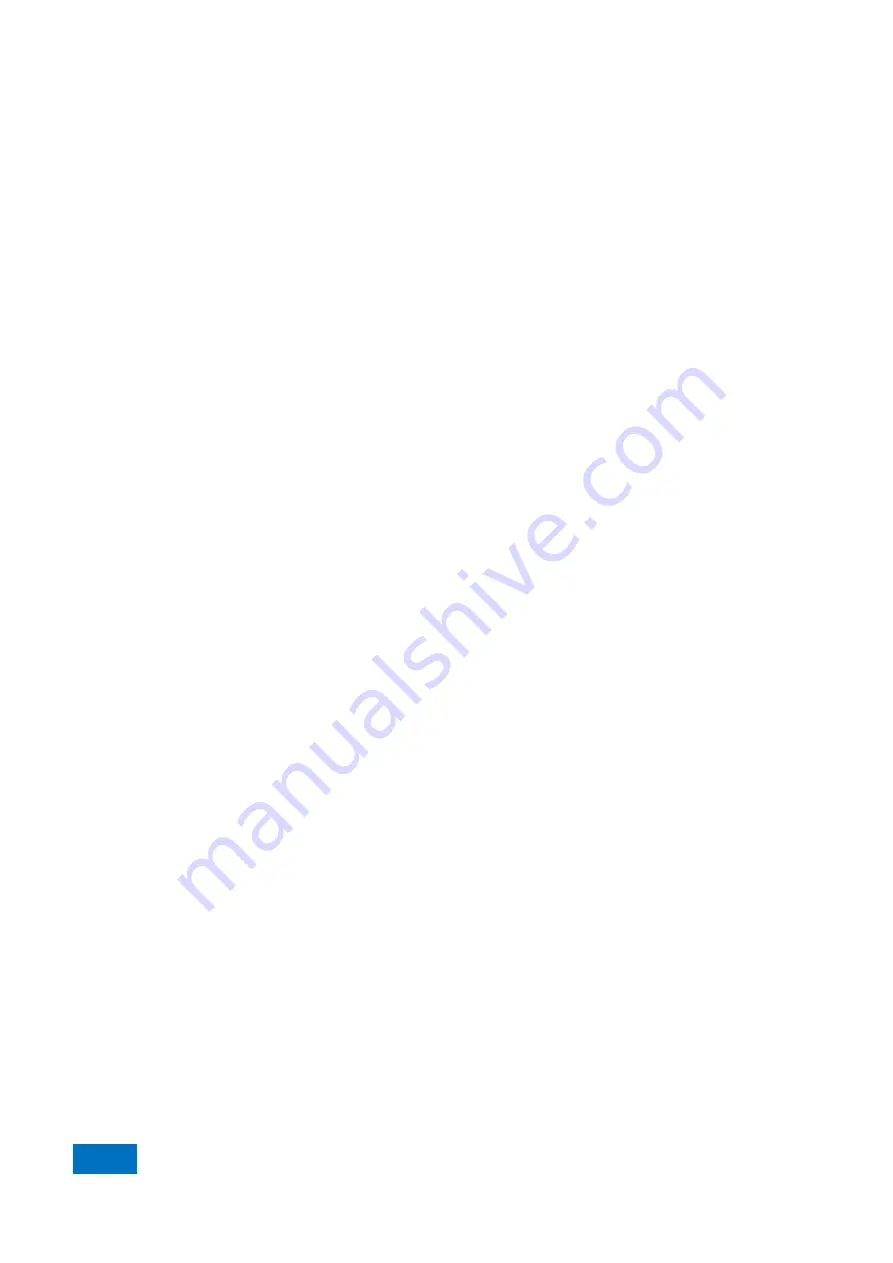
7 Calibration
7.5 Measurement Errors
216
7.5 Measurement Errors
Understanding of the source of measurement error and the way of error correction can help to improve the
measurement accuracy, as a certain degree of uncertainty still exits no matter how carefully the measurement is
done. The following kinds of errors may be produced in measurement with the analyzer.
7.5.1 Drift Errors
➢
Drift errors are produced by performance changes of the instrument or test system after calibration.
➢
The thermal expansion of the interconnected cables in the instrument and the performance changes of
microwave mixer are main causes of the drift error. The drift errors can be eliminated by recalibration.
➢
The duration of accurate calibration depends on the test environment. The stable environment can help to
minimize the drift error.
