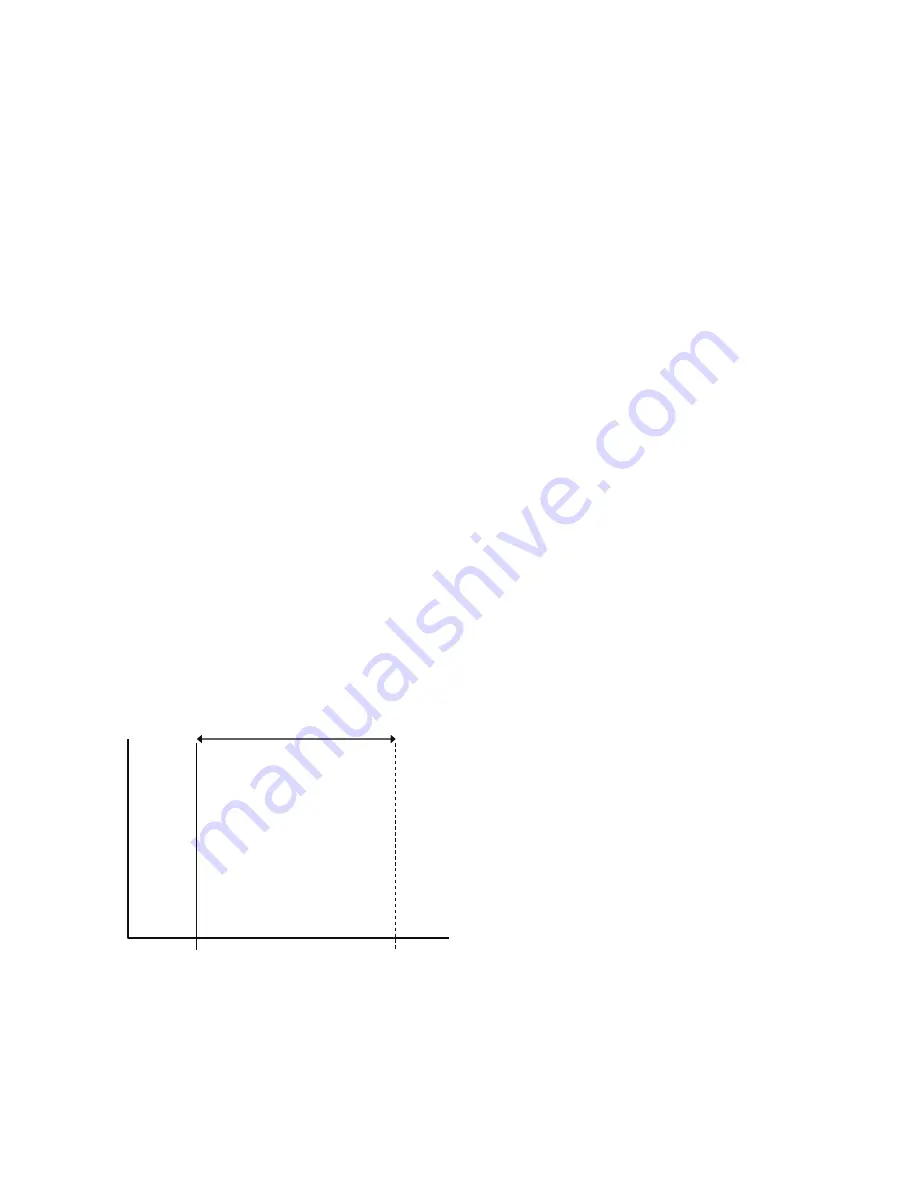
57
configured threshold. The threshold is calculated from a com-
bination of GUIDE VANE POSITION and the difference be-
tween CONDENSER PRESSURE and EVAPORATOR
PRESSURE. The operator configured data points are the MIN-
IMUM and MAXIMUM SATURATED TEMPERATURE
DIFFERENCE (Surge/HGP Delta Tsmin and Surge/HGBP
DeltaTsmax), the MAXIMUM AND MINIMUM GUIDE
VANE POSITIONS (Surge/HGBP IGVmax and Surge/HGBP
IGVmin) printed on a label fixed to the bottom of interior face
of the control panel. A line is calculated between these points.
