is
run. You can do this by switching off the "Select all" toolbox in the Tool path dialog and activating
only a single tool.