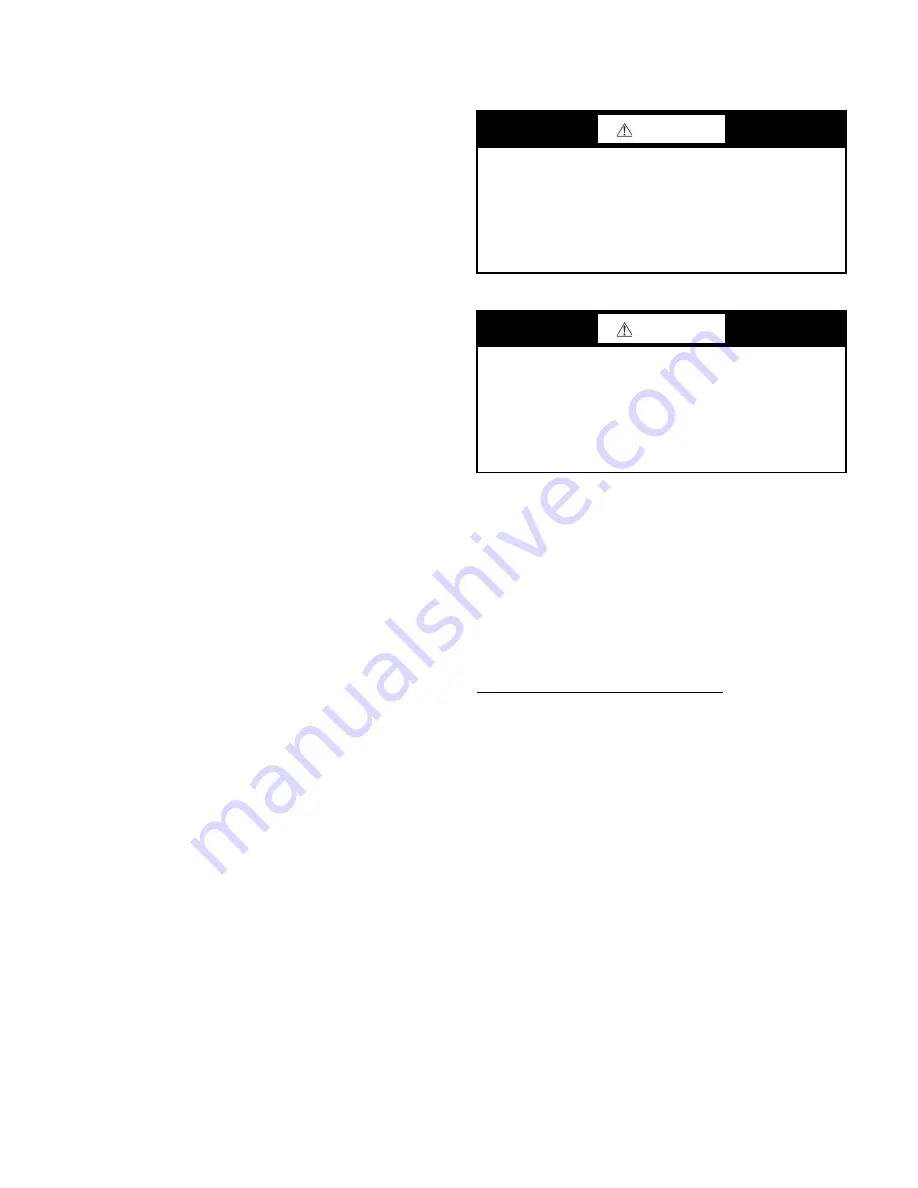
34
CADM terminal Y but no current is measured at T1, T2, T3
motor sensors); CADM relay opens and RED LED is illumi-
nated. TRIP condition maintains lockout of compressor oper-
ation until CADM is manually reset. Reset CADM by cycling
unit main power.
Complete system shutdown may be caused by loss of main
power, open compressor internal overload, open low-pressure
or high-pressure switch, or a fault detected by the CADM
logic. Compressor operation without cooling may indicate the
compressor’s ASTP feature is active; disconnect unit power
and allow compressor to cool. See Service section for further
details.
COOLING, UNIT WITH ECONOMIZER
Refer to fan coil unit installation instructions and econo-
mizer accessory installation instructions for operating se-
quences when system is equipped with accessory economizer.
HEATING
Refer to fan coil unit installation instructions and accessory
heating device installation instructions for operating sequences
in heating mode.