Whenever the
ACTUAL GUIDE VANE POSITION
is on the
left side of the plotted line, the algorithm will energize the hot
gas bypass valve to falsely load the compressor. If the
ACTU-
AL GUIDE VANE POSITION
falls to the right side of the plot-
ted line by more than the
SURGE/HGBP DEADBAND,
the hot
gas bypass valve is deenergized.
If the chiller is used for other than its original design condi-
tions, instructions to adjust the Surge / Hot Gas Bypass config-
urations are found on page 79.
HGBP OPTION = 1
(VFD OPTION ENABLED) — The
HGBP is only energized if a
SURGE PROTECTION COUNT
is registered, the
ACTIVE DELTA T
falls below the
SURGE/
HGBP DELTA T
or the
VFD LOAD FACTOR
approaches 1.0
and it is not possible to increase VFD speed. The VFD speed
cannot increase when the
VFD TARGET SPEED
is equal to
VFD MAXIMUM SPEED
or if the V
FD TARGET SPEED
is
FORCED to a fixed value.
HGBP OPTION = 2
— This option energizes the
HOT GAS
BYPASS RELAY
solely based on the ACTIVE DELTA T (actu-
al temperature difference between the
LEAVING CHILLED
WATER
and
ENTERING CHILLED WATER
). Evaluation of
the
ACTIVE DELTA T
begins at the completion of ramp load-
ing. The hot gas bypass valve is energized if the
ACTIVE DEL-
TA T
is less than the
HGBP ON DELTA T
. The hot gas bypass
relay will be turned off when the
ACTIVE DELTA T
is greater
than or equal to the sum of
HGBP ON DELTA T
plus
HGBP
OFF DELTA T
See Fig. 27.
The
HGBP ON DELTA T
must be set to a value larger
than the minimum delta T to which the chiller can un-
load.
Surge Protection (Fixed Speed Chiller) —
The
PIC II monitors surge, which results in a fluctuation on the
compressor motor amperage. Each time the fluctuation in am-
perage exceeds an operator-specified limit (SURGE DELTA %
AMPS) plus a load correction factor, both SURGE COUNTS
and SURGE PROTECTION COUNTS are incremented by
one. If more than 4 SURGE PROTECTION COUNTS occur
within an operator-specified time (SURGE TIME PERIOD),
the PIC II declares an Excessive Compressor Surge Alarm
(238) and the chiller is shut down. Both SURGE COUNTS
and SURGE PROTECTION COUNTS are decreased by one if
no surges occur within the SURGE TIME PERIOD.
If a surge occurs, the guide vane position will be reduced by
10%. The guide vanes will be prevented from increasing posi-
tion until either the Surge Time Period expires causing the
SURGE PROTECTION COUNT to return to zero or the En-
tering Condenser Water Temperature decreases by 1 degree or
the Leaving Chilled Water Temperature increases by 1 degree.
If the machine has a split ring diffuser a correction its posi-
tion will be made simulatneously.
The threshold at which a current fluctuation is interpreted as
a surge can be adjusted from the OPTIONS screen. Scroll to
the SURGE DELTA % AMPS parameter and use the IN-
CREASE or DECREASE softkey to adjust the surge threshold.
The default setting is 10 %. The SURGE TIME PERIOD can
be adjusted from the OPTIONS screen. Scroll to the SURGE
TIME PERIOD parameter and use the INCREASE or DE-
CREASE softkey to adjust the time duration. The default set-
ting is 8 minutes.
SURGE PROTECTION COUNTS are displayed in the
COMPRESS screen. Both SURGE PROTECTION COUNTS
and SURGE COUNTS are displayed in the SURGPREV
screen.
