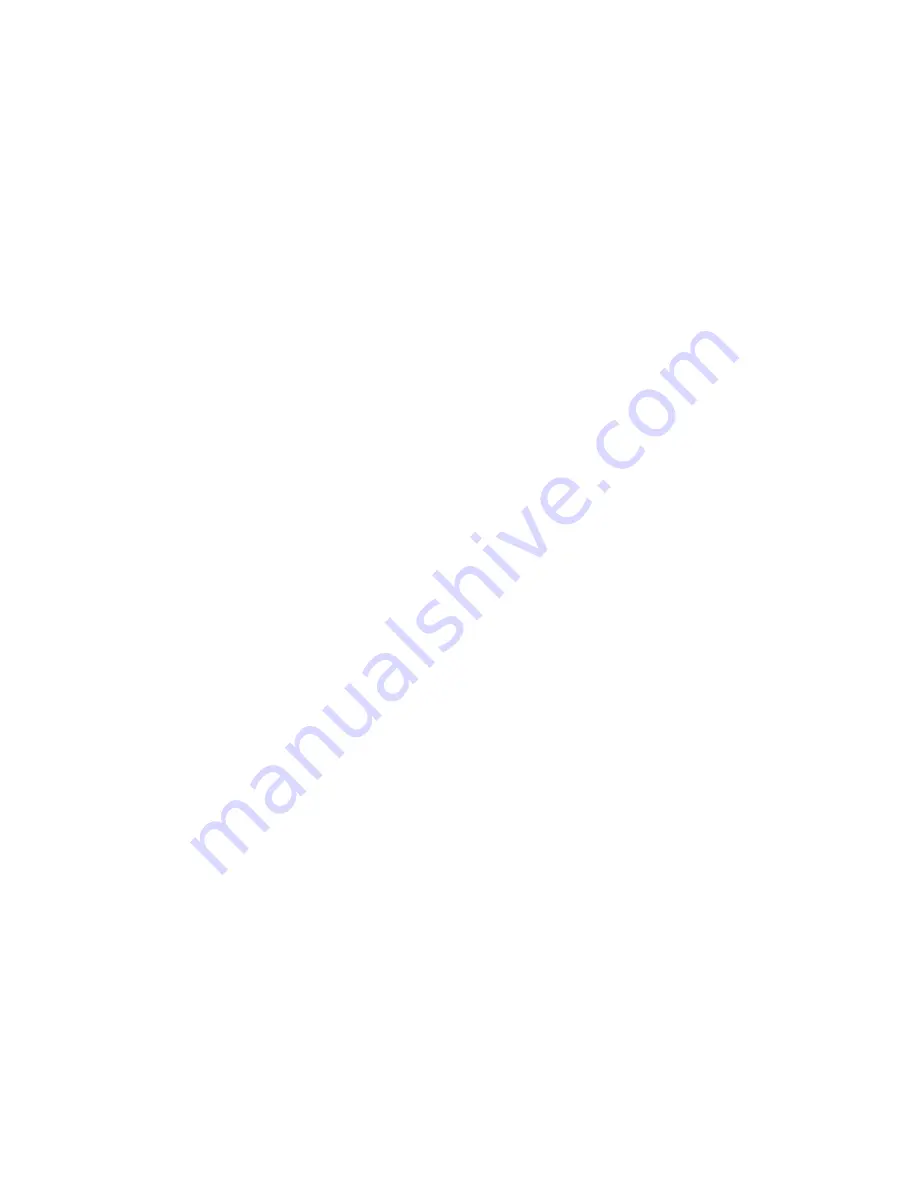
75
• In Navigator display, this test shall be located at
Service
Test
AC.DT
EC.TS
.
• Running the test shall require setting
Service
Test
TEST
=ON
The test shall also automatically run based on
EC.DY
(T24_
-
ECDY) and
EC.TM
(T24_ECTM):
• If conditions are acceptable to run the self-test (see below),
the test shall be automatically started on the configured
day
EC.DY
(T24_ECDY) at the configured time
EC.TM
(T24_ECTM).
• If conditions are not acceptable to run the self-test, it shall
be re-scheduled for 24 hours later.
The economizer self-test shall only be allowed to run if all of
the following conditions are valid:
1. The economizer is enabled
2. No actuators are detected as stuck
3. No actuators are detected as unavailable
4. RCB1 is properly communicating
5. The unit is not down due to failure (A152)
6. The supply fan VFD is not in bypass mode (if unit has this
option)
7. If configured for building pressure, the unit has a return
fan VFD and the fan is not in bypass mode
In addition to the above conditions, the economizer self-test
shall not be automatically run if any of the following condi
-
tions are valid:
1. Unit not in OFF or VENT mode.
The Test screen should be similiar to the following:
EC.TR
ON
EC.DT
WAITING
S.VFD
20.0 %
TORQ
17.5 %
ECN.P
20 %
EC2.P
0 %
EC3.P
0 %
EC.ST
RUNNING
Setting
EC.TS
=ON shall perform the following:
2. Command all actuators and dampers to the closed position.
3. Run the fan at T24SFSPD for T24ACMRT minutes and
take a baseline torque (VFD1TMAV) measurement. With
the dampers closed, there will be the least amount of air
-
flow, and therefore the least amount of motor torque.
4. Modulate a single actuator/damper assembly open to
T24ACOPN. This will increase the airflow.
