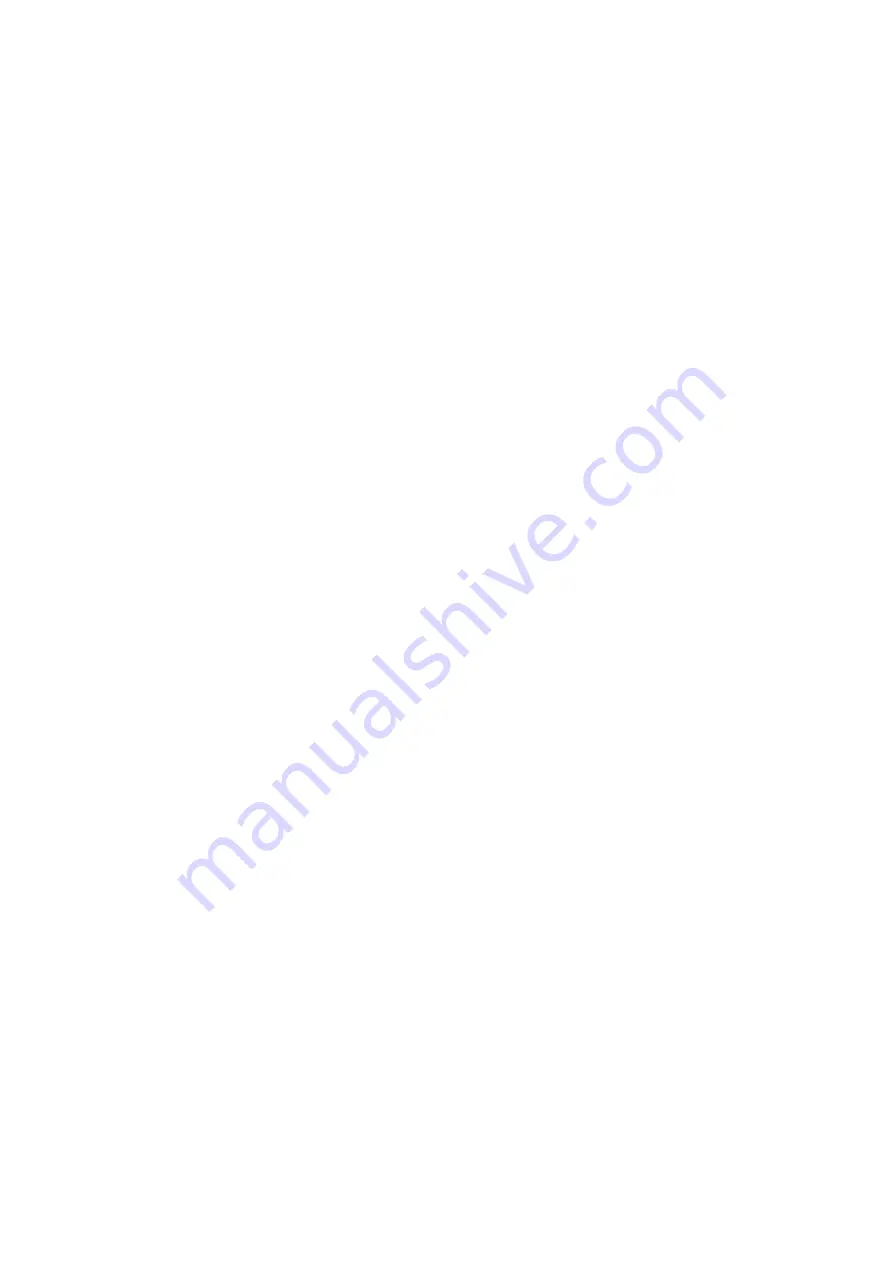
48
3.5.2 Install vent piping to relief devices
If the relief valves are installed on a change-over manifold, this is equipped with a relief valve on each of the two
outlets. Only one of the two relief valves is in operation, the other one is isolated. Never leave the change-over valve
in the intermediate position, i.e. with both ways open (Bring the actuator in abutment, front or back according to the
outlet to isolate). If a relief valve is removed for checking or replacement please ensure that there is always an active
relief valve on each of the change-over valves installed in the unit.