Surge Prevention Algorithm with VFD —
This is
an operator configurable feature that can determine if lift con-
ditions are too high for the compressor and then take corrective
action. Lift is defined as the difference between the saturated
temperature at the impeller eye and at the impeller discharge.
The maximum lift a particular impeller wheel can perform
varies with the gas flow through the impeller and the diameter
of the impeller. With a VFD the lift capability and the position
of the surge line also vary with
ACTUAL VFD SPEED
.
The surge line constructed from the
SURGE/HGBP DELTA
T
and
SURGE/HGBP DELTA P
points is based on full load
conditions and 100% compressor speed. As
ACTUAL VFD
SPEED
is reduced, the
SURGE/HGBP DELTA P
values are
automatically reduced so that the surge line duplicates the com-
pressor lift capability at the reduced speed. If the actual operat-
ing point (lift vs. load) goes above the surge prevention line
then the controls enter
SURGE PREVENTION
mode.
Changing the
VFD SURGE LINE GAIN
adjusts the rate at
which the surge line is adjusted in response to changes in
AC-
TUAL VFD SPEED
. Increasing
VFD SURGE LINE GAIN re-
duces
the size of the
SURGE PREVENTION
“on” area.
When the controls enter
SURGE PREVENTION
mode the
first response is to increase
ACTUAL VFD SPEED
and in-
crease the lift capability of the compressor while preventing the
guide vanes from opening further. Should the compressor reach
100%
ACTUAL VFD SPEED
and still be in the surge preven-
tion region, the controls will energize the HOT GAS BYPASS
RELAY and if the
SURGE LIMIT/HGBP OPTION
is config-
ured for Hot Gas Bypass).
If load decreases while the chiller is in
SURGE PREVEN-
TION
mode the
ACTUAL GUIDE VANE POSITION
will close
but the
ACTUAL VFD SPEED
will not decrease.
ACTIVE REGION
as found on the SURGPREV screen is
based on how far into the surge prevention area that the load
HGBP
On
HGBP Off As ACTIVE
DELTA T Decreases
HGBP On As ACTIVE
DELTA T Increases
∆P
∆T
HGBP ON
DELTA T
HGBP OFF
DELTA T
HGBP
Off
LEGEND
P = (Condenser Pressure) – (Cooler Pressure)
T = (ECW) – (LCW)
Fig. 27 — 19XR Hot Gas Bypass/Surge
Prevention (Option 2)
ECW
— Entering Chilled Water
HGBP
— Hot Gas Bypass
LCW
— Leaving Chilled Water
a19-1864
Содержание AquaEdge 19XR series
Страница 69: ...69 Fig 33 19XR Leak Test Procedures a19 1625 ...
Страница 150: ...150 Fig 62 PIC II Control Panel Wiring Schematic Frame 2 3 4 and E Compressors without Split Ring Diffuser a19 1870 ...
Страница 152: ...152 a19 1871 Fig 63 PIC II Control Panel Wiring Schematic Frame 4 and 5 Compressors with Split Ring Diffuser ...
Страница 154: ...154 Fig 64 Benshaw Inc Wye Delta Unit Mounted Starter Wiring Schematic Low Voltage a19 1873 ...
Страница 161: ...161 Fig 69 Typical Low Voltage Variable Frequency Drive VFD Wiring Schematic 575 v ...
Страница 162: ...162 Fig 69 Typical Low Voltage Variable Frequency Drive VFD Wiring Schematic 575 v cont ...
Страница 163: ...163 Fig 69 Typical Low Voltage Variable Frequency Drive VFD Wiring Schematic 575 v cont a19 1880 ...
Страница 176: ...176 CONTINUED ON NEXT PAGE Fig 71 Typical Medium Voltage Variable Frequency Drive VFD Wiring Schematic cont a19 2064 ...
Страница 186: ...186 APPENDIX B LEAD LAG WIRING 19XR Lead Lag Schematic Series Cooler Flow a19 1655 ...
Страница 187: ...187 APPENDIX B LEAD LAG WIRING cont 19XR Lead Lag Schematic Parallel Cooler Flow a19 1717 ...