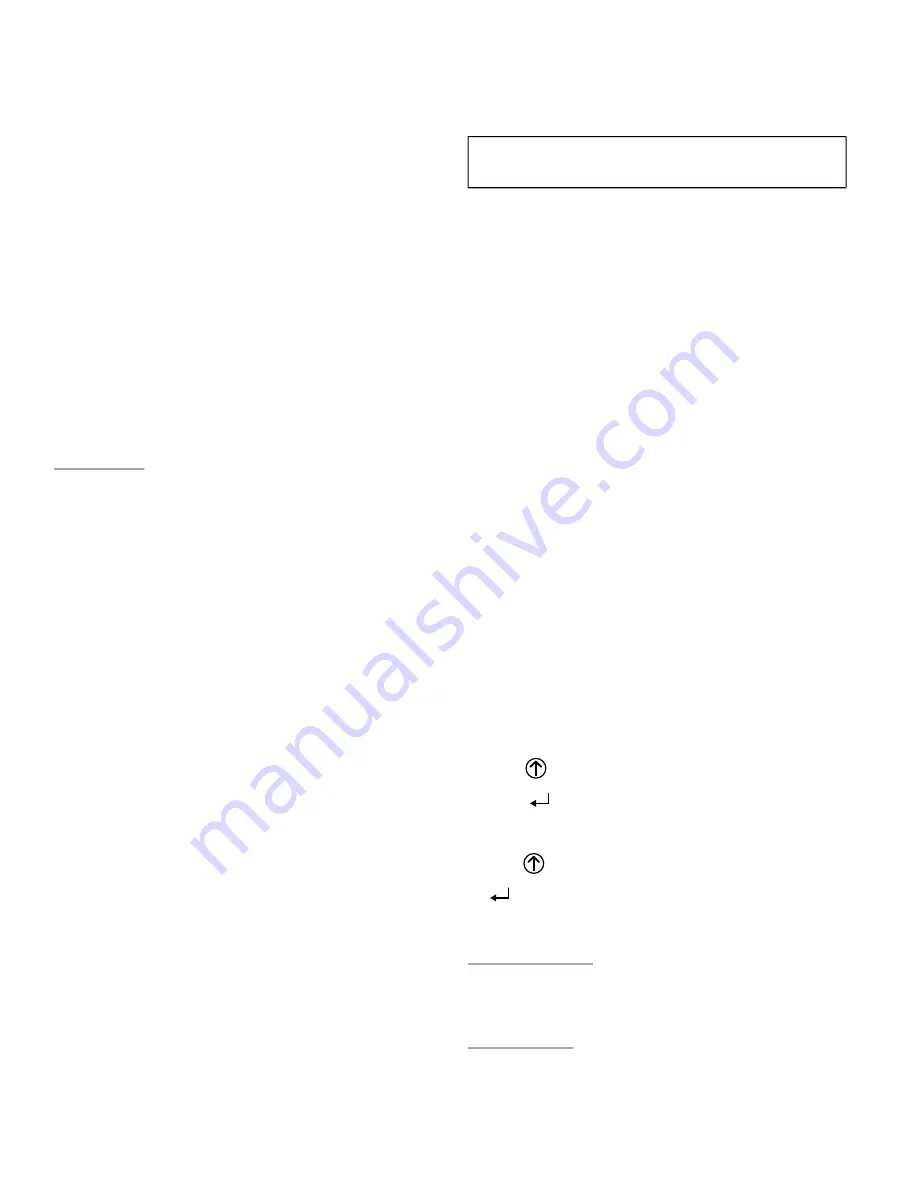
60
As space temperature falls, the thermostat will remove its call for
second stage cooling; ISC terminal Y2 call is removed. The sup
-
ply fan motor remains High Speed. The outside air damper limit is
repositioned to between MIN POS L and 100% open. Second
stage cooling (Compressor 1 operation) stops. As space tempera
-
ture continues to fall and space cooling load is satisfied, the ther
-
mostat will remove its call for first stage cooling; ISC terminal Y1
call is removed. The W7220 input Y1-I is removed; free cooling
mode ends. Outside air damper will remain at MIN POS L if sup
-
ply fan remains in operation (CONT FAN) or to closed if supply
fan stops (AUTO FAN).