All factory-installed relief valves are lead-sealed to prevent any calibration change. The external safety valves are
designed and installed to ensure damage limitation in case of a fire. In accordance with the regulations applied for
the design, the European directive on equipment under pressure and in accordance with the national usage
regulations:
• These safety valves are not safety accessories but damage limitation accessories in case of a fire,
• The high pressure switches are the safety accessories.
The relief valve must only be removed if the fire risk is fully controlled and after checking that this is allowed by
local regulations and authorities. This is the responsibility of the operator.
The external safety valves must in principle be connected to discharge pipes for units installed in a room. Refer to
the installation regulations, for example those of European standards EN 378 and EN 13136.
If a safety valve is replaced, do not leave the machine without safety valves. Only remove the safety valve, if the
risk of fire is completely controlled and under the responsibility of the user. Only one safety valve at a time must be
removed and replaced so that fire protection is maintained during this operation. Please refer to
“Safety
considerations”.
Vent relief devices to the outdoors in accordance with the applicable national standard (for example, NFE 35400 in
France and EN 378 when applicable) for the safety of chilling devices as well as any other applicable codes.
DANGER: Refrigerant discharged into confined spaces can displace oxygen and cause asphyxiation.
If relief devices are manifolded, the cross-sectional area of the relief pipe must at least equal the sum of the areas
required for individual relief pipes.
Provide a pipe plug near outlet side of each relief device for leak testing. Provide pipe fittings that allow vent piping
to be disconnected periodically for inspection of valve mechanism.
Piping connected to relief devices must not apply stress to the device. Adequately support piping. A length of flexible
tubing or piping near the device is essential on spring isolated machines.
Cover the outdoor vent with a rain cap and place a condensation drain at the low point in the vent piping to
prevent water build-up on the atmospheric side of the relief device.
Equip the piping with connections to allow disconnection of the piping for inspection.
See figure 2, item 20 and 21 for relief valves location.
3.5.3 Purge discharge
Purge discharge shall be connected to the safety valve vent line assembly with 9.6 mm flare connection to the
discharge line from purge unit.
See figure 10, item 10 for purge discharge location.
3.6 Step 5
– Electrical connection
Field wiring must be installed in accordance with job wiring diagrams and all applicable electrical codes.
CAUTION:
Do not run any hazardous voltage wiring in the control panel sections associated with extra-low voltage wiring.
Damage to machine could occur as a result.
Do not run 50 volt or higher wiring into the PIC5+ Touch screen Panel and Control Panel. The panel should only
be used for low voltage wiring (50V max).
Wiring diagrams in this publication are for reference only and are not intended for use during actual installation;
follow job specific wiring diagrams.
CAUTION:
Do not attempt to start compressor or any motor (even for a rotation check) or apply test voltage of any kind to the
VFD or motor while the chiller is under a dehydration vacuum. Motor insulation breakdown and serious damage
may result.
Содержание PIC 5+
Страница 26: ...26 VFD not shown Fig 13 Sensors actuators location ...
Страница 52: ...52 Fig 24 19DV control box ...
Страница 53: ...53 1 Power supply 24V AC 2 LEN 3 CCN 4 Ethernet 5 USB Fig 25 19DV HMI box rear view ...
Страница 54: ...54 Fig 26 19DV IOB1 wiring Fig 27 19DV IOB2 wiring ...
Страница 57: ...57 ...
Страница 113: ...113 APPENDIX A SmartView SCREEN AND MENU STRUCTURE ...
Страница 114: ...114 Detailed menu description ...
Страница 116: ...116 APPENDIX B MAINTENANCE SUMMARY AND LOGSHEETS Cont 19DV monthly Maintenance Log ...