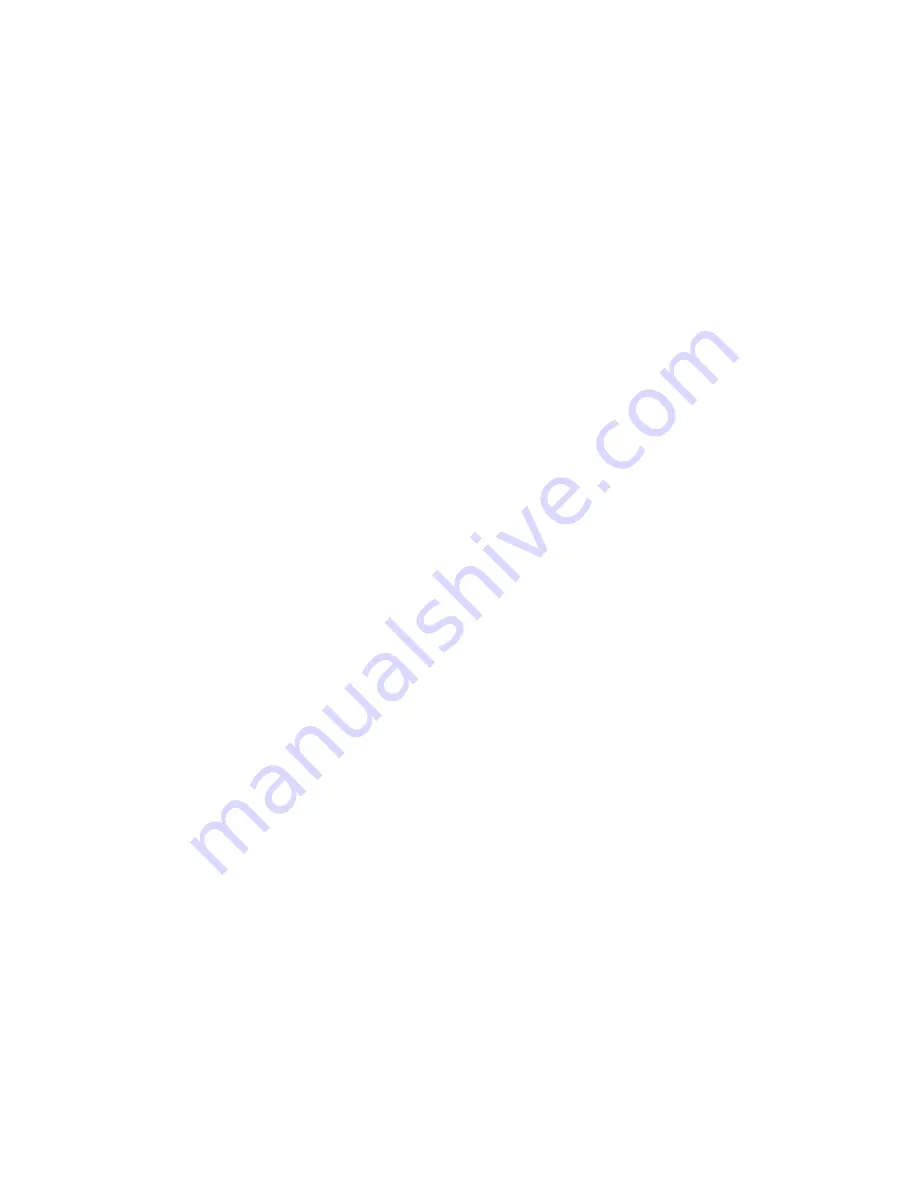
36
The EXV auto-component test functions by staging compres
-
sor A1, B1, and B2 for a 75-ton unit and A1, A2, B1, B2 for
other units, and verifying the superheat is within
±
AC_SH_DB
(auto-component test superheat deadband) of
the superheat set point (
SH.SP
).
The auto-component test superheat deadband (
AC_SH_DB
)
will default to 2°F with a range of 0°F to 10°F.
Setting
EX.TR
=ON will perform the following:
1. Stage compressors A1/B1/B2 for 75-ton unit, A1/A2/B1/
B2 for other units.
2. Allow compressors to run for 5 minutes.
3. Verify that
SH.A1
,
SH.A2
,
SH.B1
, and
SH.B2
have stabi
-
lized to
SH.SP
±
AC_SH_DB
. If all 4 superheats are
SH.SP
±
AC_SH_DB
then set PASS status and end test.
4. If any superheat is outside
SH.SP
±
AC_SH_DB
, allow
compressors to run for 5 more minutes.
5. Set PASS/FAIL status according to whether each super
-
heat has stabilized to
SH.SP
±
AC_SH_DB
and end test.
If
SH.SP
±
AC_SH_DB
then
XA1S, XA2S, XB1S,
and
XB2S
=PASS, otherwise
XA1S, XA2S, XB1S,
and
XB2S
=FAIL.
If the EXV superheat is not within
SH.SP
±
SH.DB
, the super
-
heat alert will be logged:
Refrigerant Charge Auto-Test (without Liquid
Sensors)
The refrigerant charge auto test without liquid sensors requires
the following conditions:
1. Unit is not shut down due to failure (A152).
2. OAT>70°F.
3. No compressors are on or requested on.
4. All compressors are available for staging.
The test screen will display the following:
When no liquid sensors are installed, all compressors and outdoor
fans of both Circuit A and B are commanded to be ON. The oper
-
ator will read
OAT
,
SCT.A
, and
SST.A
in order to then compare
the values to the A charging chart to determine if refrigerant in
Circuit A is properly charged. The operator reads
OAT
,
SCT.B
,
and
SST.B
, in order to then compare the values to the B charging
chart to determine if refrigerant in Circuit B is properly charged.