7.5.2 Random Errors
The random error cannot be predicted or eliminated by means of calibration. The influence on measurement results
can be reduced by some methods. Random errors are mainly divided into three types:
1) Random error of instrument
a) Electrical disturbance of internal components of the analyzer may result in random noise, mainly including:
➢
Low-level noise arising from the base noise within the receiver broadband;
➢
High-level noise or data trace jittering, which is mainly caused by the base noise inside the instrument and
phase noise of the LO source.
b) The random noise error can be reduced in the following methods:
➢
Increase the source power input into the DUT;
➢
Reduce the intermediate frequency bandwidth;
➢
Apply the function of sweep averaging.
2) Switch repeatability error
The switch is used to change attenuator settings of the source. If the switch acts, contact closing may be different
from previous closing sometimes. In this case, the measurement accuracy will be affected seriously. Therefore, the
attenuator settings should not be changed in high-accuracy measurement so as to reduce the switch repeatability
error.
3) Connector repeatability error
Connector wear may result in electrical performance changes. Proper connection maintenance can help to reduce
the connector repeatability error.
7.5.3 System Errors
System errors are caused by non-ideal hardware properties and may be repeatable (therefore, it can be predicted). It
is assumed that system errors do not change over time. System errors can be determined by calibration and
eliminated by mathematical calculation in measurement.
System errors cannot be fully eliminated. Due to limitations of the calibration process, some residual errors may
exist after calibration, mainly resulting from:
➢
Non-ideal calibration standard;
➢
Connector connection;
➢
Interconnected cable;
➢
Instrument.
All measurements are affected by the dynamic accuracy and frequency errors. For reflection measurement, relevant
residual errors include:
Содержание AV3672 Series
Страница 1: ...AV3672 Series Vector Network Analyzer User Manual China Electronics Technology Instruments Co Ltd...
Страница 3: ......
Страница 4: ...AV3672 Series Vector Network Analyzer Contents...
Страница 5: ......
Страница 124: ...5 Menu 5 1 Menu structure 120 5 1 2 Track Fig 5 2 Track Menu...
Страница 125: ...5 Menu 5 1 Menu structure 121 5 1 3 Channel Fig 5 3 Channel Menu...
Страница 126: ...5 Menu 5 1 Menu structure 122 5 1 4 Excitation Fig 5 4 Excitation Menu I...
Страница 127: ...5 Menu 5 1 Menu structure 123 Fig 5 5 Excitation Menu II...
Страница 128: ...5 Menu 5 1 Menu structure 124 Fig 5 6 Excitation Menu III...
Страница 129: ...5 Menu 5 1 Menu structure 125 5 1 5 Response Fig 5 7 Response Menu I...
Страница 130: ...5 Menu 5 1 Menu structure 126 Fig 5 8 Repsonse Menu II...
Страница 131: ...5 Menu 5 1 Menu structure 127 Fig 5 9 Response Menu III...
Страница 132: ...5 Menu 5 1 Menu structure 128 Fig 5 10 Response Menu V Fig 5 11 Response IV...
Страница 133: ...5 Menu 5 1 Menu structure 129 5 1 6 Calibration Fig 5 12 Calibration Menu...
Страница 134: ...5 Menu 5 1 Menu structure 130 5 1 7 Marker Fig 5 13 Cursor Menu I...
Страница 135: ...5 Menu 5 1 Menu structure 131 Fig 5 13 Cursor Menu II...
Страница 136: ...5 Menu 5 1 Menu structure 132 Fig 5 15Marker Menu III...
Страница 137: ...5 Menu 5 1 Menu structure 133 5 1 8 Analysis Fig 5 16 Analysis Menu I...
Страница 138: ...5 Menu 5 1 Menu structure 134 Fig 5 17 Analysis Menu II...
Страница 139: ...5 Menu 5 1 Menu structure 135 Fig 5 18 Analysis Menu III...
Страница 140: ...5 Menu 5 1 Menu structure 136 5 1 9 System Fig 5 19 System Menu I...
Страница 141: ...5 Menu 5 1 Menu structure 137 Fig 5 20 System Menu I...
Страница 254: ...8 Basis of Network Measurement 8 3 Amplifier Parameter Specifications 250...
Страница 257: ...8 Basis of Network Measurement 8 4 Complex Impedance 253...
Страница 366: ...Appendix Appendix 3 Frequency Offset Measurement 362 Fig 3 13 Test of Return Loss of Mixer LO Port...
Страница 373: ...Appendix Appendix 4 Pulse Measurement 369 Fig 4 9 Receiver gain configuration Dialog Box...