Should 100% outside air and second stage cooling (Compressor 1
operation) not be capable of satisfying the space cooling load,
space temperature will rise and the thermostat will call for third
stage cooling: ISC terminal Y3 is also energized, starting third
stage cooling (Compressor 2 operation). The supply fan motor
will remain at High Speed. The Y3 demand is received at W7220
input Y2-I. The outdoor air damper position will modulate from
MIN POS H to 100% Open to maintain SAT at MAT SET concur
-
rent with Compressor 2 operation.
As space temperature falls, the thermostat will remove its call for
third stage cooling; ISC terminal Y3 call is removed. The supply
fan will remain at High Speed. The W7220 input Y2-I is also re
-
moved; the outside air damper is repositioned to modulate from
MIN POS L to 100% Open, third stage cooling (Compressor 2 op
-
eration) stops.
Power Exhaust
If accessory power exhaust is installed, the power exhaust fan mo
-
tors will be energized by the economizer control as the dampers
open above the setpoint EXH1 SET L during Low Speed opera
-
tion or EXH1 SET H during High Speed fan operation. The EXH1
output will be de-energized as the dampers close below the EXH1
setpoint value.
Damper movement from full closed to full open (or vice versa)
will take approximately 1
1
/
2
minutes.
Heating with EconoMi$er
®
X
When the space temperature calls for heat (W1 closes), ISC termi
-
nal W1 is energized. The supply fan will start and run in High
Speed. The W1 signal will connect to W7220 input AUX2I; the
outside air damper will move to MIN POS H. Unit heating se
-
quence will follow base unit control sequences.
Demand Controlled Ventilation
If a space or return air CO
2
sensor is connected to the EconoMi$er
X control, a Demand Controlled Ventilation strategy will operate
automatically.
When the space CO
2
level is below setpoint DCV SET (default
1100 ppm), the minimum ventilation position for the outside air
damper will be reset to lower settings suited for offsetting CO
2
loads from space sources not including people. The settings will
vary according to supply fan speed. When the supply fan speed is
Low, the DCV minimum ventilation point is VENTMIN L. When
the supply fan speed is High, the DCV minimum ventilation point
is VENTMAX H.
As the CO
2
level in the space increases above the setpoint DCV
SET (default 1100 ppm), the DCV ventilation position of the out
-
side air damper will be increased proportionally, until the Maxi
-
mum Ventilation setting is reached. The settings will vary accord
-
ing to supply fan speed. When the supply fan speed is Low, the
DCV maximum ventilation point is VENTMAX L. When the
supply fan speed is High, the DCV maximum ventilation point is
VENTMAX H.
DCV operation will float between its VENTMIN and VENT
-
MAX settings, never exceeding the VENTMAX limit as the space
CO
2
level varies according to changes in people occupancy levels.
During concurrent demand for DCV and free cooling, the out
-
door-damper will follow the higher demand condition from the
DCV mode or from the free-cooling mode.
W7220 ECONOMIZER SETUP AND CONFIGURATION
Before being placed into service, the W7220 Economizer module
must be setup and configured for the installed system according to
project control specifications.
Inspect all wiring connections at the Economizer module’s termi
-
nals, and verify compliance with the installation wiring diagrams.
See Fig. 77 for typical wiring.
Initial Menu Display
On initial start up, Honeywell displays on the first line and Econo
-
mizer W7220 on the second line. After a brief pause, the software
revision number appears on the first line and the second line is
blank.
Time-Out and Screensaver
When no buttons have been pressed for 10 minutes, the LCD
displays a screen saver, which cycles through the Status items.
Each Status item displays in turn and cycles to the next item after
5 seconds.
Setup and Configuration Menus
Setup and configuration involves stepping through three menus
(SYSTEM SETUP, ADV SETUP and SETPOINTS) to enable re
-
quired functions, and re-selecting setpoints to meet project re
-
quirements. Use the Control Setpoint and Configuration Log on
page 63 to record the settings for this specific project.
NOTE: The W7220 controller will be in the “set up” mode for the
first 60 minutes after it is powered. If a sensor for OA air or S-bus
device (sensor, actuator) is disconnected during the set up mode,
the W7220 controller will not signal that failure with an alarm.
