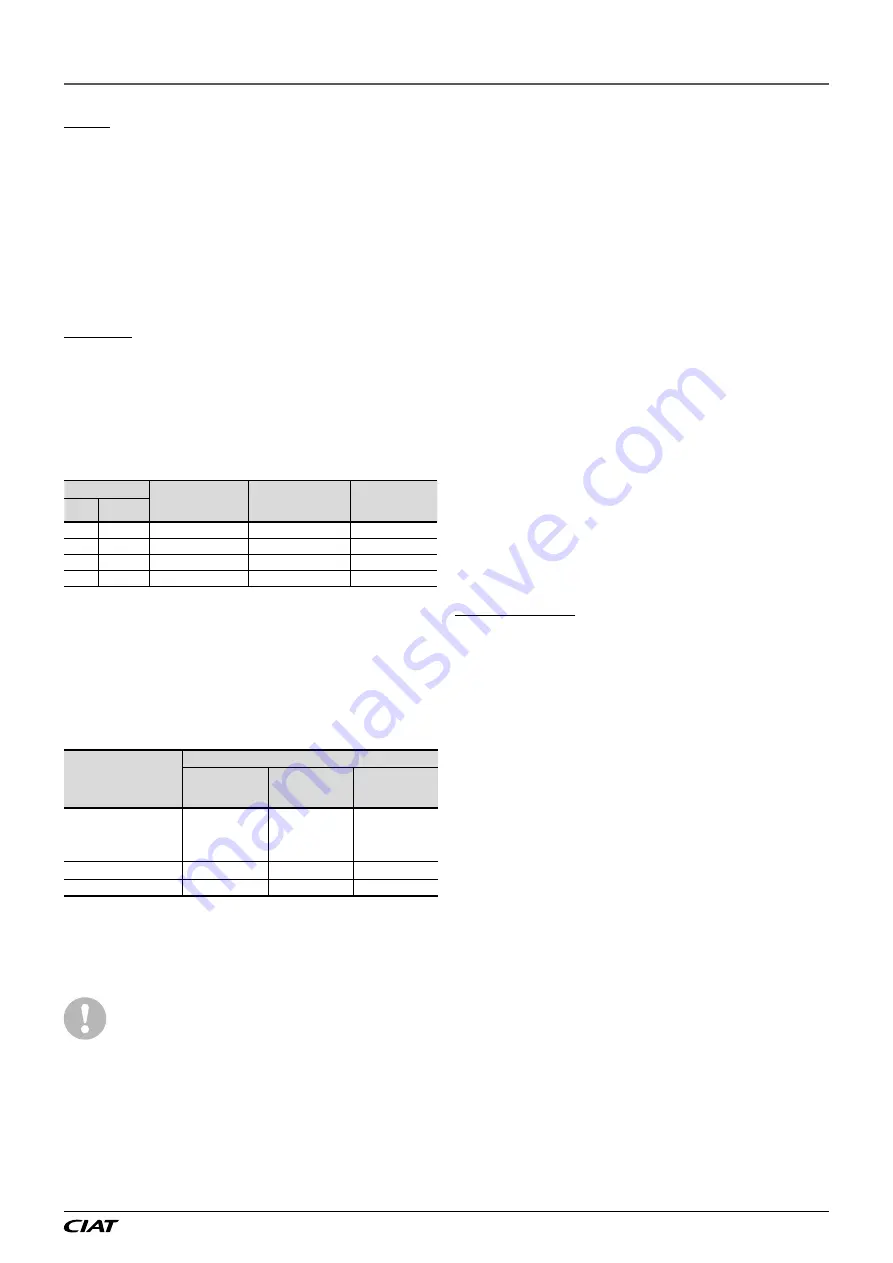
Repair:
Any repair or modification, including replacement of removable
parts:
-
Must comply with local regulations and must be performed by
qualified operators in accordance with qualified processes,
including changing a wiring harness conductor,
-
Must be approved by the original manufacturer. Repairs and
modifications which involve a permanent assembly (welding,
soldering, expansion of tubes, etc.) must be performed by
qualified operators following operating procedures,
-
All modifications and repairs must be listed in the monitoring
and maintenance register,
-
Never attempt to repair or modify a plate heat exchanger.