MAINTENANCE
These items should be part of a routine maintenance pro-
gram, to be checked every month or two, until a specific
schedule for each can be identified for this installation:
Quarterly Inspection (and 30 days after initial
start)
INDOOR SECTION
• Condenser coil cleanliness checked.
• Return air filter replacement
• Outdoor hood inlet filters cleaned
• Belt tension checked
• Belt condition checked
• Pulley alignment checked
• Fan shaft bearing locking collar tightness checked
• Condensate drain checked
Seasonal Maintenance
These items should be checked at the beginning of each
season (or more often if local conditions and usage patterns
dictate):
AIR CONDITIONING
• Condenser fan motor mounting bolts tightness
• Compressor mounting bolts
• Condenser fan blade positioning
• Control box cleanliness and wiring condition
• Wire terminal tightness
• Refrigerant charge level
• Evaporator coil cleaning
• Evaporator blower motor amperage
HEATING
• Power wire connections
• Fuses ready
• Manual-reset limit switch is closed
ECONOMIZER OR OUTSIDE AIR DAMPER
• Inlet filters condition
• Check damper travel (economizer)
• Check gear and dampers for debris and dirt
SERVICE
Refrigeration System
COMPRESSOR OIL
Servicing Systems on Roofs with Synthetic Materials
POE (polyolester) compressor lubricants are known to
cause long term damage to some synthetic roofing materials.
Exposure, even if immediately cleaned up, may cause embrit-
tlement (leading to cracking) to occur in one year or more.
When performing any service which may risk exposure of
compressor oil to the roof, take appropriate precautions to
protect roofing. Procedures which risk oil leakage include but
are not limited to compressor replacement, repairing refriger-
ants leaks, replacing refrigerant components such as filter dri-
er, pressure switch, metering device, coil, accumulator, or re-
versing valve.
Synthetic Roof Precautionary Procedure:
1. Cover extended roof working area with an impermeable
polyethylene (plastic) drop cloth or tarp. Cover an
approximate 10 x 10 ft (3.3 x 3.3 m) area.
2. Cover area in front of the unit service panel with a terry
cloth shop towel to absorb lubricant spills and prevent
run-offs, and protect drop cloth from tears caused by
tools or components.
3. Place terry cloth shop towel inside unit immediately
under component(s) to be serviced and prevent lubricant
run-offs through the louvered openings in the base pan.
4. Perform required service.
5. Remove and dispose of any oil contaminated material
per local codes.
LIQUID LINE FILTER DRIER
The factory-provided filter drier is specifically designed to
operate with Puron. Replace the filter drier with factory-au-
thorized components only with a filter drier with desiccant
made from 100% molecular sieve grade XH-11. Filter drier
must be replaced whenever the refrigerant system is opened.
When removing a filter drier, use a tubing cutter to cut the
drier from the system. Do not unsweat a filter drier from the
system. Heat from unsweating will release moisture and con-
taminants from drier into system.
FIELD REFRIGERANT ACCESS PORTS
Field service access to refrigerant pressures is through the
access ports located at the service valves (see Fig. 35 and 36).
CAUTION
UNIT DAMAGE HAZARD
Failure to follow this caution may result in equipment dam-
age.
Never charge liquid into the low-pressure side of system. Do
not overcharge. During charging or removal of refrigerant,
be sure indoor-fan system is operating. Ensure both outdoor
fan motors are running; bypass any Motormaster function.
CAUTION
UNIT DAMAGE HAZARD
Failure to follow this caution may result in equipment dam-
age.
Never charge liquid into the low-pressure side of system. Do
not overcharge. During charging or removal of refrigerant,
be sure indoor-fan system is operating. Ensure both outdoor
fan motors are running; bypass any Motormaster function.
Содержание Gemini 38AU07 Series
Страница 5: ...5 Fig 3 38AUD Z 07 14 Base Unit Dimensions ...
Страница 19: ...19 Fig 17 Typical Single Circuit Single Stage 38AUZ Wiring Diagrams ...
Страница 20: ...20 Fig 18 Typical Single Circuit Two Stage 38AUZ Wiring Diagram ...
Страница 21: ...21 Fig 19 Typical Dual Circuit Two Stage 38AUD Wiring Diagram ...
Страница 30: ...30 Fig 30 38AUZD E08 Charging Chart RTPF 7 5 Ton Dual Stage Charging Chart R 410A Refrigerant ...
Страница 46: ...46 APPENDIX C LOW AMBIENT OPTION FACTORY INSTALLED CONT Fig C Wind Baffles D K J H G F E C B A ...
Страница 48: ......
Страница 49: ......