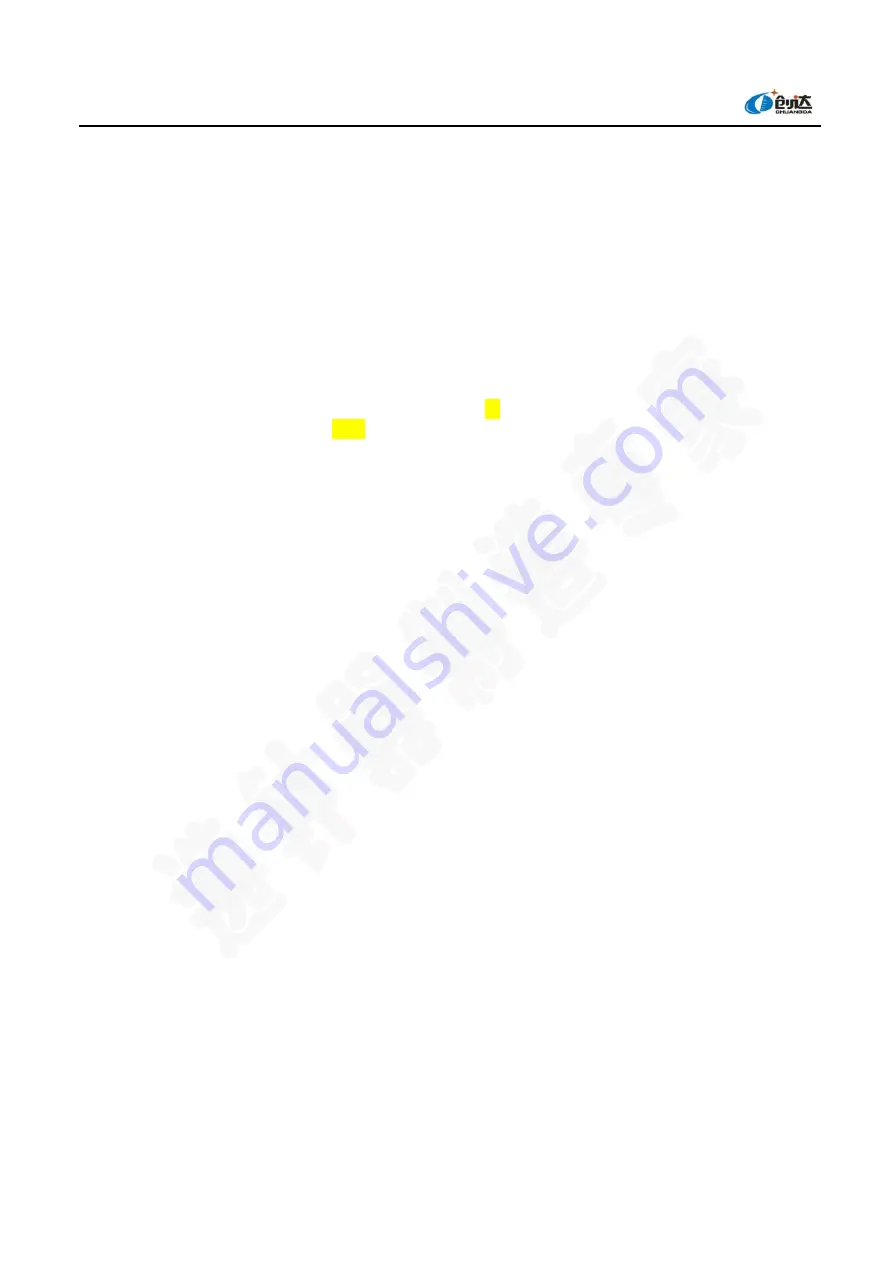
Guangdong Chuangda Automatic Equipment Co.,Ltd.
57
/
63
Add: D11, New Lighting Source Industrial Basis, Nanhai District, Foshan City, Guangdong Province
Tel: +86- 0757-82629566 82629546 82326616 Fax: +86- 0757-82622156
15 Troubleshooting of Common Problems
15-1 General Steps to Troubleshoot the Machine’s Failure to Make Patterns During Operation
1. Troubleshoot system program faults
In the main standby menu, use a sheet metal to keep the sensor active (photoelectric switch light is lit, the upper
left corner displays ON), start the machine to see if the machine can enter jacquard interface. If it can enter the
jacquard interface, then re-adjust the origin and the sensor to the appropriate positions, confirm that the connection
lines have no problem, if it cannot enter the Jacquard system, it can be judged that the system program has problems;
enter the next step.
2. Check whether the origin sensor can be triggered at high speed during operation
After starting the machine, check whether the sensor status can be displayed on the machine interface, or directly
observe whether the sensor light flashes when the machine runs to the sensor position. It not, readjust the sensor
position, and observe as above again. If the sensor is trigger ed, but the machine still fails to enter the jacquard
interface, enter the next step for further checl.
3. Check whether the position of the sensor and the pattern starting point of synchronizer are the same.
Move the needle cylinder to the zero position, check whether the
【
Adjustment Value
】
of the "synchronizer origin
adjustment setting" is close to 0, if there is a large deviation, adjust the position of the origin , and observe the result
again. And confirm that the sensor device is not loose. After it is confirm that the above items have no problem, but
the machine still cannot enter the jacquard interface, you can increase the sensing area of the sensor, or adjust the
【
Deviation Value
】
in the synchronizer origin adjustment and setting interface, so that the pattern start point is
slightly lag behind the sensor zero position.
4. Check whether the sensor hardware and connecting lines are have problems.
Enter the synchronizer origin adjustment and setting interface, rotate the needle cylinder to confirm whether the
adjusted value has changed, use a metal sheet to keep the sensor triggered, check whether
【
Zero Point Switch
】
on the
interface displays ON. And make sure that the cable is in good contact.
5. Check whether the synchronizer hardware, the shaft couplings and other related devices have problems
Enter the synchronizer check interface, refer to 2.4.3 synchronizer check steps, confirm that the synchronizer is
normal. Reassemble, and make sure that the couplings are free from slip, deformation, fracture and other failures.
6. If problems still exist after all above items are checked, then it can judged that the mechanical structure has
problems, such as problems in large disc gears or gearbox etc.
15-2 General Steps to Troubleshoot Why the Machine Makes Wrong Patterns During Operation
The following troubleshooting mainly focuses on a computer system failure, do not include knitting process details
Regular wrong patterns:
1. If mirror image patterns are knitted, check whether the needle cylinder rotation direction is correct, and confirm
that whether "reverse break down" is checked when making break down.
2. Check whether the corresponding knitting needles, thimbles, jacquard pieces, and actuator are abnormal
(including whether actuator codes are repeated)
3. Check whether the blowing mechanism repeatedly impacts a certain unit.
Irregular wrong patterns:
1. Check whether the synchronizer and needle cylinder rotation direction is set correctly, whether the band group is
set correctly (if there is a second band, confirm whether the function is enabled).
2. Check other parameters of the preliminary instructions, actuator units, angle, etc.
3. Check whether the synchronization ratio is set correctly, and make sure that the synchronizer and coupling have
no problem and are connected properly.
4. Check whether the large gear and gearbox of the machine are abnormal