5. Let the motor run for one minute. If the torque has
increased by T24VFDPC % over the baseline measure
-
ment from Step 2, the current torque is set as the new base
-
line measurement; proceed to Step 5. If the torque has not
increased by T24VFDPC %, continue to run the fan for a
total of T24ACMRT minutes. If, after T24ACMRT min
-
utes total, the torque has not increased by T24VFDPC %
over the Step 2 baseline measurement, a fault is logged,
and the test is ended.
6. Modulate the actuator/damper assembly closed.
7. Let the motor run for one minute. If the torque has
decreased by T24VFDPC % over the baseline measure
-
ment from Step 4, the current torque is set as the new base
-
line measurement; proceed to Step 7. If the torque has not
decreased by T24VFDPC %, continue to run the fan for a
total of T24ACMRT minutes. If, after T24ACMRT min
-
utes total, the torque has not decreased by T24VFDPC %
below the Step 4 baseline measurement, a fault is logged,
and the test is ended.
8. Repeat Steps 1-5 for additional actuator/damper assemblies.
9. Command actuators/dampers to “normal” positions.
If the torque increases and decreases properly,
EC.ST
=
“PASS,” otherwise
EC.ST
=“FAIL.”
If
EC.ST
is set to pass, any existing “damper not modulating”
alert shall be automatically cleared.
If
EC.ST
is set to fail, the “damper not modulating” alert shall
be logged.
If at any point in the test the fan does not reach the command
speed or an actuator does not reach the command position
within 5 minutes, the test shall be stopped and the status set to
“NOT RUN.”
FDD CONFIGURATIONS
Log Title 24 Faults
(LOG.F)
Enables Title 24 detection and logging of mechanically discon
-
nected actuator faults.
T24 Econ Move Detect
(EC.MD)
Detects the amount of change required in the reported position
before economizer is detected as moving.
T24 Econ Move SAT Test
(EC.ST)
The minimum amount the economizer must move in order to
trigger the test for a change in SAT. The economizer must
move at least
EC.ST
% before the control will attempt to deter
-
mine whether the actuator is mechanically disconnected.
T24 Econ Move SAT Change
(S.CHG)
The minimum amount (in degrees F) SAT is expected to
change based on economizer position change of
EC.ST
.
T24 Econ RAT-OAT Diff
(E.SOD)
The minimum amount (in degrees F) between RAT (if avail
-
able) or SAT (with economizer closed and fan on) and OAT to
perform mechanically disconnected actuator testing.
T24 Heat/Cool End Delay
(E.CHD)
The amount of time (in minutes) to wait before mechanical
cooling or heating has ended before testing for mechanically
disconnected actuator. This is to allow SAT to stabilize at con
-
clusion of mechanical cooling or heating.
T24 Test Minimum Position
(ET.MN)
The minimum position below which tests for a mechanically dis
-
connected actuator will not be performed. For example, if the ac
-
tuator moves entirely within the range 0 to
ET.MN
,
a determina
-
tion of whether the actuator is mechanically disconnected will not
be made. This is due to the fact that at the extreme ends of the ac
-
tuator movement, a change in position may not result in a detect
-
able change in temperature. When the actuator stops in the range 0
to 2% (the actuator is considered to be closed), a test shall be per
-
formed where SAT is expected to be approximately equal to RAT.
If SAT is not determined to be approximately equal to RAT, a
“damper not modulating” alert shall be logged.
T24 Test Maximum Position
(ET.MX)
The maximum position above which tests for a mechanically dis
-
connected actuator will not be performed. For example, if the ac
-
tuator moves entirely within the range
ET.MX
to 100 a determina
-
tion of whether the actuator is mechanically disconnected will not
be made. This is due to the fact that at the extreme ends of the ac
-
tuator movement, a change in position may not result in a detect
-
able change in temperature. When the actuator stops in the range
98 to 100% (the actuator is considered to be open), a test shall be
performed where SAT is expected to be approximately equal to
OAT. If SAT is not determined to be approximately equal to OAT,
a “damper not modulating” alert shall be logged.
Содержание WeatherExpert 48N2
Страница 135: ...135 Fig 18 48 50N Typical Power Schematic Nominal 075 Ton Unit Shown ...
Страница 136: ...136 Fig 19 48 50N Typical Power Schematic Nominal Ton 90 150 Units Shown ...
Страница 137: ...137 Fig 20 48 50N Main Base Board Input Output Connections ...
Страница 138: ...138 Fig 21 48 50N RXB EXB CEM Input Output Connections a48 9307 ...
Страница 139: ...139 Fig 22 48 50N EXV SCB Input Output Connections a48 9308 ...
Страница 140: ...140 Fig 23 48N Typical Modulating Gas Heat Unit Control Wiring ...
Страница 141: ...141 Fig 24 50N Typical Electric Heat Unit Control Wiring ...
Страница 144: ...144 Fig 27 48N Typical Gas Heat Section Wiring Nominal Ton 120 to 150 Units ...
Страница 145: ...145 Fig 28 48 50N Typical Power Component Control Wiring 460 v ...
Страница 146: ...146 Fig 29 48 50N Component Control Wiring 575 v Nominal Ton 075 to 150 Units ...
Страница 147: ...147 Fig 30 48 50N Component Arrangement Power Box ...
Страница 148: ...148 Fig 31 48 50N Component Arrangement Control Box ...
Страница 168: ...168 Fig 47 Sensor and Ignition Position Fig 48 Combustion Blower Details SENSOR DETAILS IGNITION DETAILS ...
Страница 240: ...240 APPENDIX D VFD INFORMATION CONT Fig G VFD Bypass Wiring Diagram WHEN USED ...