Recycling:
The pressure equipment can be recycled in whole or in part.
After use they may contain refrigerant vapours and oil residue.
Some parts are painted.
1.4 - Maintenance safety considerations
The manufacturer recommends the following template for the
maintenance log (the table below is only given as a guide and
does not engage the manufacturer's liability).
Intervention
Name of the
commissioning
engineer
Applicable
national regulations
Verification
Organisation
Date Nature
(1)
(1) Maintenance
Any technician carrying out work on the electrical or refrigerating
section must be authorised, with the relevant qualifications and
certifications, including for brazing operations and for operation
of the shut-off valve. He/she must have been specifically trained
on this equipment and system.
The manual valves must only be manipulated when the machine
is off. Do not forget to refit protective caps to prevent leaks.
Technicians working on the units must be equipped as follows:
Personal protection
equipment (PPE)
(1)
Operations
Handling
Maintenance,
service
operations
Welding or
strong brazing
(2)
Protective gloves,
eye protection,
safety shoe,
protective clothing.
X
X
X
Ear protection.
X
X
Filtering respirator.
X
(1) We recommend following the instructions in EN 378-3.
(2) Performed in the presence of A1 refrigerant according to EN 378-1.
Never work on a unit that is still energised.
Never work on any of the electrical components until the general
power supply to the unit has been isolated and locked out.
Even if the unit has been shut down, the power
circuit remains energized, unless the unit or circuit
disconnect switch is open. Refer to the wiring
diagram for further details. Follow the appropriate
safety guidelines. When working in a fan area,
specifically if the grilles have to be removed, isolate
the power supply to the fans to prevent their
operation.
Units equipped with the variable speed fan option, variable speed
pump options and the power factor option are equipped with
capacitor batteries which take 5 minutes to fully discharge once
the power has been switched off.
After disconnecting the power supply to the electrics box, wait 5
minutes before accessing the electrics box or variable drives.
Before any intervention, verify that there is no voltage present
at any accessible conducting parts of the power circuit.
Regularly check that the vibration levels remain acceptable and
close to those at the initial machine start-up.
Before opening a refrigerant circuit, purge and read the pressure
indicators.
If the refrigerant circuit remains open after an intervention (such
as a component replacement, etc.):
-
Seal the openings if the duration is less than a day
-
Beyond this time, charge the circuit with a dry, inert gas
(nitrogen).
The objective is to prevent penetration of atmospheric humidity
and the resulting corrosion of the unprotected internal steel walls.
1.5 - Safety considerations during system
interventions
To prevent any damage or accidents, trained personnel must
service the various parts of this machine and must resolve any
malfunctions or leaks immediately.
Comply with the regulations and recommendations given in the
safety standards for refrigerant systems and machines, such as:
EN 378, ISO 5149, etc.
Risk of explosion:
Never use air or gases containing oxygen during leak tests, to
purge pipework or to pressurise a unit. Pressurised air mixtures
or gases containing oxygen can be the cause of an explosion.
Oxygen reacts violently with oil and grease.
Only use dry nitrogen for leak tests, possibly with an appropriate
tracer gas.
A failure to observe the above recommendations can have
serious or even fatal consequences and damage the
installations.
Never exceed the specified maximum operating pressures. Verify
the maximum permissible high and low test pressures by
checking the instructions in this manual or the pressures given
on the unit nameplate.
The necessary protection equipment must be available, and
appropriate fire extinguishers for the system and the refrigerant
type used must be within easy reach.
Do not attempt to remove refrigerant circuit components or fittings
while the machine is under pressure or while it is running. Make
sure the circuit pressure is zero and that the unit has been
stopped and powered off before removing components or
opening a circuit. When the refrigerant circuit is opened to repair,
see the recommendations in chapter “Maintenance safety
considerations”.
No part of the unit must be used as a walkway, rack or support.
Periodically check and repair or, if necessary, replace any
component or piping that shows signs of damage.
The lines can break under the weight and release refrigerant,
causing personal injury.
1 - INTRODUCTION
EN-7
AQUACIAT
POWER
ILD