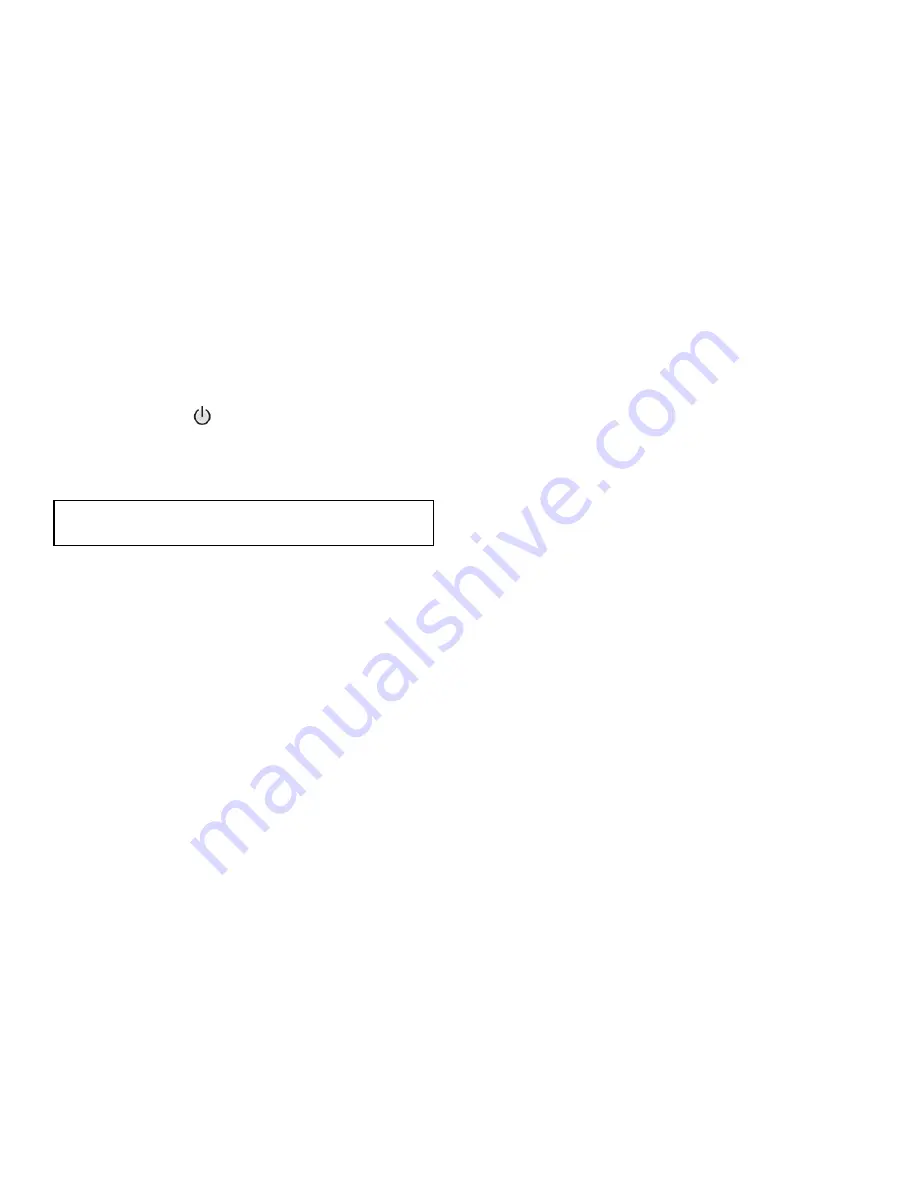
32
3. Evaporator pressure and temperature also will vary with
the design conditions. Typical pressure range will be
between 29.5 and 40.1 psig (203.4 and 276.4 kPa), with
temperature ranging between 34 and 45°F (1.1 and 7.2°C).
4. The active electrical demand setting can be overridden to
limit the compressor kW, or the pulldown rate can be
decreased to avoid a high demand charge. It may be neces-
sary to demand limit chiller. Base Demand Limit % is set at
the Setpoint Menu in the Main Menu. Demand limit is based
on chiller amps and kW is based on configured Demand
Limit Source in
Main Menu
→
Configuration Menu
→
Gen-
eral
. Pulldown rate can be based on load rate or temperature
rate and is viewed at
Main Menu
→
Configuration Menu
→
General
. Configuration of the actual ramping rate is done in
the Service Parameters Menu (
Main Menu
→
Configuration
Menu
→
Service Parameters
) where either Amps/KW Ramp
per minute or Temperature Ramp per minute can be adjusted
to slow down the chiller response.