The SAT sensor is a system “critical” sensor. If the SAT sensor is
removed during the set up mode, the W7220 will send an alarm.
After 60 minutes the W7220 controller will change to operation
mode and all components removed or failed will generate alarms
in the operation mode.
For this application with the 2-speed supply fan option, note that
parameters EQUIPMENT, AUX2I and FAN TYPE have re
-
quired settings. Check that these parameters are set at these re
-
quired settings:
• EQUIPMENT must be CONV
• AUX2I must be W
• FAN SPEED must be 2SPEED
Press the
(Exit) button exit the SYSTEM SETUP menu and
return to top level menu. Scroll down to ADV SETUP menu and
press the
(Enter) button to enter this menu. Scroll down
through the list of parameters and adjust settings as required. Be
sure that the message CHANGE STORED appears with every
change in parameter setting.
Press the
(Exit) button exit the ADV SETUP menu and return
to top level menu. Scroll down to SETPOINTS menu and press
the
(Enter) button to enter this menu. Scroll down through the
list of parameters and adjust settings as required. Be sure that the
message CHANGE STORED appears with every change in pa
-
rameter setting.
SETPOINT Defaults
The default setpoint values represent many years of successful
experience with economizing systems. Any changes that repre
-
sent significant deviations from the default values should be well
considered.
DCV SETPOINT
The default value for DCV SET is 1100 ppm. It is recommended
that this setpoint be adjusted down to 500 ppm (or CO
2
level of
outdoor air plus 100 ppm, whichever is higher) to permit an earlier
initiation of the DCV mode as space occupancy increases.
IMPORTANT: During setup, the economizer module is
live at all times.
Содержание WeatherExpert 50LC14
Страница 4: ...4 Fig 2 50LC Vertical Airflow Size 14...
Страница 5: ...5 Fig 3 50LC Horizontal Airflow Size 14...
Страница 6: ...6 Fig 4 50LC Back View and Condensate Drain Location Size 14...
Страница 7: ...7 Fig 5 50LC Corner Weights and Clearances Size 14...
Страница 8: ...8 Fig 6 50LC Bottom View Size 14...
Страница 9: ...9 Fig 7 50LC Vertical Airflow Sizes 17 20...
Страница 10: ...10 Fig 8 50LC Horizontal Airflow Sizes 17 20...
Страница 11: ...11 Fig 9 50LC Back View and Condensate Drain Location Sizes 17 20...
Страница 12: ...12 Fig 10 50LC Corner Weights and Clearances Sizes 17 20...
Страница 13: ...13 Fig 11 50LC Bottom View Sizes 17 20...
Страница 14: ...14 Fig 12 50LC Vertical Airflow Sizes 24 26...
Страница 15: ...15 Fig 13 50LC Horizontal Airflow Sizes 24 26...
Страница 16: ...16 Fig 14 50LC Back View and Condensate Drain Location Sizes 24 26...
Страница 17: ...17 Fig 15 50LC Corner Weights and Clearances Sizes 24 26...
Страница 18: ...18 Fig 16 50LC Bottom View Sizes 24 26...
Страница 21: ...21 Fig 19 Roof Curb Details 14 Size Unit...
Страница 22: ...22 Fig 20 Roof Curb Details 17 and 20 Size Units...
Страница 23: ...23 Fig 21 Roof Curb Details 24 and 26 Size Units...
Страница 30: ...30 Fig 42 50LC 14 26 Electro Mechanical Control Wiring Diagram...
Страница 31: ...31 Fig 43 50LC 14 26 RTU Open Control Wiring Diagram...
Страница 32: ...32 Fig 44 50LC 14 26 SystemVu Control Wiring Diagram...
Страница 33: ...33 Fig 45 Typical Power Wiring Diagram Electro Mechanical and RTU Open Controls 50LC 14 24 Units 208 230V Shown...
Страница 35: ...35 Fig 47 Typical Power Wiring Diagram SystemVu Controls 50LC Unit 208 230V Shown...
Страница 36: ...36 Fig 48 Typical Power Wiring Diagram SystemVu Controls 50LC Unit 460V 575V Shown...
Страница 80: ......
Страница 81: ......