Thus this is a semi-auto test because operator intervention is re
-
quired to determine the test results. No test results are displayed.
Setting
CD.TR
=ON will perform the following:
1. Command supply fan ON.
2. Command all A and B Circuit outdoor fans ON.
3. Stage all A and B Circuit compressors ON.
4. Let compressors run 5 minutes.
5. Prompt user to read charging charts.
6. Let compressors run 5 minutes.
7. End test.
Minimum Load Valve Auto-Component Test
Minimum load valve (MLV) is also referred to as hot gas by
-
pass valve (HGBV).
The hot gas bypass auto-component test requires the following
conditions:
1. Unit is not shut down due to failure (A152).
2.
MLV
=ENBL.
3. No compressors are on or requested on.
4. Compressor A1 is available to start.
The test screen will display the following:
The MLV auto-component test functions by comparing the dis
-
charge pressure when MLV is closed to that when MLV is
open, and verifying
DP.A
decreases by at least
AC_MLVDR
.
The auto-component MLV deadband (
AC_MLVDR
) will de
-
fault to 5 psig with a range of 0 to 10 psig.
Setting
ML.TR
=ON will perform the following:
1. Command A1 ON and
MLV
OFF.
2. Let circuit stabilize for 5 minutes and save
DP.A
(recorded).
3. Command
MLV
ON.
4. Let circuit stabilize for 5 minutes and record
DP.A
(current).
5. Verify
DP.A
(recorded) -
DP.A
(current) >
AC_MLVDR
.
6. End test.
If
DP.A
(recorded) –
DP.A
(current) >
AC_MLVDR
then
ML.ST
=PASS, otherwise
ML.ST
=FAIL.
Supply Fan Auto-Component Test
The supply fan auto-component test requires the following
conditions:
1. Unit is not shut down due to failure (A152).
2. Supply fan VFD not in bypass mode.
3. Power exhaust or return fan (if enabled) not in bypass mode.
4. Supply fan not on.
The test screen will display this:
The supply fan auto-component test functions by commanding the
supply fan to minimum speed (
STATPMIN
), and verifying that
VFD power (
S.PWR
) and duct static pressure (
SP
) is increasing.
Setting
SF.TR
=ON will perform the following:
1. Record
S.PWR
and
SP
.
2. Command
S.VFD
to
STATPMIN
, and let run 5 minutes.
3. Verify
S.PWR
increases.
4. If
SP.CF
=ENBL and
SP.S
=ENBL, verify
SP
increases.
5. End test.
XA1S
Running
EXV A1 Auto-Test Status
XA2S
Running
EXV A2 Auto-Test Status
XB1S
Running
EXV B1 Auto-Test Status
XB2S
Running
EXV B2 Auto-Test Status
T064
EXV A1 Superheat Outside Range
T065
EXV A2 Superheat Outside Range
T066
EXV B1 Superheat Outside Range
T067
EXV B2 Superheat Outside Range
CD.TR
ON
Run Chrg Test without Lqd Sen
CD.ET
Running Test Status and Timer
SCT.A
105.3 F Cir A Sat. Condensing Temp
SST.A
50.4 F
Cir A Sat. Suction Temp
OAT
66.3 F
Outside Air Temp
SCT.B
106.5 F Cir A Sat. Condensing Temp
SST.B
49.8 F
Cir A Sat. Suction Temp
ML.TR
No
Run MLV/HGBV Auto-Test
ML.TD
Running 1/1 Test Status and Timer
MLV
Off
Minimum Load Valve Relay
DP.A
331.3 psig
Cir A Discharge Pressure
ML.ST
Running
MLV/HGBP AutoTest Result
SF.TR
ON
Run Supply Fan Auto-Test
SF.DT
Running
Test Status and Timer
S.VFD
0%
VFD1 Actual Speed %
S.PWR
0.00 kW
VFD1 Actual Motor Power
SP
0.00˝ H20
Static Pressure
SF.ST
Pass
SF Auto-Test Result
Содержание WeatherExpert 48N2
Страница 135: ...135 Fig 18 48 50N Typical Power Schematic Nominal 075 Ton Unit Shown ...
Страница 136: ...136 Fig 19 48 50N Typical Power Schematic Nominal Ton 90 150 Units Shown ...
Страница 137: ...137 Fig 20 48 50N Main Base Board Input Output Connections ...
Страница 138: ...138 Fig 21 48 50N RXB EXB CEM Input Output Connections a48 9307 ...
Страница 139: ...139 Fig 22 48 50N EXV SCB Input Output Connections a48 9308 ...
Страница 140: ...140 Fig 23 48N Typical Modulating Gas Heat Unit Control Wiring ...
Страница 141: ...141 Fig 24 50N Typical Electric Heat Unit Control Wiring ...
Страница 144: ...144 Fig 27 48N Typical Gas Heat Section Wiring Nominal Ton 120 to 150 Units ...
Страница 145: ...145 Fig 28 48 50N Typical Power Component Control Wiring 460 v ...
Страница 146: ...146 Fig 29 48 50N Component Control Wiring 575 v Nominal Ton 075 to 150 Units ...
Страница 147: ...147 Fig 30 48 50N Component Arrangement Power Box ...
Страница 148: ...148 Fig 31 48 50N Component Arrangement Control Box ...
Страница 168: ...168 Fig 47 Sensor and Ignition Position Fig 48 Combustion Blower Details SENSOR DETAILS IGNITION DETAILS ...
Страница 240: ...240 APPENDIX D VFD INFORMATION CONT Fig G VFD Bypass Wiring Diagram WHEN USED ...