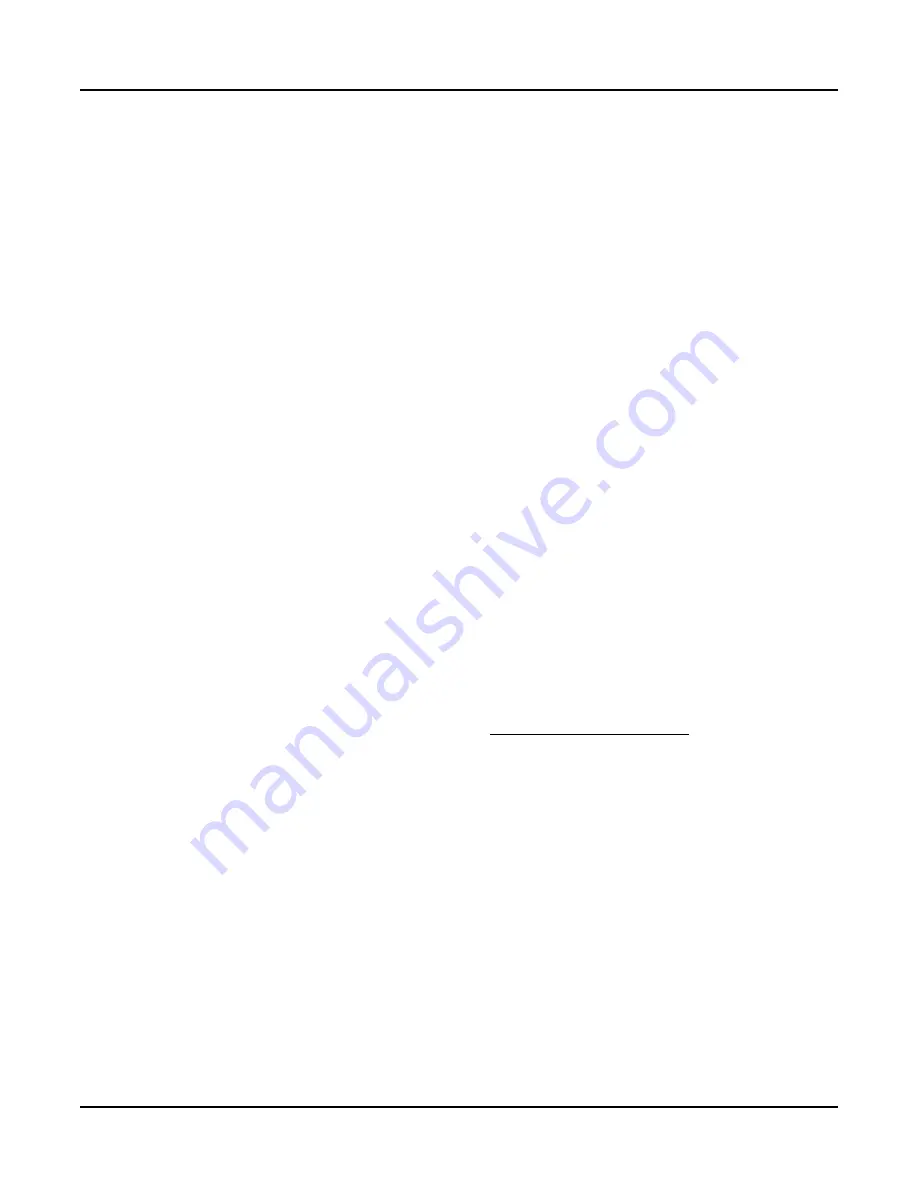
Chapter 8 — Inspection and Maintenance
8-12
Part No. 750-184
disturbed. Failure to follow these instructions could result
in equipment damage.
L. FORCED DRAFT FAN
The position of the fan housing and the clearance between it and the
impeller is extremely important to the output capacity of the fan.
The procedures for installing and adjusting are as follows:
1. Bolt the motor securely to the head.
2. Slide the fan onto the shaft, but do not tighten the setscrews.
3. Turn the spacers on the studs until they contact the headplate.
4. Place external tooth lockwashers next to the spacers and install the fan
housing on the studs. Hold the fan housing in place with nuts and
lockwashers. Finger tighten the nuts.
5. Slide the impeller outward until its vanes contact the fan housing. The
housing must be parallel to the impeller. Adjust the spacers as necessary
to align the housing with the impeller.
6. Slide the impeller toward the motor. Use a feeler gauge to obtain .030-
.050” clearance between the impeller and the housing.
7. Secure the key and then tighten the impeller hub setscrews. Using a
selected vane, rotate the impeller while checking to see that the clearance
between the impeller and the housing remains constant and within the
specified 0.030-0.050" clearance.
8. Install the air duct assembly through the head opening. Tighten the
screws securing the air duct to the fan housing only enough to create a
seal between the neoprene gasket and the housing.
9. After connecting the motor leads, verify that the impeller rotation is
counter-clockwise when viewed from the motor end.