To Stop the Chiller
The occupancy schedule starts and stops the chiller automatically
once the time schedule is configured.
The unit can be stopped manually using the HMI by pressing the
green Start/Stop icon
. The Unit Start/Stop screen is dis-
played. Press Confirm Stop. The compressor will then follow the
normal shutdown sequence as described in the Start-Up/Shut-
down/Recycle Sequence section on page 12. The chiller is now
in the OFF control mode.
If the chiller is stopped by an alarm condition,
do not restart the
chiller
until the problem is diagnosed and corrected.
After Limited Shutdown
No special preparations should be necessary. Follow the regular
preliminary checks and starting procedures.
Preparation for Extended Shutdown
The refrigerant should be transferred into the pumpout storage
tank (if supplied; see “PUMPOUT AND REFRIGERANT
TRANSFER PROCEDURES” on page 33) to reduce chiller pres-
sure and the possibility of leaks. Maintain a holding charge of 5 to
10 lb (2.27 to 4.5 kg) of refrigerant or nitrogen to prevent air from
leaking into the chiller.
For season chiller shutdown and lay-up, if the treated water is not
drained then provisions should be made to start the pumps weekly
to circulate the water and avoid corrosion. Consult the water treat-
ment company for details. Carrier is not responsible for waterside
corrosion.
If freezing temperatures are likely to occur in the chiller area, drain
the chilled water, the condenser water, and the pumpout condenser
water circuits to avoid freeze-up. Keep the waterbox drains open.
It is recommended not to store the refrigerant in the unit if below
freezing temperatures are anticipated. A nitrogen holding charge is
recommended in this case.
After Extended Shutdown
Ensure water system drains are closed. It may be advisable to
flush water circuits to remove any soft rust that may have formed.
This is a good time to brush the tubes and inspect the Schrader fit-
tings on the waterside flow devices for fouling, if necessary.
Brushing the tubes will also confirm the absence of any debris or
particulate lodged in the tubes that could result in tube failure.
Match the actual to the recorded nitrogen pressure prior to the ex-
tended shutdown to determine if a leak is present. Check the evap-
orator pressure on the HMI panel and compare it to the original
holding charge that was left in the chiller. If, after adjusting for
ambient pressure changes, any change in pressure is indicated,
check for refrigerant leaks. See Check Chiller Tightness section,
page 15.
If charge was removed, recharge the chiller by transferring refrig-
erant from the pumpout storage tank (if supplied). Follow the
Pumpout and Refrigerant Transfer Procedures section on page 33.
Observe freeze-up precautions.
Carefully make all regular preliminary and running system
checks.
Cold Weather Operation
When the entering condenser water temperature drops very low,
the operator should automatically cycle the cooling tower fans off
to keep the temperature up and tower bypass piping or condenser
water flow modulation may be required.
Manual Guide Vane Operation
It is possible to manually operate the guide vanes in order to check
control operation or to control the guide vanes in an emergency.
Manual operation is possible by overriding the target guide vane
position. Forcing the guide vanes is only possible in the Lab Test
Forced factory menu.
NOTE: Manual control overrides the configured pulldown rate
during start-up and permits the guide vanes to open at a faster
rate. Motor current above the electrical demand setting, capacity
overrides, and chilled water temperature below the control point
override the manual target and close the guide vanes. For de-
scriptions of capacity overrides and set points, see the 19MV
Controls Operation and Troubleshooting guide.
Refrigeration and Service Log
A refrigeration log (as shown in Fig. 35), is a convenient checklist
for routine inspection and maintenance and provides a continuous
record of chiller performance. It is also an aid when scheduling
routine maintenance and diagnosing chiller problems.
Keep a record of the chiller pressures, temperatures, and liquid
levels on a sheet similar to the one in Fig. 35. Automatic recording
of data is possible by exporting the data from the PIC6 controller.
Contact a Carrier representative for more information.
IMPORTANT: Do not attempt to stop the chiller by opening an
isolating knife switch. High intensity arcing may occur.
Содержание AquaEdge 19MV
Страница 49: ...49 Fig 46 SIOB...
Страница 50: ...50 Fig 47 IOB2...
Страница 51: ...51 Fig 48 19MV Auxiliary Controls Wiring...
Страница 52: ...52 Fig 49 Motor Bearing Control Board Wiring...