Notice
Note: If the boiler is installed in a dusty location, check the
vanes occasionally for deposits of dust or dirt. These
buildups can cause a decrease in air capacity, or lead to an
unbalanced condition or cause damage to the equipment.
Do not hand operate the valve with less than 75% of the stamped set
pressure exerted on the underside of the disc. When hand operating, be sure
to hold the valve in an open position long enough to purge accumulated
foreign material from the seat area and then allow the valve to snap shut.
Frequent usage of the safety valve will cause the seat and disc to become
wire drawn or steam cut. This will cause the valve to leak and necessitate
down time of the boiler for valve repair or replacement. Repair of a valve
must be done only by the manufacturer or his authorized representative.
Avoid having the operating pressure too near the safety valve set pressure.
A 10% differential is recommended. An even greater differential is desirable
and will assure better seat tightness and valve longevity.
Содержание CB Ohio Special 100 HP
Страница 2: ...ii ...
Страница 8: ...viii ...
Страница 42: ...Chapter 2 Burner Operation and Control 2 22 Part No 750 184 ...
Страница 116: ...Chapter 6 Adjustment Procedures 6 28 Part No 750 184 ...
Страница 126: ...Chapter 8 Inspection and Maintenance 8 6 Part No 750 184 ...
Страница 153: ...Chapter 9 Parts Part No 750 184 9 3 Insulated Front Head Model CB LE ...
Страница 154: ...Chapter 9 Parts 9 4 Part No 750 184 Insulated Front Head Interior Model CB LE ...
Страница 155: ...Chapter 9 Parts Part No 750 184 9 5 Insulated Inner Door Model CB OS ...
Страница 156: ...Chapter 9 Parts 9 6 Part No 750 184 Insulated Rear Head CB LE ...
Страница 157: ...Chapter 9 Parts Part No 750 184 9 7 Insulated Rear Head CB LE ...
Страница 158: ...Chapter 9 Parts 9 8 Part No 750 184 Insulated Rear Head CB OS ...
Страница 159: ...Chapter 9 Parts Part No 750 184 9 9 Dry Oven Model CB LE ...
Страница 161: ...Chapter 9 Parts Part No 750 184 9 11 Motor Impeller Model CB LE ...
Страница 162: ...Chapter 9 Parts 9 12 Part No 750 184 Front Head Linkage ...
Страница 170: ...Chapter 9 Parts 9 20 Part No 750 184 Control Cabinet Hawk ICS ...
Страница 171: ...Chapter 9 Parts Part No 750 184 9 21 Control Panel Standard ...
Страница 172: ...Chapter 9 Parts 9 22 Part No 750 184 Entrance Box ...
Страница 173: ...Chapter 9 Parts Part No 750 184 9 23 Front Head Electrical CB LE ...
Страница 174: ...Chapter 9 Parts 9 24 Part No 750 184 Front Head Electrical CB LE ...
Страница 175: ...Chapter 9 Parts Part No 750 184 9 25 Front Head Electrical CB OS ...
Страница 176: ...Chapter 9 Parts 9 26 Part No 750 184 Front Head Electrical CB OS ...
Страница 179: ...Chapter 9 Parts Part No 750 184 9 29 Heavy Oil Piping 60 Steam CB LE ...
Страница 180: ...Chapter 9 Parts 9 30 Part No 750 184 Heavy Oil Piping 60 Steam CB LE SEE TABLE NEXT PAGE ...
Страница 181: ...Chapter 9 Parts Part No 750 184 9 31 Common Oil Parts Heavy Oil ...
Страница 182: ...Chapter 9 Parts 9 32 Part No 750 184 Side Mounted Air Compressor Piping ...
Страница 183: ...Chapter 9 Parts Part No 750 184 9 33 Air Compressor Piping CB OS ...
Страница 185: ...Chapter 9 Parts Part No 750 184 9 35 Light Oil Piping ...
Страница 186: ...Chapter 9 Parts 9 36 Part No 750 184 Light Oil Air Piping Front Head ...
Страница 187: ...Chapter 9 Parts Part No 750 184 9 37 Light Oil Air Piping Front Head PAGE 9 31 ...
Страница 191: ...Chapter 9 Parts Part No 750 184 9 41 Gas Train 125 150 HP ...
Страница 193: ...Chapter 9 Parts Part No 750 184 9 43 Gas Train 200 HP ...
Страница 195: ...Chapter 9 Parts Part No 750 184 9 45 Steam Pressure Controls ...
Страница 196: ...Chapter 9 Parts 9 46 Part No 750 184 Hot Water Temperature Controls ...
Страница 197: ...Chapter 9 Parts Part No 750 184 9 47 Water Column ...
Страница 198: ...Chapter 9 Parts 9 48 Part No 750 184 Water Column ...
Страница 199: ...Chapter 9 Parts Part No 750 184 9 49 Fireside Gaskets CB LE ...
Страница 200: ...Chapter 9 Parts 9 50 Part No 750 184 Fireside Gaskets CB OS ...